Where Blockchain and 3D Printing Converge, Distributed Manufacturing Can Thrive
Decentralizing production through additive manufacturing can bring numerous benefits, but these can only be realized through trust. VeriTX is building a platform to secure a trusted digital supply chain for aerospace and beyond.
Share
“We went to centralized manufacturing models because of cost, but also because the factory model allows you to keep control,” says James Regenor, a retired Air Force pilot and founder of VeriTX. “In order to take things outside of the traditional four walls of the factory, we have to find a way to trust.”
As production has become centralized in pursuit of cost savings and control, supply chains have stretched to the point that trust has been degraded. Restoring it will be the key to manufacturing’s future, to new digital supply chains that will bring production out of the four factory walls and onto aircraft carriers, oil rigs, even spacecraft. His company VeriTX was founded to be a new, secure and trustworthy bridge between designers, manufacturers and buyers, utilizing blockchain technology and additive manufacturing (AM) to securely move data and distribute manufacturing wherever it is needed.
Trust Built on Blockchain
Regenor is well situated to build this bridge, having been on both sides of it. As a U.S. Air Force pilot and commander of a logistics organization, he experienced firsthand the delays and hurdles of the conventional aerospace supply chain. “Military aircraft are held hostage by long supply chains,” he says. “It can take 87 weeks to receive a forging or casting, and then another 4 to 6 months of lead time to actually get a needed aircraft part.”
Upon leaving the Air Force, Regenor joined Moog, the aerospace OEM that for a time owned 3D printing service bureau Linear Mold (Linear AMS). As a leader of Moog’s aircraft military aftermarket division, he became familiar with additive manufacturing technology and saw its potential for delivering parts and spares on a more rapid timeline. In 2018, Regenor left Moog to pursue the project that would eventually become VeriTX. The company is now close to launch, with multiple proof-of-concept successes under its belt.
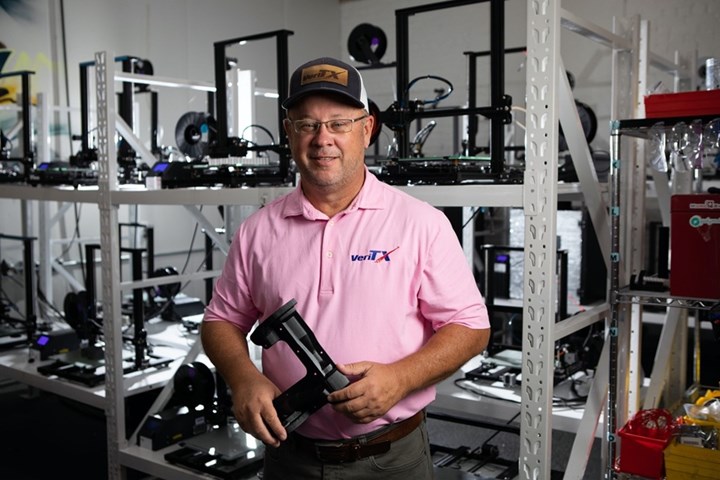
Production became centralized because of cost and control, but blockchain can be the key to making trusted distributed manufacturing a reality, according to Col. James Allen Regenor, U.S. Air Force (retired) and founder of VeriTX Corp. Photo Credit: Stephan Gabris for VeriTX Corp.
VeriTX's product is a B2B system for validating parts and suppliers when OEMs and distant manufacturers are strangers to one another. The company essentially provides a supply chain marketplace that allows OEMs to securely upload digital rights-managed (DRM) part files to an online hub where buyers with the right qualifications and manufacturing capacity can purchase and download them. Blockchain technology (provided through a partnership with Algorand) protects the provenance of the part designs, while biometrics secure them on the manufacturing side; only a known and identified recipient can receive the digital asset. Each produced part also has a “digital fingerprint” in the form of an embedded tag or printed code associated with the blockchain hash to provide proof against counterfeiting. Thus, trust can be maintained all along the supply chain from design through finished part, and it can be maintained throughout a widely distributed network of suppliers working in parallel.
The VeriTX platform will list only qualified parts and will only allow them to be made by exactly the right manufacturer using the proper material and equipment. When I spoke to Regenor at the beginning of October 2020, he said the company was just a few months away from fielding organic orders on the platform.
