ExOne, SSI Collaborate to Drive Volume Production with Metal Binder Jetting
With ExOne 3D printers and SSI’s furnace and sintering capabilities, the parts manufacturer says it will offer components with increased complexity and size for volume production with no tooling in a variety of metals.
Share
Read Next
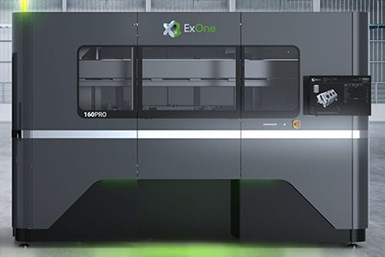
SSI will use the InnoventPro 3L for material and application development, with the X1 160Pro dedicated to volume production through a fully automated cell with continuous sintering and state-of-the-art furnace equipment. Photo Credit: ExOne
Wisconsin-based SSI Sintered Specialties, a supplier of high-performance metal parts, has purchased two metal binder jet 3D printers from ExOne, a global supplier of industrial sand and metal 3D printers using binder jetting technology.
SSI will use the InnoventPro 3L for material and application development, with the X1 160Pro dedicated to volume production through a fully automated cell with continuous sintering and state-of-the-art furnace equipment. The InnoventPro 3L metal binder jetting system features ExOne’s Triple Advanced Compaction Technology (ACT).
The two ExOne printers are slated for delivery in the first half of 2022 and will be located at the company’s headquarters in Janesville, Wisconsin. SSI says its 250,000-square-foot facility also houses the world’s largest installed capacity of high-temperature sintering furnaces — a process step which is core to metal binder jetting – and postprocessing technology to support volume production in metal binder jetting.
“The addition of metal binder jetting to SSI’s technology portfolio was the natural next step in providing our customers with the most advanced technology on the market to produce complex geometries in volume production,” says Paul Hauck, SSI Sintered Specialties COO. “Our expertise and lengthy heritage in high-temperature metallurgy processing is a perfect fit for binder jetting technology, and we are thrilled to be working with ExOne to offer our customers the future of metal 3D printing.”
SSI has over 40 years of powder metallurgy experience and metal 3D printing adds to the company’s existing capabilities in press and sinter powder metallurgy, and nontraditional metal injection molding. With ExOne’s 3D printers and SSI’s furnace and sintering capabilities, the parts manufacturer says it will offer components with increased complexity and size for volume production with no tooling in a variety of metals.
The investment in ExOne’s binder jet technology is just one of the steps in SSI’s business strategy to embrace additive manufacturing and bring new manufacturing solutions for volume production.
Related Content
-
3D Printed Metal Filters Protect Circuit Breakers from Explosion: The Cool Parts Show #57
New high-voltage circuit breakers from Schneider Electric make use of 3D printed metal filters to protect people and equipment in the event of an overload. Binder jetting provided both the geometric complexity and price point needed for these parts.
-
Multimodal Powders Bring Uniform Layers, Downstream Benefits for Metal Additive Manufacturing
A blend of particle sizes is the key to Uniformity Labs’ powders for 3D printing. The multimodal materials make greater use of the output from gas atomization while bringing productivity advantages to laser powder bed fusion and, increasingly, binder jetting.
-
What Is the Role of Sintering in Binder Jetting? (Video)
And how strong are green parts prior to sintering? Filmed at HP, here is a look at sintering, including the shrinkage from green to sintered binder jet parts.