Holo Expands Material Options for High-Resolution, High-Throughput Metal Additive Manufacturing
Expanded PureForm MicroAM materials options include copper, stainless steels and other metals.
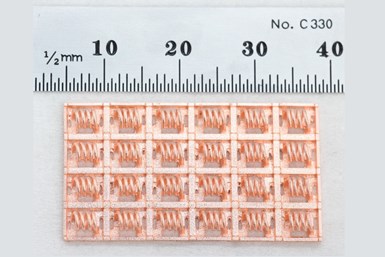
Micro inductor coils printed in a 24-piece array — 20 such arrays can be printed simultaneously on one Holo PureForm printer.
Holo, a Silicon Valley-based metal additive manufacturing (AM) company and spinout of Autodesk , has expanded its PureForm MicroAM materials to include copper, stainless steels and other metals. PureForm MicroAM is a high resolution and high throughput metal AM platform, capable of producing parts with features less than 50 μm. It is said to enable a wide range of applications, including electrical components, jewelry, and medical and dental devices.
The platform is designed to support volume production for complex parts with fine features, enabling customers to manufacture parts at a lower cost and produce geometries that cannot be made any other way. PureForm MicroAM has offered new capabilities for customers in the electronics industry, producing fine-featured micro inductors coils, built with 400 µm strands (Figure 1) and in high-end custom jewelry, the company says.
Leveraging the design freedom of AM and the fine features of PureForm are said to enable users to create unique, custom pieces with high resolution and surface quality that couldn’t be made using other manufacturing processes. A variety of AM applications have been enabled by PureForm MicroAM, including stainless steel biopsy scoops used in medical applications with sharp point features down to 20 µm and dental abutments with printed functional threads that hold a 200 µm pitch.
The company says its platform offers new capabilities to support a variety of new MicroAM applications — from surgical equipment and dental, to microelectronics, microrobotics, consumer electronics and jewelry.
PureForm was launched earlier in 2021 to produce high-performance pure copper parts directly for customers using its high-resolution, high-throughput technology. PureForm MicroAM is ramping up at Holo’s 20,000-square-foot production facility in the San Francisco area, where it has capacity to produce tens of thousands of parts per month.
Related Content
-
VulcanForms Is Forging a New Model for Large-Scale Production (and It's More Than 3D Printing)
The MIT spinout leverages proprietary high-power laser powder bed fusion alongside machining in the context of digitized, cost-effective and “maniacally focused” production.
-
3D Printed Titanium Replaces Aluminum for Unmanned Aircraft Wing Splice: The Cool Parts Show #72
Rapid Plasma Deposition produces the near-net-shape preform for a newly designed wing splice for remotely piloted aircraft from General Atomics. The Cool Parts Show visits Norsk Titanium, where this part is made.
-
Video: 5" Diameter Navy Artillery Rounds Made Through Robot Directed Energy Deposition (DED) Instead of Forging
Big Metal Additive conceives additive manufacturing production factory making hundreds of Navy projectile housings per day.