Launching with Aerospace
To start, VeriTX is focused on 3D printable aerospace parts. The aerospace industry has much to gain from this secure, digital supply chain solution, not only as a way of shortening lead times and distributing production but also as a method for combating counterfeit parts. Regenor says that up to $3 billion of counterfeit parts are installed on aircraft every year; until recently they have been fairly simple parts, but the advance of 3D printing technology potentially opens the door for more complex counterfeits. At least 30% of BAE Systems’ next-generation Tempest fighter jet will be 3D printed, for example. As the aerospace industry embraces AM adoption for its design and lightweighting benefits, it becomes increasingly important to have traceability for these components.
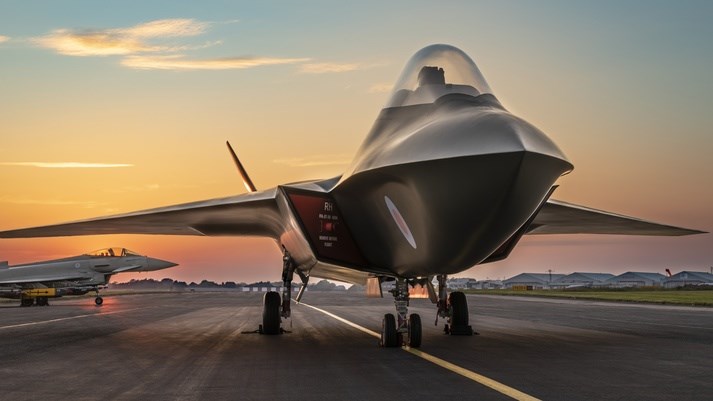
30% of the parts used in the next generation Tempest fighter jet from BAE Systems will be 3D printed. As the technology becomes more prolific in aerospace, so does the need to prevent counterfeit 3D printed parts. Photo Credit: BAE Systems
VeriTX will bring that traceability to military and airline customers, enabling distributed manufacturing and digital, additive manufacturing of needed parts on an accelerated timeline. Rather than wait for a forging, and again for machining, and yet again for shipping, the VeriTX platform would allow a military base, for example, to buy the DRM file for a needed part, 3D print it on-site with the specified parameters and material, and install it in a matter of days or even hours rather than months. The same process can be applied to commercial airlines, too; in one proof-of-concept study VeriTX was able to deliver a replacement part for a business class seat on a commercial plane that would have resulted in a loss of up to $30,000 in revenue from an unoccupied seat for multiple trip legs.
“We were able to seed the digital part in their supply chain in Singapore, and they pushed it to us in Los Angeles. We made the part on premises and it was waiting for the airplane when it landed. All that from order to delivery took one hour,” Regenor says. “It wasn’t that complex, but if you start thinking in these terms you can see the kind of outcomes that are possible.”
As this example illustrates, manufacturing in situ from a digital file significantly reduces the amount of time between an order being placed to having a part in hand. It also alters the role and business of the original equipment manufacturer. In a distributed manufacturing model like the VeriTX platform, OEMs will continue to create and maintain ownership of their part files, but they don’t need to also maintain conventional levels of equipment, floorspace, inventory and shipping infrastructure. When the distributed manufacturing method is digital, the need for tooling goes away too. The costs of traditional manufacturing thus move downstream or disappear altogether.
“The cost of production and the cost of raw materials are consumed right at impact, so the OEM is not creating physical product and putting it on the shelf,” Regenor says. “It’ll change that balance.” This is not e-commerce where buyers order and receive a physical product, he says, but “d-commerce” — digital commerce, where digital assets change hands rather than physical goods.
In a d-commerce supply chain, the manufacturing capacity can be owned by the part user, or perhaps a nearby service provider, rather than the OEM. Material can be purchased by that user in small lots as needed, and production takes place on demand. Manufacturing happens either onsite or very near to the point of use, so shipping is greatly reduced or avoided altogether.
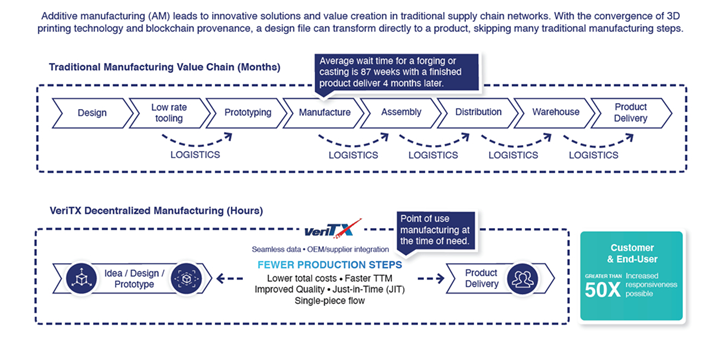
VeriTX’s decentralized manufacturing model reduces production steps and wait time versus the traditional manufacturing value chain. Image credit: VeriTX Corp.
