DyeMansion Expands Series of AM Postprocessing Systems
Powershot Performance Series is designed for next-level blasting systems for postprocessing cleaning and surfacing.
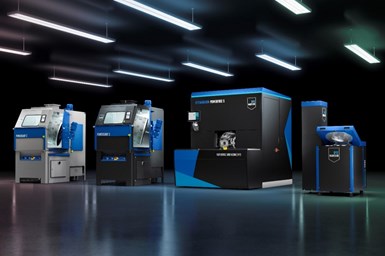
The Dual, Powershot C and S systems all include features for quality assurance, traceability, connectivity and automation, resulting higher throughput in less time.
DyeMansion expands its print-to-product workflow with three systems, including the Powershot Performance series, a new generation of the Powershot C cleaning and S surfacing models, and the PolyShot Cleaning process, which works with both Powershot models.
The Powershot Dual Performance model combines both cleaning and surfacing processes in one blasting system, purpose-built for the factory and high-volume production. It is designed for demanding additive manufacturing (AM) applications. It is also the first system with the DyeMansion Multi Belt, an integrated wide-troughed belt, making it capable of processing full-sized build jobs. The open system design also enables alternative automation options such as robots, conveyor belts and more.
The company says the dual model reduces process time up to 20% and increases load capacity 150%, making it incredibly efficient. The compact design saves users up to 60% in workspace to offer high performance and maximum efficiency with a small workspace.
The classic Powershot C and S models are entry-level systems which offer improved ease of use, next-level part processing, ensured dust retention and simplified troubleshooting.
The Dual, Powershot C and S systems all come equipped with Siemens’ automation technology and also include features for quality assurance, traceability, connectivity and automation, resulting higher throughput in less time.
The PolyShot Cleaning process features plastic blasting media to gently remove powder without damaging parts or leaving mineral dust on the surface. The process works with the latest Powershots as well as the Performance series to complete the print-to-product workflow. The company says the residue-free cleaning process for brilliant colors enables a wider range of process parameters and precision adjustment than conventional cleaning processes. It is compatible with common powder-bed technologies and improves the depowdering of challenging process materials.
Related Content
-
Additive Manufacturing Is Subtractive, Too: How CNC Machining Integrates With AM (Includes Video)
For Keselowski Advanced Manufacturing, succeeding with laser powder bed fusion as a production process means developing a machine shop that is responsive to, and moves at the pacing of, metal 3D printing.
-
DMG MORI: Build Plate “Pucks” Cut Postprocessing Time by 80%
For spinal implants and other small 3D printed parts made through laser powder bed fusion, separate clampable units resting within the build plate provide for easy transfer to a CNC lathe.
-
3D Printed Cutting Tool for Large Transmission Part: The Cool Parts Show Bonus
A boring tool that was once 30 kg challenged the performance of the machining center using it. The replacement tool is 11.5 kg, and more efficient as well, thanks to generative design.