When 3D printing contract manufacturer Cumberland Additive recently acquired the metal additive manufacturing operations of Stratasys Direct, the move doubled the company’s number of metal AM machines and gave the company an additional production facility in its home region of Austin, Texas. However, this new facility became not the second, but rather the third location for Cumberland. Prior to the acquisition, Cumberland opened a location far from its Texas headquarters at Neighborhood 91, the Pittsburgh, Pennsylvania, industrial park that is focused on additive manufacturing.
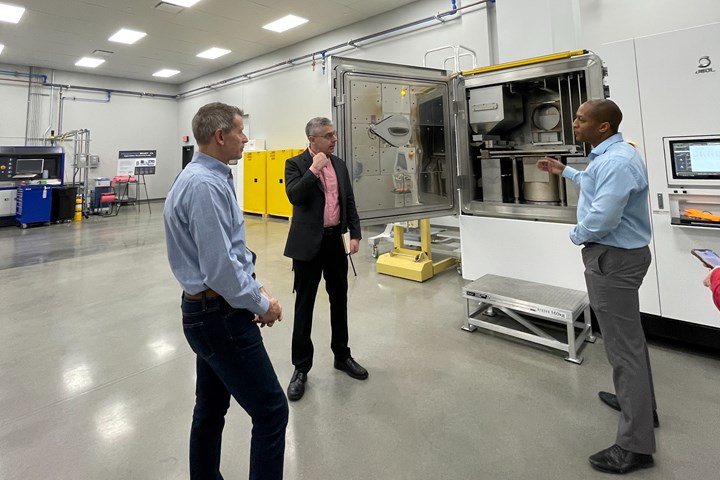
Cumberland Additive has two metal additive machines and processes at its Pittsburgh location. The Nikon SLM Solutions laser powder bed fusion machine (in the background and at the top of this page) closely matches the capabilities of an SLM machine used by a Neighborhood 91 neighbor. The JEOL electron beam melting machine is overseen by JEOL applications engineer Jonathan Buckley, who works at this facility. Buckley is at right, seen here with Cumberland's Mark Straszheim (left) and me.
Now, two years after opening the Pittsburgh site, Mark Straszheim, the Cumberland regional director who worked to stand up the facility, has various observations about the value the distant facility brings and how best to leverage its capabilities. The site has made an effective staging ground for the development of a partnership with a machine provider, JEOL, that is new for the company and new to the U.S. market. And while shifting AM work digitally between sites for distributed manufacturing is an option the company has successfully employed, Straszheim says the “digital transparency” of employees has delivered even greater value.
Opening a Pittsburgh Site and Joining Neighborhood 91
Cumberland’s leadership was interested in the Neighborhood 91 concept from the start. Becoming a tenant at this Pennsylvania campus would mean establishing a site geographically closer to customers in the Northeast while also benefiting from knowledge sharing with the staffs of other AM companies working at this location. The initial questions focused on how to imagine this northern sister site for Cumberland’s Pflugerville, Texas, main location.
According to Straszheim, “We were asking ourselves: Do we make it a focus factory? Or do we have production at one site and R&D at the other?”
The answer the company found was to establish a facility that is like Pflugerville in terms of its role — that is, both 3D printing and postprocessing, both production and prototyping — but also distinctly flavored to match to special possibilities of the Pittsburgh location.
For example, of the two powder bed fusion metal AM machines installed at the newer site, one of them, an SLM 500 from what is now Nikon SLM Solutions, closely matches a machine from the same provider that is used by the very first Neighborhood 91 tenant, locomotive component producer Wabtec. The Cumberland machine has the same X-Y travels as Wabtec’s SLM model; it differs just in Z.
Wabtec and Cumberland are not competitors. Therefore, the benefits of two neighbors having very nearly the same additive machine have been apparent for both. Pittsburgh manufacturing engineer Kyle Kubovcik says, “We each have better access to replacement parts, and our two teams together make up a larger pool of experience and expertise on this machine.” Cumberland also has served Wabtec by machining some of its parts when the latter’s machining center was overcommitted. And in one case, small but significant, Wabtec had on-hand the very lens cleaner Cumberland had run out of for servicing its machine. The cooperation in this moment resembled one residential neighbor borrowing a power tool or cup of sugar from another.
Meanwhile, the other powder bed machine at Cumberland’s Neighborhood 91 location is a JAM-5200 electron beam melting (EBM) system from JEOL. Cumberland is an early U.S. user of this company’s machine, and also a partner supporting the company’s introduction to the U.S. JEOL applications engineer Jonathan Buckley works here essentially as an adjunct Cumberland team member. He helps Cumberland with EBM part production and with translation of existing EBM jobs to this new platform for interested customers , while he also uses the location as a demonstration site for other prospective EBM users. The Neighborhood 91 location, with its close proximity to the Pittsburgh International Airport (the airport is one of the site’s landlords) makes it an ideal location for hosting this relationship.