Initially the manufacturing capacity available to VeriTX users will be exclusively 3D printing, but Regenor’s vision is eventually to give buyers choices that allow them to best solve the problem at hand. A future VeriTX user looking for a replacement aircraft component might be presented with options to buy a new machined part to be made on demand, a used version in stock, or a 3D printable STL file. Each of these options would likely come with a tradeoff. The new machined part might take a long time to make, maybe longer than the aircraft can wait. The used part may be cheapest, but might be stored abroad, resulting in a long shipping time and potential delays at customs. A 3D printable part made on site would be the fastest solution, but likely more expensive than the other two. The choice would depend upon the end user’s priority.
Trustworthy Parts Through a Digital Supply Chain
Regardless of the option chosen, the parts sold through this platform will be trustworthy — which gets at the long-term goal for VeriTX. Rather than simply a part marketplace, VeriTX will become a digital database for parts and complete systems. For each part or product that is reverse engineered, designed or otherwise added to the platform, a digital twin is created to follow its full lifecycle. By digitizing and twinning parts at every opportunity, “We’re able to start collecting data, to create data and knowledge that didn’t exist before,” he says.
The potential impact of this knowledge creation is great; with digital twins, VeriTX can move into the realm of predictive and prescriptive maintenance. It can create digital maintenance records to help militaries and airlines maintain their fleets and solve problems before something goes wrong. It can assist repair technicians in identifying failing components and ordering replacements. The system can even ease reverse forensics, providing a clear trail of data that will speed and simplify root-cause analysis when problems do occur.
“With the convergence of all these technologies … we can form a trusted digital supply chain. The world becomes borderless.”
VeriTX is preparing for launch in early 2021. Moog is one of the first 27 partners on the platform and will be providing its aerospace part catalog for purchase through the platform; other ecosystem partners include Northern Block, Airspace Technologies, Hummingbird Aero, and AM companies such as Innosek, CALT Dynamics and Accelerate3D. Aerospace will be the focus at first, but in time the platform will expand to serve the medical industry, industrial parts and other highly regulated markets. VeriTX’s digital supply chain concept could even be applied for space travel, allowing astronauts to produce needed parts and equipment with the same confidence as manufacturers based on earth.
“Commerce, culture and government used to spring up at the world’s rivers, but now those waterways have been replaced by ‘data rivers’,” Regenor says. “With the convergence of all these technologies — machine learning, 3D printing, blockchain, digital rights — we can form a trusted digital supply chain. The world becomes borderless.”
Related Content
Seurat: Speed Is How AM Competes Against Machining, Casting, Forging
“We don’t ask for DFAM first,” says CEO. A new Boston-area additive manufacturing factory will deliver high-volume metal part production at unit costs beating conventional processes.
Read MoreVariable Resistance Valve Trim Achieves Lead Time Reduction Through AM: The Cool Parts Show #69
Baker Hughes is realizing shorter lead times and simplified manufacturing through powder bed fusion to produce valve trims previously assembled from many machined metal parts.
Read MoreBig Metal Additive: The Difference Between a Shape and a Part Is Quality
Preparing to scale directed energy deposition to ongoing full production is not a technological challenge: DED is ready. But it is an organizational challenge, says the company founder. Here is what it means to implement a quality system.
Read MoreThis Year I Have Seen a Lot of AM for the Military — What Is Going On?
Audience members have similar questions. What is the Department of Defense’s interest in making hardware via 3D printing over conventional methods? Here are three manufacturing concerns that are particular to the military.
Read MoreRead Next
What Is the Role for Additive Manufacturing in Aircraft Structural Components?
Spirit AeroSystems recently began installing the Boeing 787’s first titanium structural component to be made through AM. The part is not critical but also not minor. I spoke with manufacturing leaders at Spirit about the meaning of the part and the way forward for additive in aircraft structures.
Read MoreJabil, Fictiv Partnership Addresses Capacity Challenge of Distributed Manufacturing via 3D Printing
With additive manufacturing, production can be relocated quickly and performed at whatever site is ideal. But what about the capacity waiting for this shift? Relationship gives global producer access to “transactional” 3D printing.
Read MoreProfilometry-Based Indentation Plastometry (PIP) as an Alternative to Standard Tensile Testing
UK-based Plastometrex offers a benchtop testing device utilizing PIP to quickly and easily analyze the yield strength, tensile strength and uniform elongation of samples and even printed parts. The solution is particularly useful for additive manufacturing.
Read More