Zeiss, ORNL Collaborate on Fast, Automated Print Parameter Qualification Solution
RAPID 2021: ParAM is designed to evaluate print parameters to help reduce build failure rates and make AM processes reliable, while reducing the cost per part.
Share
Read Next
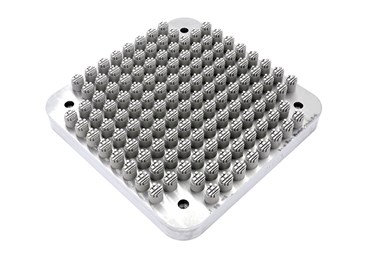
AM samples on build plate
Zeiss’ ParAM (Parameter for Additive Manufacturing) is an additive manufacturing (AM) solution service designed to help produce defect-free parts. Zeiss and the Defense Department’s Oak Ridge National Laboratory (ORNL) have working together at the ORNL Manufacturing Demonstration Facility to develop this novel, fully automated solution to comprehensively evaluate a set of parameters in less than 12 hours.
The company says that optimum print parameters dictate the ability to print with a new material, adapt to change in powder characteristics and increase print speed by increasing layer thickness to even placement of parts on the build plate. The goal is for users of ParAM to start with a design of experiments, print coupons and evaluate best print parameters from the design of experiments plan in the same day, so they are ready to print parts the next morning.
According to the company, only a handful of alloys are currently qualified for printing and the majority of those are used in conventional manufacturing. However, there is said to be tremendous benefit in developing and qualifying novel alloys specifically designed for AM. The current challenge is the qualification process, and technologies that can accelerate the development of new materials are said to be critical.
Zeiss ParAM’s test design and evaluation workflow make it a versatile solution for multiple applications, the company says. Examples include evaluating parameters to print defect-free parts with a change in powder quality or a degree of recycling; developing print parameters for thicker powder layers; qualification of a build envelop; evaluating or compensating for a laser performance in multilaser systems; and creating a parameter to print deformation-free parts. One or a combination of these parameter optimizations is said to help reduce the build failure rate and make AM processes reliable, while reducing the cost per part.
Related Content
-
Additive Manufacturing in Transportation: How It Moves Us
Transportation is experiencing unprecedented pressure to move people and goods farther, faster, cheaper and more sustainably. The Barnes Global Advisors and Wabtec discuss the role that additive manufacturing is playing for rail transportation, and how 3D printed parts such as manifolds are qualified for this industry.
-
Valve Manufacturer Outlines Path to Qualification for Additive Manufactured Pressure Equipment
In this case study, Samson shares how manufacturers can design and produce pressure equipment using additive manufacturing that is compliant with the European Pressure Equipment Directive (PED).
-
Additive Manufacturing for Defense: Targeting Qualification
Targeting qualification in additive manufacturing for the defense industry means ensuring repeatability as well as reliability as there is much at stake, including human lives. Certain requirements therefore must be met by weapons systems used by the defense industry.