Dyndrite, MIMO Technik, Astro Collaborate on Machine, Material Qualification for 3D Metal Printing
The companies chose to collaborate on the development of the Mastro process in order to streamline and automate a closed-loop source for additive production and qualification.
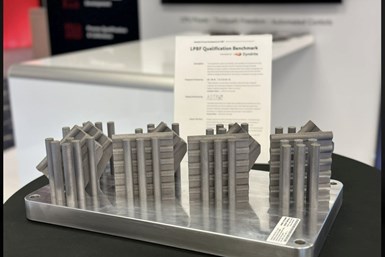
Build plate showcases a qualification build studying material defect formation using parametrically defined and varied parameters. Created by MIMO Technik Inc. with testing by Astro Mechanical Testing Laboratory and printed on SLM Solutions’ 500 3D metal machine. Photo Credit: Dyndrite
Dyndrite is collaborating with MIMO Technik and Astro Mechanical Testing Laboratory to accelerate machine and material qualification for 3D metal printing. The collaboration brings together the expertise of all three companies to offer specialized solutions that support critical programs for aerospace and defense.
Dyndrite’s GPU-accelerated computation engine is designed to create next-generation digital manufacturing hardware and software, while MIMO Technik develops manufacturing solutions in the additive manufacturing (AM) space for aerospace, rocketry, defense and motorsport clients. Astro is known for executing mechanical and metallurgical testing for additive materials developed for spaceflight hardware, launch vehicles and satellites.
MIMO Technik and Astro chose to collaborate with Dyndrite on the development of the Mastro process in order to streamline and automate a closed-loop source for additive production and qualification. Mastro is MIMO Technik and Astro’s internal proprietary parameter development process that involves experiments to determine values for all variables that influence the SLM process.
Together, through the Mastro process, the organizations have qualified materials for industry leaders such as Boeing, Lockheed Martin and Northrop Grumman. Qualified material is now in production for fracture-critical hardware such as landing gear, propulsion systems, payload structures and defense applications.
MIMO Technik and Astro plan to leverage Dyndrite’s software tools to codify Mastro build recipes to ensure repeatable quality and traceability. Automated build layout, serialization and reporting are all necessary for a scalable qualification process for machines, materials and process parameters. Currently, MIMO Technik exclusively uses 10 SLM Solutions L-PBF machines due to their open architecture, continued support and philosophy for advancement.
“The business case for being an open architecture metal 3D solution provider is at its core about making our customers more successful,” says Garett Purdon, vice president of sales - Americas at SLM Solutions. “It’s about creating choices for our customers and removing arrogance. We’re not a jack-of-all-trades, but a true master of one. We acknowledge that others can add additional value.”
According to the partners, parameter development and qualification can be a tedious and time-consuming process. “Dyndrite’s tools allow users to rationally explore the parameter space of interest using their own algorithms while building upon provided tools, says Steve Walton, head of product at Dyndrite. “Our APIs are designed to support the user in these studies and algorithmically provide the build and toolpath pedigree to ensure data can be used in research, qualification and production environments. The build and toolpath automation provided allows engineers to explore the solutions to new process problems, instead of spending energy on manual, error prone data entry.”
The Dyndrite-MIMO Technik collaboration aims to serve as an model for qualifying AM processes for laser powder bed fusion (LPBF) machines. Dyndrite has unveiled its first end-user AM application, Dyndrite Materials and Process Development for LPBF. This GPU-based 3D application was designed for materials and process engineers developing new metal alloys and parts for laser-based 3D metal printing. It takes advantage of the features within Dyndrite’s Accelerated Computation Engine (ACE), including the ability to perform 3D geometric queries in order to detect and optimize for difficult geometric features such as domes, cantilevers and thin walls.
It also provides engineers with the ability to improve build rates by easily working with multiple layer heights and parameter settings, improves part quality through the use of rational APIs for distributing the process and developing toolpath trajectories, and deploying support strategies that deliver maximum flexibility. Customers using Dyndrite can also easily create shareable build recipes (Python) that provide all the necessary information required to recreate a build and drive a variety of 3D metal printers, including Aconity, EOS, Renishaw, SLM and others.
“Scaling digital additive manufacturing to an industrial level is the next step for strategic aerospace and defense infrastructure,” says Jonathan Cohen, CEO and co-founder of Mimo Technik. “Dyndrite is the platform we are using to build that reality. Empowering our engineers from rapid material development to creating qualified aerospace workflows for our growing AM facility.”
Astro says it has characterized dozens of materials through the Mastro process over the last two years. “Our partnership with Dyndrite will accelerate the efforts to streamline testing efficiencies in order to get customers to production sooner,” says Humna Khan, CEO and co-founder of Astro.
Dyndrite and MIMO Technik will further partner to develop advanced scan path strategies for productivity and quality on SLM machines for a variety of alloys used by MIMO Technik’s customers.
- Read about Dyndrite joining ASTM to provide AM reference data. The collaborative effort aims to create shareable reference datasets that drive consistency across the industry, accelerating qualification and adoption of metal additive manufacturing.
- Learn about another Dyndrite collaboration, this time with AMFG for cross-platform 3D metal automated production. AMFG powered by Dyndrite is an integrated solution that is said to unlock the full potential of metal 3D printing by bringing order-to-part automation, eliminating bottlenecks and streamlining the entire production process for increased efficiency and cost savings.
Related Content
Jeol’s Electron Beam 3D Printer Meets Aerospace Qualification Standard
The company says that meeting the AMS7032 operational qualification standard ensures manufacturers that Jeol’s JAM-5200EBM is capable of producing aerospace-grade material with stable performance and meets all material specification requirements.
Read MoreInspection Method to Increase Confidence in Laser Powder Bed Fusion
Researchers developed a machine learning framework for identifying flaws in 3D printed products using sensor data gathered simultaneously with production, saving time and money while maintaining comparable accuracy to traditional post-inspection. The approach, developed in partnership with aerospace and defense company RTX, utilizes a machine learning algorithm trained on CT scans to identify flaws in printed products.
Read MoreAdditive Manufacturing at NASA (Part 2): AM Radio #52
In this follow-up podcast episode on additive manufacturing at NASA, Dr. Tim Simpson joins us to discuss how the organization thinks about AM overall, and its role in advancing additive alongside and in service of commercial industry.
Read MoreA Framework for Qualifying Additively Manufactured Parts
A framework developed by The Barnes Global Advisors illustrates considerations and steps for qualifying additively manufactured parts, using an example familiar to those in AM: the 3D printed bottle opener.
Read MoreRead Next
Crushable Lattices: The Lightweight Structures That Will Protect an Interplanetary Payload
NASA uses laser powder bed fusion plus chemical etching to create the lattice forms engineered to keep Mars rocks safe during a crash landing on Earth.
Read More3D Printed Polymer EOAT Increases Safety of Cobots
Contract manufacturer Anubis 3D applies polymer 3D printing processes to manufacture cobot tooling that is lightweight, smooth and safer for human interaction.
Read MoreProfilometry-Based Indentation Plastometry (PIP) as an Alternative to Standard Tensile Testing
UK-based Plastometrex offers a benchtop testing device utilizing PIP to quickly and easily analyze the yield strength, tensile strength and uniform elongation of samples and even printed parts. The solution is particularly useful for additive manufacturing.
Read More