3D Automatic Unpacking System Enables Continuous Workflow
HP and AM Solutions collaborate on the HP Jet Fusion 5200 Series 3D Automatic Unpacking Station, which offers consistent, repeatable unpacking and a high powder reclaim rate.
Share
Read Next
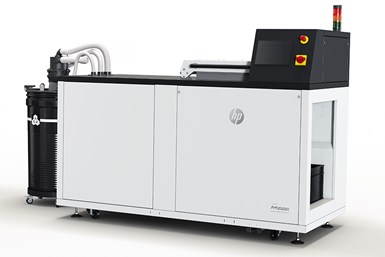
3D Automatic Unpacking Station
HP and AM Solutions have jointly developed the HP Jet Fusion 5200 Series 3D Automatic Unpacking Station. The machine is a scalable, industrial postprocessing solution that enables the fully automatic and consistent unpacking of AM parts made on the HP Jet Fusion 5200 3D Printing System in a continuous workflow, the company says. The machine is said to improve productivity increase and cost efficiency, as well as provide a higher powder reclaim rate for certain geometries. AM Solutions (a Rösler subsidiary) will manufacture the Automatic Unpacking Station at its 3D postprocessing technology location in Germany.
The machine combines the printing and postprocessing operations into one automated, scalable process. The automatic unpacking process takes place immediately after the cooling of the build job in the HP Natural Cooling Unit. A lifting device is used to transfer the cooling unit to the Automatic Unpacking Station. There it is positioned and unlocked, and the entire build job is placed in the station.
All relevant printing job data is transmitted to the unpacking station by means of its RFID reader. This is said to ensure that the job- and process-related data can be tracked, and the process monitored remotely by means of HP’s 3D Center software. The automated unpacking process — adapted to the individual workpieces — enables a considerably higher powder reclaim rate for certain geometries. An air suction system transfers the powder collected in the station continuously to a dedicated external tank. The printed parts are discharged into an unloading box. Once the external tank is full, it is replaced with an empty one, and the retrieved powder can be loaded back into an HP Build Unit after connecting the full tank to the processing station.
HP and AM Solutions have jointly developed the HP Jet Fusion 5200 Series 3D Automatic Unpacking Station. The machine is a scalable, industrial postprocessing solution that enables the fully automatic and consistent unpacking of AM parts made on the HP Jet Fusion 5200 3D Printing System in a continuous workflow, the company says. The machine is said to improve productivity increase and cost efficiency, as well as provide a higher powder reclaim rate for certain geometries. AM Solutions (a Rösler subsidiary) will manufacture the Automatic Unpacking Station at its 3D postprocessing technology location in Germany.
The machine combines the printing and postprocessing operations into one automated, scalable process. The automatic unpacking process takes place immediately after the cooling of the build job in the HP Natural Cooling Unit. A lifting device is used to transfer the cooling unit to the Automatic Unpacking Station. There it is positioned and unlocked, and the entire build job is placed in the station.
All relevant printing job data is transmitted to the unpacking station by means of its RFID reader. This is said to ensure that the job- and process-related data can be tracked, and the process monitored remotely by means of HP’s 3D Center software. The automated unpacking process — adapted to the individual workpieces — enables a considerably higher powder reclaim rate for certain geometries. An air suction system transfers the powder collected in the station continuously to a dedicated external tank. The printed parts are discharged into an unloading box. Once the external tank is full, it is replaced with an empty one, and the retrieved powder can be loaded back into an HP Build Unit after connecting the full tank to the processing station.
Related Content
With Electrochemical Additive Manufacturing (ECAM), Cooling Technology Is Advancing by Degrees
San Diego-based Fabric8Labs is applying electroplating chemistries and DLP-style machines to 3D print cold plates for the semiconductor industry in pure copper. These complex geometries combined with the rise of liquid cooling systems promise significant improvements for thermal management.
Read MoreDMG MORI: Build Plate “Pucks” Cut Postprocessing Time by 80%
For spinal implants and other small 3D printed parts made through laser powder bed fusion, separate clampable units resting within the build plate provide for easy transfer to a CNC lathe.
Read MoreWhat Is Neighborhood 91?
With its first building completely occupied, the N91 campus is on its way to becoming an end-to-end ecosystem for production additive manufacturing. Updates from the Pittsburgh initiative.
Read MoreActivArmor Casts and Splints Are Shifting to Point-of-Care 3D Printing
ActivArmor offers individualized, 3D printed casts and splints for various diagnoses. The company is in the process of shifting to point-of-care printing and aims to promote positive healing outcomes and improved hygienics with customized support devices.
Read MoreRead Next
Profilometry-Based Indentation Plastometry (PIP) as an Alternative to Standard Tensile Testing
UK-based Plastometrex offers a benchtop testing device utilizing PIP to quickly and easily analyze the yield strength, tensile strength and uniform elongation of samples and even printed parts. The solution is particularly useful for additive manufacturing.
Read MoreCrushable Lattices: The Lightweight Structures That Will Protect an Interplanetary Payload
NASA uses laser powder bed fusion plus chemical etching to create the lattice forms engineered to keep Mars rocks safe during a crash landing on Earth.
Read MoreBike Manufacturer Uses Additive Manufacturing to Create Lighter, More Complex, Customized Parts
Titanium bike frame manufacturer Hanglun Technology mixes precision casting with 3D printing to create bikes that offer increased speed and reduced turbulence during long-distance rides, offering a smoother, faster and more efficient cycling experience.
Read More