Additive Manufacturing Media has covered Azoth before, but the company we wrote about previously is dramatically different than the company I visited in 2022. In 2018, Azoth was newly launched for the purpose of providing polymer 3D printed tooling to manufacturers. Four years later, the company has five different types of additive manufacturing processes in house that cover both polymer and metal, and 80% of its business is end-use production. This change came about gradually, in stages, as a response to its customers’ needs.
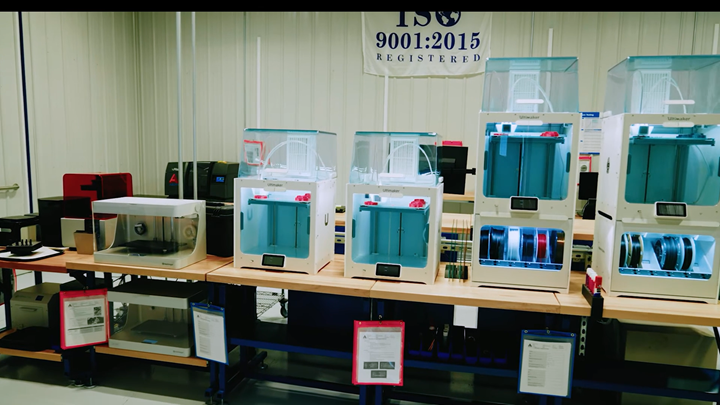
Azoth was founded to provide 3D printed tooling, jigs and fixturing to customers of the EWIE Group, an industrial distributor that manages tool cribs for large manufacturers. This work has transformed into a service the company calls TOMO Digital Inventory, where Azoth creates and manages a digital inventory of 3D printed tooling, printing parts on-demand. Photo Credit: Azoth
Building Experience Through Digital Inventory
Azoth’s roots are with the EWIE Group of Companies (EGC), an industrial distributor that brings cutting tool expertise to large manufacturers, including Ford, Rolls-Royce, General Motors and Caterpillar. EGC employees work on-site at these plants, managing customers’ indirect production needs such as cutting tools and abrasives, as well as jigs, fixtures and machine spare parts in some locations.
EGC has a wealth of knowledge and experience with subtractive manufacturing, but around 2017 it started considering additive manufacturing. “We saw throughout all of these different customer facilities that they’re trying to figure this out,” says Cody Cochran, co-founder and general manager at Azoth. “And the products they were trying to 3D print were the products we were purchasing and managing for them. And so we decided to get into additive manufacturing.” EGC founded Azoth to provide on-demand 3D printed tooling, fixturing and gaging that were traditionally made from UHMW, MC nylon, blue Delrin and ABS.
Thinking ahead to when it might move from printing components in-house to placing printers in customers’ facilities, Azoth started with polymer machines from Rize. (The company ceased operations in 2022, but its machines continue to be supported by Palitra.) At the time, the company believed that its customers would have safety and environmental concerns with open FDM machines, powder-based systems and certain materials like ABS. It needed a machine that was functional, easy to use and easy to approve for installation in customers’ facilities, and Rize met the requirements. Eventually, it expanded into other polymer-based 3D printing technologies as well. “We grew to the point where we were doing urethane casting, SLA, FDM and SLS, but everybody really needed metal,” Cochran says.
When looking at different metal AM technologies, the company needed to find something that had high throughput and part quality and was cost-effective for high-mix, low-volume work. Those requirements quickly ruled out some processes, such as powder bed fusion (PBF). In addition to PBF’s high startup costs, it would likely have required more time to dial in the parameters and more postprocessing, which made it impractical for Azoth’s on-demand model. “If someone’s ordering aluminum gripper fingers, I can't make them more cost effective with powder bed fusion, and they're going to last the same amount of time,” Cochran explains. “That’s going to be a difficult strategy, unless we try to bring additive value to every part we put in the field.”
