Roboze’s ARGO 1000 Fabricates Large Parts Using Super Polymers, Composites
Printer uses more sustainable, high-performing super polymers and composites such as PEEK, Carbon PEEK and ULTEM AM9085F to reduce the strain on global supply chains.
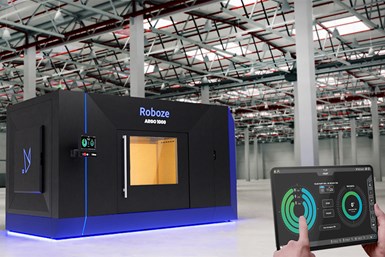
Roboze’s ARGO 1000
Roboze’s ARGO 1000 is one of the world’s first 3D printers with a heated chamber designed to produce large-scale parts with super polymers and composites for industrial applications. The printer can offer large, customizable, industrial parts and on-demand production at scale, the company says.
The system is said to fabricate lighter, higher quality components for a variety of industries, including aerospace, energy, transportation, medical technology and automotive. Using more sustainable and high-performing super polymers and composites (such as PEEK, Carbon PEEK and ULTEM AM9085F), Roboze can help reduce the strain on global supply chains, and replace metal parts and mission-critical components for extreme applications.
The ARGO 1000 production system includes a heated and controlled working chamber with printing dimensions equal to 1 m3 (39.37" × 39.37" × 39.37"). Process control is on par with CNC machining and injection molding, resulting in process accuracy and repeatability equal to 99.96% of parts obtained on multiple machines, the company says. The system is said to offer a dramatic reduction in production time with its comprehensive monitoring capabilities, remote diagnostic tools and predictive maintenance.
The system features software parameters and constant remote updates for continuous performance improvements. Users can achieve certification for every piece produced via a comprehensive print log system that monitors all parameters, temperatures and factors involved to create a digital model of the part produced. It offers printing capability using more than 10 materials. A double extruder enables the system to process soluble and breakaway supports. The loading system can handle up to 17.6 lbs/8kg of material with automatic material change in case material ends during the printing process.
The printer also includes a beltless system for achieving mechatronic handling accuracies up to 10 µ; automatic self-leveling floor; and a head self-calibration system.
Related Content
-
Aircraft Ducts 3D Printed in Composite Instead of Metal: The Cool Parts Show #68
Eaton’s new reinforced PEKK, tailored to aircraft applications, provides a cheaper and faster way to make ducts compared to formed aluminum.
-
3 Unique Elements of LFAM to Consider in Design
While similar to desktop fused filament fabrication (FFF), large format additive manufacturing (LFAM) in polymer composite poses several unique challenges as a result of its scale.
-
Next-Gen Horse Trailers to Be Built With Robotic 3D Printing
Double D Trailers is currently developing a prototype horse trailer that will be made with large-format additive manufacturing. The technology brings potential benefits for labor, weight and design features to this subset of recreational vehicles.