Lithoz CeraMax 3D Printer for Large Ceramic Parts
Using laser-induced slipcasting (LIS) technology, the CeraMax Vario V900 3D printer is said to produce large ceramic parts in full densities.
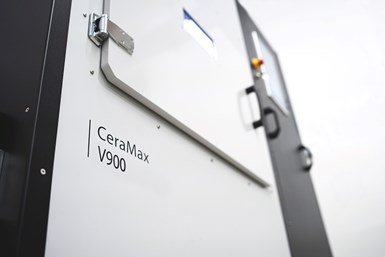
Lithoz’s CeraMax Vario V900 3D ceramic printer. Photo Credit: Lithoz
Lithoz says its CeraMax Vario V900 is the world’s first 3D printer that can produce large ceramic components with thick walls and full densities using oxide and non-oxide ceramics. The company says the printer can also easily process dark ceramics such as silicon carbide.
The printer uses laser-induced slipcasting (LIS) technology, enabling additive manufacturing (AM) using industrial water-based suspensions with very low organic binder contents. According to the company, this new technique has been specifically designed for producing large ceramic parts with thick walls and full densities.
The LIS technology uses water-based slurries of oxide and non-oxide ceramics, giving it the ability to apply up to 1.000 µm slurry per layer in less than a minute and a build envelope of up to 250 × 250 × 290 mm. Due to a simplified debinding process, wall thicknesses can be realized that have not yet been possible with other ceramic 3D printing technologies.
It is said green parts printed with this printer are machineable without any restrictions, meaning they can be easily reintroduced into the traditional ceramic process chain. For ceramic producers, it is said LIS technology is a good entry point into ceramic 3D printing as it combines the full 3D design flexibility plus an accelerated ceramic shaping process with economical water-based suspensions which stay very close to familiar standard slurries.
In the LIS technology powering the printer, the water-based slurry solution is said to completely absorb the laser beam. Due to treatment being purely heat-induced, it is said even dark ceramics such as silicon carbide can be processed without issues or loss of desired properties.
According to the company, silicon carbide is one of the most sought-after technical ceramics for both mechanical properties and width of possible applications, and is difficult to process via any AM technology that involves the use of light for curing of slurry materials. However, utilizing the LIS technology is said to enable processing this material.
Related Content
-
Formlabs Expands SLA/SLS Ecosystem With New Materials, Postprocessing Tools
The new hardware, software and materials are designed to streamline postprocessing and unlock new workflows.
-
Video: AM for Harder, Longer-Lasting Brake Discs
Additive manufacturing is being applied to limit automotive brake dust. For a major automaker, Etxetar and Talens are developing a production-speed directed energy deposition system to give brake discs a precise layer of wear-resistant carbide.
-
Horizon Expands Services With Subcontract Micro AM Production, Design Support
Horizon also offers a suite of proprietary coating processes that enable customers to successfully expand the functionality of parts which are typically produced in plastics on commercially available micro additive manufacturing platforms.