Desktop Metal Qualifies 316l Stainless Steel for High-Volume Manufacturing
With 316L, businesses can produce cost-effective, end-use metal parts for extreme temperature, highly corrosive applications on the world’s fastest metal 3d printing platform, the company says.
Share
Read Next
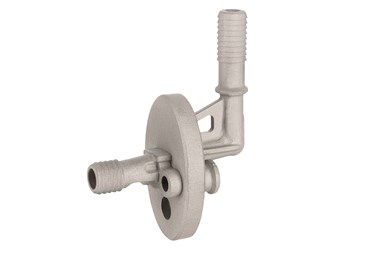
The Production System platform enables printing this heavy industry fluid connector in 316L stainless steel as a single, consolidated component and can support a throughput of nearly 5,500 parts per week.
Desktop Metal has qualified the use of 316L stainless steel for its Production System platform, which leverages patent-pending Single Pass Jetting (SPJ) technology designed to achieve some of the fastest build speeds in the metal additive manufacturing (AM) market.
Known for its corrosion resistance and excellent mechanical properties at extreme temperatures, 316L stainless steel is well suited for applications in demanding conditions, such as parts exposed to marine or pharmaceutical processing environments, food preparation equipment, medical devices and surgical tooling. It also exhibits excellent weldability by standard fusion and resistance methods, the company says.
“With 316L on the Production System P-50, businesses will now be able to leverage additive manufacturing to produce complex, end-use parts suitable for use in harsh environments at volumes and costs competitive with conventional manufacturing,” says Jonah Myerberg, Desktop Metal co-founder and CTO.
Through extensive testing, the Desktop Metal materials science team has validated that 316L stainless steel printed on Production System technology and sintered by Desktop Metal meets MPIF 35 standards for structural powder metallurgy parts set by the Metal Powder Industries Federation. The company says that parts printed with 316L have demonstrated excellent mechanical properties and corrosion resistance, while significantly decreasing production time and part cost.
One test involved rocker arms that are used to open and close intake and exhaust valves on an outboard marine engine. The use of 316L extended the part’s life and provided corrosion resistance against harsh saltwater environments. Manufacturing on the Production System P-50 enabled the production of more than a thousand parts per day with ribbing features and cutouts to deliver adequate strength and stiffness while maintaining low weight and a small footprint versus the standard cast alternatives, which require up to 8 to 14 weeks lead time.
Related Content
-
3D Printing Molds With Metal Paste: The Mantle Process Explained (Video)
Metal paste is the starting point for a process using 3D printing, CNC shaping and sintering to deliver precise H13 or P20 steel tooling for plastics injection molding. Peter Zelinski talks through the steps of the process in this video filmed with Mantle equipment.
-
DMG MORI: Build Plate “Pucks” Cut Postprocessing Time by 80%
For spinal implants and other small 3D printed parts made through laser powder bed fusion, separate clampable units resting within the build plate provide for easy transfer to a CNC lathe.
-
Postprocessing Steps and Costs for Metal 3D Printing
When your metal part is done 3D printing, you just pull it out of the machine and start using it, right? Not exactly.