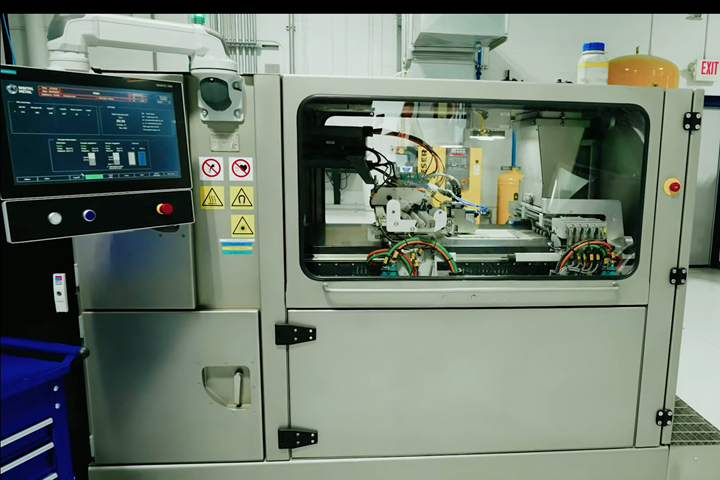
After expanding into multiple polymer 3D printing processes, Azoth realized that its customers needed metal parts. The company determined that binder jetting would enable the high throughput and part quality required for on-demand manufacturing, and added its first machine in 2018. Photo Credit: Azoth
Binder jetting, on the other hand, is more suited to the high-mix, low-volume production that Azoth needed, with its high throughput and part quality. The company got its first binder jetting machine in 2018 from Digital Metal (now part of Markforged), and over the next year printed close to 500 different unique geometries, according to Cochran. Many of the parts were originally designed for CNC machining, but Azoth was able to print them faster and most cost effectively using binder jetting.
At this point, Azoth had gained experience with multiple forms of 3D printing in a range of different materials. “We developed the capabilities to go into any of those customer plants, do a full inventory review, and tell them everything on the indirect side that could be 3D printed,” Cochran explains. This includes not only what parts could be 3D printed, but the best way to 3D print them. Eventually, the company launched this as a service called TOMO Digital Inventory. (TOMO stands for “take one, make one.”) Azoth creates and manages a digital inventory of 3D printed tooling for its customers, so when someone takes a 3D printed item out of the inventory, the company makes another one on demand and ships it to the customer.
To set up this digital inventory, Azoth first scrubs the customer’s inventory data using a custom algorithm which rules out parts based on specific keywords, product categories, price data and volume usage to create a shortlist of parts that could be 3D printed. (For example, additive doesn’t make sense for parts that customers procure from standard online catalogs or for components with high quantities.) A member of the Azoth team goes through the blueprints for all of the shortlisted parts and determines which ones can be printed, as well as which processes and materials to use. “The whole goal is to find the top 20 parts that should be transitioned to additive to make a business impact,” Cochran explains.
At the end of the evaluation process, the customer has a list of 3D printable parts that’s divided into different categories: parts that should be immediately transitioned to additive, parts that require more advanced testing and timelines, and parts that can be 3D printed in emergency situations.
Then Azoth prints prototype parts and sends them to the customer’s facility for validation. Testing is an important step for digital inventory, according to Cochran. “Digital inventory is more than 3D printing,” he says. “You have to have a validation part.” This is especially true if the 3D printed part has been redesigned or is made of a different material.
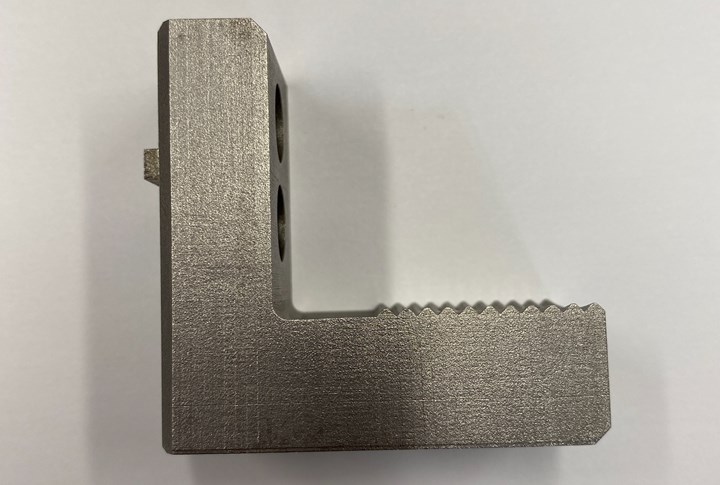
Binder jetting enables Azoth to 3D print parts that were originally designed for CNC machining, such as this gripper finger, faster and more cost effectively.
Once the part is tested and approved, it’s added to the digital inventory, which lives in the cloud. “We have the ability to connect to their facilities through API, where they have the parts stocked in vending machines, and we developed an ecosystem where that speaks right to Azoth to print on demand,” Cochran says. Customers who have enough volume of FFF printed parts can have a printer onsite, but parts made using other processes (including binder jetting) are made at Azoth’s Competence Center in Ann Arbor and shipped directly to the customer.