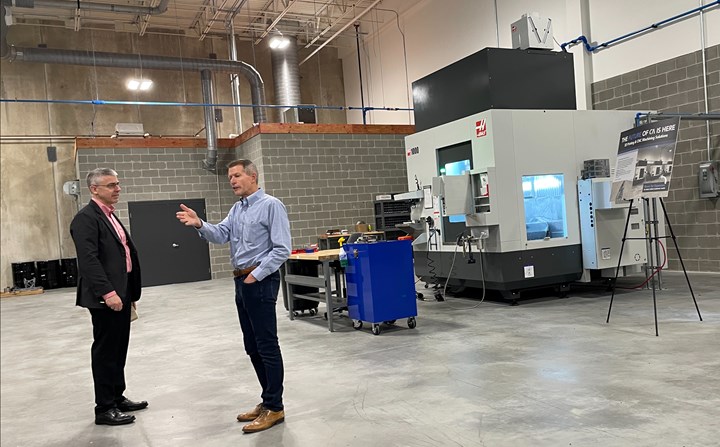
Machining is also a vital capability to have on-site, Straszheim says. The site’s five-axis machining center is seen here. Because of the digital transparency of Cumberland's organization, the machining expert based in Pittsburgh who programs and runs this machine actually spends most of his time writing programs for machine tools in Texas.
These two machines together are just a small share of Cumberland’s AM capacity overall. After the recent acquisition, the company has 35 powder bed fusion systems total, 31 of which are metal (the others are SLS machines for polymer). Similarly, a five-axis machining center from Haas Automation at the Neighborhood 91 site is just one of 25 CNC machine tools throughout the organization. Importantly, though, the share of personnel and talent in Pittsburgh is much greater. Kubovcik is one of six people doing similar AM engineering work for the company. Much of his time is focused on work performed in Texas. And for Pittsburgh CNC programmer Victor Ross, this is even more true — he is one of three CNC programmers in the company. He writes programs for the Neighborhood 91 machining center and runs this machine, while giving more than half of his time to programming work for Texas CNC machines.
Digital Transparency Empowers Multi-Site Manufacturing
This is what Straszheim means by digital transparency, his version of it at least. It simply should not matter much, if at all, where an engineering or programming employee is located. This employee transparency is a necessary and perhaps underappreciated requirement of a distributed manufacturing model. In additive, part files can be sent digitally for production wherever there is the right type of 3D printer and secure infrastructure. And in AM, the ratio of expert staffing to the number of machines is smaller than practically any production process. Put these two points together, and what they mean is that AM personnel located anywhere (except for the ones physically tending the machines) need to be able to serve production that is also occurring anywhere. Secure systems, open communications and minimal sense of cultural separation between geographic sites are the way to achieve this. As near as possible, Straszheim says, the multi-site company has to function like one big site, with access and responsibilities unaffected by where a desk is located.
This applies not just to 3D printing, but also to CNC machining. In metal part production, machining is part of AM — and this is why Ross spends so much of his time programming for Texas machine tools.
Doing this is not without challenge, he notes. “The difficulty in programming at a distance comes from just not being able to hold the part in my hand,” he says. “The clamping or approach strategy I am imagining maybe doesn’t work.” Generally, it is not long before a misperception such as this is seen and addressed. Still, it speaks to how a different quality of programmer is needed for this role, possessing a certain extra capacity to spatially imagine an abstract form.
The value of that kind of acuity speaks to a larger shift Straszheim sees. It is pronounced in AM, yet he believes it is apparent in all fields harnessing technology’s freedom to do more with fewer and more dispersed staffing. “The challenge of manufacturing today,” he says — and the challenge of small business — “is finding employees able to thrive using a broad range of abilities and talents.”
Related Content
Machine Tool Drawbar Made With Additive Manufacturing Saves DMG MORI 90% Lead Time and 67% CO2 Emission
A new production process for the multimetal drawbar replaces an outsourced plating step with directed energy deposition, performing this DED along with roughing, finishing and grinding on a single machine.
Read MoreSeurat: Speed Is How AM Competes Against Machining, Casting, Forging
“We don’t ask for DFAM first,” says CEO. A new Boston-area additive manufacturing factory will deliver high-volume metal part production at unit costs beating conventional processes.
Read MoreNew Zeda Additive Manufacturing Factory in Ohio Will Serve Medical, Military and Aerospace Production
Site providing laser powder bed fusion as well as machining and other postprocessing will open in late 2023, and will employ over 100. Chief technology officer Greg Morris sees economic and personnel advantages of serving different markets from a single AM facility.
Read MoreDMG MORI: Build Plate “Pucks” Cut Postprocessing Time by 80%
For spinal implants and other small 3D printed parts made through laser powder bed fusion, separate clampable units resting within the build plate provide for easy transfer to a CNC lathe.
Read MoreRead Next
Cumberland Additive Acquires Stratasys Direct Manufacturing Metals Operations, Doubles Metal AM Capacity
The agreement also expands and diversifies Cumberland’s material offerings in aluminum, copper and other metal materials.
Read MoreWhat Is Neighborhood 91?
With its first building completely occupied, the N91 campus is on its way to becoming an end-to-end ecosystem for production additive manufacturing. Updates from the Pittsburgh initiative.
Read MoreAdditive Manufacturing for Rail Industry Is Gaining Traction at Neighborhood 91
Locomotive manufacturer Wabtec is the first tenant of Pittsburgh’s N91 additive manufacturing ecosystem, where the company is ramping up production via laser powder bed fusion.
Read More