BMF Receives FDA Clearance for UltraThineer Dental Veneer Material
The zirconia materials are now qualified for use in the production of the world’s thinnest cosmetic veneers, which require significantly less tooth preparation or grinding, thereby preserving more of the patient’s natural enamel.
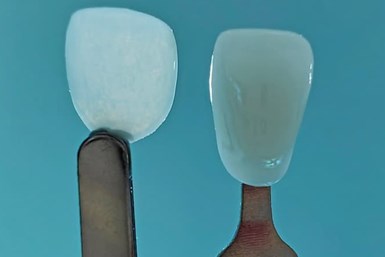
UltraThineer and regular veneer. Source: Boston Micro Fabrication
Boston Micro Fabrication (BMF), a provider of advanced manufacturing solutions for ultrahigh precision applications, has received U.S. Food and Drug Administration (FDA) 510(k) clearance for its UltraThineer material used to create what it says is the world’s thinnest cosmetic dental veneer. The company says these dental veneers are thinner and smaller than what’s currently on the market, helping patients have a better experience and reducing the prep time for dentists.
The 3D printed veneers use projection microstereolithography (PµSL), a technology that enables greater resolution, accuracy and precision to custom manufacture veneers that are three times thinner than traditional veneers. The UltraThineer veneers requires significantly less preparation for dental professionals, enabling preservation of the patient’s original enamel with a more realistic final appearance.
“We are thrilled to hear that the UltraThineer veneer has received FDA 510(k) clearance,” says Dany Karam, Advanced Dental Technologies president. “This is a significant milestone for our industry as having the ability to 3D print veneers in zirconia is a game changer for dental technology. This breakthrough allows us to offer patients high-quality veneers that require minimum prepping. This is just the beginning of our journey to revolutionize dental care, and we look forward to working with BMF to begin offering the UltraThineer to dental patients across the country.”
According to the company, UltraThineer veneers are the world’s thinnest veneers and feature advanced material, a production workflow and a finishing process to deliver more comfortable and less invasive options in cosmetic dentistry. Developed in collaboration with Peking University, dental labs can now offer this highly precise alternative to traditional veneers for dental practices across the U.S., powered by BMF’s unique, microscale printing technology. Additive manufacturing, or 3D printing, is already proven across multiple dental applications including orthodontic aligners, mouth guards, drill guides and dentures due to the need for on-demand, personalized custom solutions.
“After refining this process, technology and material for the last year, we’re incredibly encouraged by the FDA’s expedient review of the UltraThineer material so we can quickly bring it to consumers looking for a more streamlined veneer solution,” says Professor Sun Yuchun, Peking University School of Stomatology. “With the same durability as traditional veneers, dental labs across the U.S. can now deliver an improved veneer option that isn’t as invasive for the patient, minimizing tooth reduction and improving the overall appearance of teeth.”
BMF has begun to partner with dental labs in the U.S. and expects to have the products commercially available in the second half of 2024. The UItraThineer material represents the latest innovation delivered by BMF as the company looks to explore and establish new applications where its technology can reduce production time and cost.
“We’ve continued to innovate our solutions and explore end-use applications that can be uniquely enabled by the PµSL process in dentistry and the life sciences. We are very pleased with our recent 510(k) clearance and the progress we’ve made towards commercializing this technology to offer more options for patients considering cosmetic dentistry,” says John Kawola, BMF CEO-Global.
In addition, BMF is developing complementary cosmetic dentistry offerings in international markets to support both direct-to-patient and provider-enabled access to thinner veneers.
Related Content
Ultra-Complex 3D Printed Scaffolds Enable Cell Growth: The Cool Parts Show #70
Perhaps the ultimate surface-area challenge is in bioengineering: creating structures that can grow sufficient cells within a compact volume to be effective for leading-edge medical treatments. The Southwest Research Institute develops bioreactor scaffolds that could only be made using 3D printing.
Read MoreActivArmor Casts and Splints Are Shifting to Point-of-Care 3D Printing
ActivArmor offers individualized, 3D printed casts and splints for various diagnoses. The company is in the process of shifting to point-of-care printing and aims to promote positive healing outcomes and improved hygienics with customized support devices.
Read More8 Cool Parts From Formnext 2023: The Cool Parts Show #65
New additive manufacturing technologies on display at Formnext were in many cases producing notable end-use components. Here are some of the coolest parts we found at this year’s show.
Read MoreFDA-Approved Spine Implant Made with PEEK: The Cool Parts Show #63
Curiteva now manufactures these cervical spine implants using an unusual 3D printing method: fused strand deposition. Learn how the process works and why it’s a good pairing with PEEK in this episode of The Cool Parts Show.
Read MoreRead Next
3D Printed Polymer EOAT Increases Safety of Cobots
Contract manufacturer Anubis 3D applies polymer 3D printing processes to manufacture cobot tooling that is lightweight, smooth and safer for human interaction.
Read MoreProfilometry-Based Indentation Plastometry (PIP) as an Alternative to Standard Tensile Testing
UK-based Plastometrex offers a benchtop testing device utilizing PIP to quickly and easily analyze the yield strength, tensile strength and uniform elongation of samples and even printed parts. The solution is particularly useful for additive manufacturing.
Read MoreAlquist 3D Looks Toward a Carbon-Sequestering Future with 3D Printed Infrastructure
The Colorado startup aims to reduce the carbon footprint of new buildings, homes and city infrastructure with robotic 3D printing and a specialized geopolymer material.
Read More