Even though many of these parts are designed for CNC machining, producing them via 3D printing can reduce lead times (from 6-10 weeks to 10-15 days, according to Cochran). It can be useful as a redundant source, especially for high-value parts. “It doesn’t make sense to switch to additive, but if you have an emergency situation, this will keep your line running,” he explains. Procuring parts on demand also reduces carrying costs and eliminates the issue of obsolete inventory. Say a process engineer wants to change the design of a gripper finger to make it more effective. If the company already has $15,000 worth of the original grippers in inventory, it would be difficult to make that switch.
Indirect to Direct
As Azoth continued to gain 3D printing experience, the types of parts customers were requesting started to change. “There was a shift from people wanting services just on indirect components and digital inventory,” Cochran says. “Late 2019, early 2020, we see the shift of people wanting actual end-use parts.”
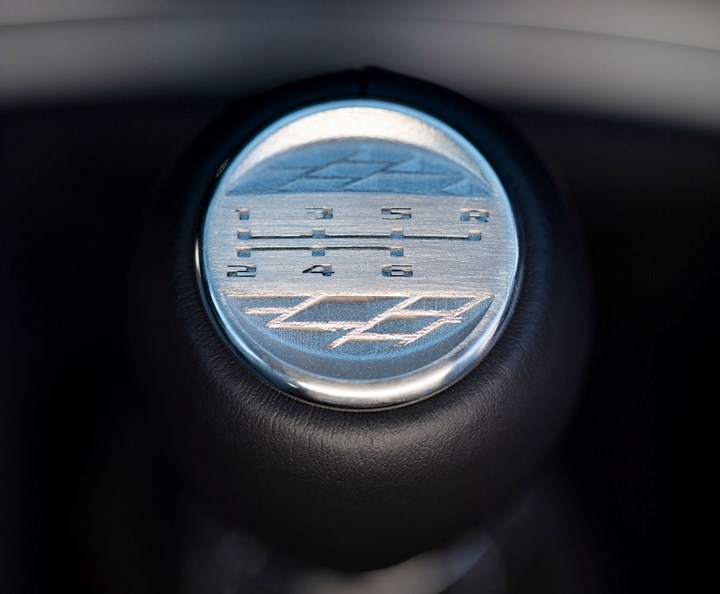
Eventually, customers shifted from needing 3D printed tooling to end-use parts. One of these production jobs was the shift knob medallion for the Cadillac Blackwing, which includes undercuts that cannot be machined.
Photo Credit: Cadillac
Taking 500 low-volume parts through the binder jetting process within a year taught Azoth the nuances of evaluating and designing parts for AM, the digital thread in binder jetting, and validation of 3D printed parts. One of the most important lessons was about sintering. “Printing has never been an issue. What you get out of the furnace is a different story,” Cochran explains. “Design for binder jet is typically design for sintering.” This was one reason that the company decided to focus on small, complex parts. “With sintering, tolerances right now are a percentage of your overall dimension,” he says. “So as you go with bigger parts, you have a wider tolerance band.” This equates to more postprocessing on larger parts.
One of Azoth’s production jobs was the first binder jetted part on a GM vehicle — a shift knob medallion for the Cadillac Blackwing. The medallion is cosmetic, but it features a geometry that can only be produced via 3D printing. The back is designed for heat dissipation, and the front features undercuts that can’t be machined. This part was notable because it passed a level 3 Production Part Approval Process (PPAP). “Now we’re working on dozens of parts for PPAP in the automotive industry across various customers,” Cochran adds.
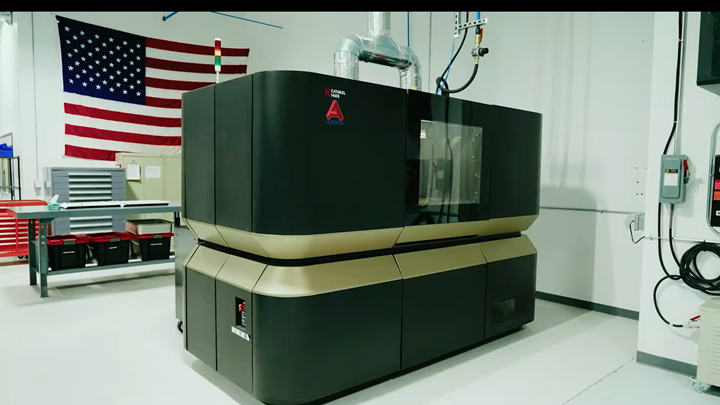
As Azoth has taken on smaller, more complex parts, it needed a solution that could produce parts with better surface finishes and tolerances than binder jetting. Its Carmel 1400M nanoparticle jetting system from XJet enables the company to produce parts that can’t be made by any other method. Photo Credit: Azoth
Azoth is seeing more production applications in the automotive industry, particularly in new electric vehicles, and the dental and medical industries, especially in end effectors for surgical robots. The dental and surgical parts in particular are the type of small, complex metal parts that Azoth seeks out, but it was finding that the surface finish and tolerance class produced by binder jetting often had limitations when considering high-volume production. The company found a solution in XJet’s Carmel 1400M metal nanoparticle jetting platform, the first of its kind in the U.S.
