EOS, Metalpine to Jointly Develop Sustainable Metal Powder for Industrial 3D Printing
The future development involves Metalpine’s atomization technology coupled with EOS’ material, process and system development competence.
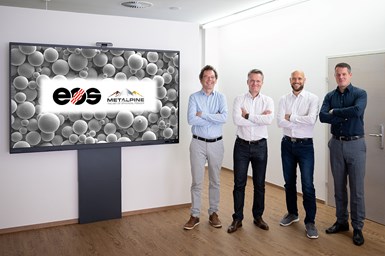
(left to right) Dr. Martin Dopler and Gerald Pöllmann from Metalpine; Sascha Rudolph, EOS and Andreas Rohrseitz, Hightech Metal Investment (Photo Credit: Metalpine)
EOS has acquired a stake in Metalpine, a manufacturer of metal powders for additive manufacturing (AM), which is based in Graz, Austria. The aim is to work more closely in the joint development of innovative and sustainable metal powders.
The future development involves Metalpine’s new atomization technology coupled with EOS’ material, process and system development competence. The two companies say they are well positioned to offer users of AM both sustainable and economically efficient powder products in the future, so that customers can grow successfully without wasting valuable resources unnecessarily.
Metalpine says its atomization technology, which is specially designed for industrial 3D printing, makes it possible to produce new types of powder with optimum efficiency in powder production and in the 3D printing process. With this minority stake participation, both companies are said to be better able to contribute to the sustainability of AM as it applies to raw material, electricity and gas consumption in the traditionally energy-intensive part of metal powder production.
The founders of Metalpine, a subsidiary of the High Tech Metal Investment (HTM Invest) Group, have decades of experience in the manufacture of metallic products such as powder. The recently opened production center in Graz is said to meet the highest demands in terms of operating efficiency and environmental protection, and enables efficient scaling with consistently high production quality.
“We can now offer our customers even more powerful and sustainable solutions in the interplay between our industrial 3D printing process and the metal powder production used for this purpose,”says Sascha Rudolph, EOS senior vice president metal materials.
The Metalpine process is said to enable a whole new dimension of flexibility and is consistently geared toward the application field of 3D printing. “The systems are particularly compact, can be quickly set up for new materials and are so low in emissions that they can also be operated in metropolitan areas without hesitation,” Rudolph adds.
Related Content
-
3D Printing Brings Sustainability, Accessibility to Glass Manufacturing
Australian startup Maple Glass Printing has developed a process for extruding glass into artwork, lab implements and architectural elements. Along the way, the company has also found more efficient ways of recycling this material.
-
Copper, New Metal Printing Processes, Upgrades Based on Software and More from Formnext 2023: AM Radio #46
Formnext 2023 showed that additive manufacturing may be maturing, but it is certainly not stagnant. In this episode, we dive into observations around technology enhancements, new processes and materials, robots, sustainability and more trends from the show.
-
Next-Gen Horse Trailers to Be Built With Robotic 3D Printing
Double D Trailers is currently developing a prototype horse trailer that will be made with large-format additive manufacturing. The technology brings potential benefits for labor, weight and design features to this subset of recreational vehicles.