Admaflex300 Ceramic, Metal 3D Printer Offers 12 million Pixels Per Single Layer
It is said the printer can greatly increase the accuracy, throughput and efficiency in high-performance technical ceramic and metal 3D printing.
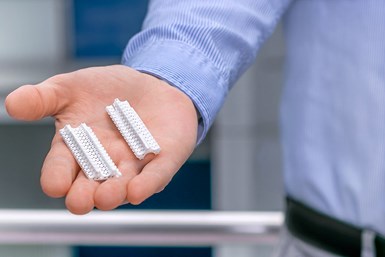
3D printed zirconia fluid break for nuclear applications, printed with pixel resolution of 50 µm. Photo Credit: Hilgenberg Ceramics
Admatec’s Admaflex300 printer comes with 12 million pixels per single layer for dramatically increased accuracy, throughput and efficiency in high-performance technical ceramic and metal 3D printing. Its lithography-based additive manufacturing (AM) technology enables ceramic and metal printing on one machine and higher resolutions, the company says.
The machine combines ceramic and metal 3D printing to produce complex shapes directly from a CAD file, without the need for a mold, with comparable material properties as traditionally produced ceramics, when using the appropriate 3D printing technology, materials and furnaces. Compared to direct laser-based printing techniques, lithography-based ceramic and metal printing is said to enable the finest details and highest resolution. After sintering, smooth and stress-free end-use parts are obtained — which usually do not require postprocessing, the company says.
The machine is said to combine advancements in the latest projection technologies. The lithography-based ceramic and metal AM technique uses Digital Light Processing (DLP) technology, which cures a next layer of a full build platform in a few seconds. In combination with tape casting to deposit a new slurry layer, it enables users to increase printing speeds up to 300 layers per hour.
The company says the machine can be tailored to meet the needs of the customer, with different projection sizes and resolutions. Currently, the Admaflex300 is available with pixel resolution of 40 µm in combination with a build platform of 202 × 102 mm, meaning more than 12 million pixels in one single layer to greatly increase the throughput and efficiency in highly accurate technical ceramic and metal 3D printing.
It is said the machine is well suited for R&D and material development for users who want to only use the smallest amount of material for printing small parts. For users looking to scale up to maximum productivity, the machine is said to offer more than three times the production output of a smaller machine that only has a 102 × 64 mm platform. It can also come with specifications similar to the Admaflex130 machine, enabling users to upgrade later on to the full capabilities and specifications of the larger machine.
Related Content
-
Video: AM for Harder, Longer-Lasting Brake Discs
Additive manufacturing is being applied to limit automotive brake dust. For a major automaker, Etxetar and Talens are developing a production-speed directed energy deposition system to give brake discs a precise layer of wear-resistant carbide.
-
8 Cool Parts From Formnext 2023: The Cool Parts Show #65
New additive manufacturing technologies on display at Formnext were in many cases producing notable end-use components. Here are some of the coolest parts we found at this year’s show.
-
BMF Receives FDA Clearance for UltraThineer Dental Veneer Material
The zirconia materials are now qualified for use in the production of the world’s thinnest cosmetic veneers, which require significantly less tooth preparation or grinding, thereby preserving more of the patient’s natural enamel.