“The fact that they’re using nanoparticle metals got us excited,” Cochran says. “We knew that that would really enable a lot of advantages in sintering.” The smaller particle sizes allows the use of lower temperatures in sintering. With sintering temperatures that are further away from the material’s melting point, the parts distort less. Smaller particles also mean thinner layer heights and higher resolution prints.
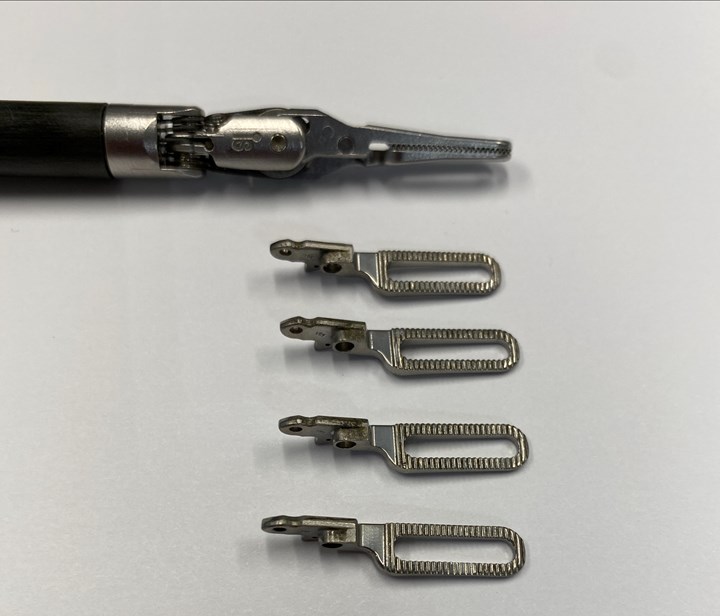
Metal nanoparticle jetting uses smaller particles than binder jetting, which enable Azoth to use lower temperatures when sintering, causing less distortion, as well as thinner layer heights for higher resolution prints. Medical and dental parts, such as these surgical robot end effectors, are a good fit for the machine, as well as defense and electronics work.
Cochran says that the XJet complements the company’s current capabilities. “There’s not really a product overlap (between binder jetting and nanoparticle jetting),” he says. “Where binder jetting starts to tail off just due to some physical limitations, our XJet solution picks up and it rounds out Azoth’s portfolio.”
Related Content
This Drone Bird with 3D Printed Parts Mimics a Peregrine Falcon: The Cool Parts Show #66
The Drone Bird Company has developed aircraft that mimic birds of prey to scare off problem birds. The drones feature 3D printed fuselages made by Parts on Demand from ALM materials.
Read MoreUnderstanding PEKK and PEEK for 3D Printing: The Cool Parts Show Bonus
Both materials offer properties desirable for medical implants, among other applications. In this bonus episode, hear more from Oxford Performance Materials and Curiteva about how these companies are applying PEKK and PEEK, respectively.
Read MoreQ&A With Align EVP: Why the Invisalign Manufacturer Acquired Cubicure, and the Future of Personalized Orthodontics
Align Technology produces nearly 1 million unique aligner parts per day. Its acquisition of technology supplier Cubicure in January supports demand for 3D printed tooling and direct printed orthodontic devices at mass scale.
Read MoreActivArmor Casts and Splints Are Shifting to Point-of-Care 3D Printing
ActivArmor offers individualized, 3D printed casts and splints for various diagnoses. The company is in the process of shifting to point-of-care printing and aims to promote positive healing outcomes and improved hygienics with customized support devices.
Read MoreRead Next
Cadillac Utilizes 3D Printing to Bring Back Manual Transmission
New Cadillac V-Series Blackwing models will be first GM production vehicles with functional 3D-printed parts, including two HVAC ducts and an electrical harness bracket.
Read MoreThis Company Is Pioneering Embedded Service as a Model for Delivering AM
PSMI manages ordering and inventory of tooling and MRO supplies for major manufacturers. Installing 3D printers within those customer sites offers an entirely different way to service this demand.
Read MoreFor AM and Machining to Work Together, Let Them Compete
A medical device maker establishes a center of excellence for product and process development in which additive manufacturing and CNC machining both challenge and complement one another.
Read More