HP, AM Solutions Jointly Develop 3D Automatic Unpacking Station
Joint development is said to offer significant productivity increase, greatly improved cost efficiency and higher powder reclaim rate for certain geometries.
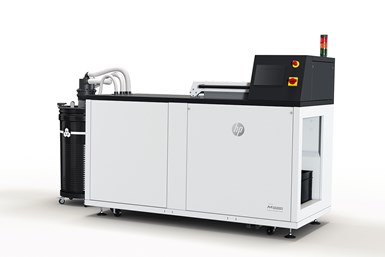
HP Jet Fusion 5200 Series 3D Automatic Unpacking Station. Photo Credit: HP
HP and Rösler’s AM Solutions have jointly developed the HP Jet Fusion 5200 Series 3D Automatic Unpacking Station. This scalable, industrial postprocessing solution is said to enable the fully automatic and consistent unpacking of AM parts made on the HP Jet Fusion 5200 3D Printing System in a continuous workflow.
The companies say that, compared to manual unpacking operations, this solution offers a significant productivity increase, greatly improved cost efficiency and higher powder reclaim rate for certain geometries.
The unpacking station is said to enable 3D printing on an industrial scale because it combines printing and postprocessing operations into one automated, scalable process for consistent, repeatable unpacking and a high powder reclaim rate.
The automatic unpacking process takes place immediately after the cooling of the build job in the HP Natural Cooling Unit. A lifting device is used to transfer the cooling unit to the Automatic Unpacking Station. There it is positioned, unlocked and the entire build job is placed in the station. All relevant printing job data is transmitted to the unpacking station by means of its RFID reader. This ensures that the job- and process-related data can be tracked and the process monitored remotely by means of HP’s 3D Center software.
According to the companies, the automated unpacking process, adapted to the individual workpieces, also enables a considerably higher powder reclaim rate for certain geometries. An air suction system transfers the powder collected in the station continuously to a dedicated external tank. The printed parts are discharged into an unloading box. Once the external tank is full, it is replaced with an empty one, and the retrieved powder can be loaded back into an HP Build Unit after connecting the full tank to the Processing Station.
The Automatic Unpacking Station is said to minimize manual operations and reduce overall cycle time for certain applications because the unpacking operation can start right after the recommended minimum cooling time is completed.
Related Content
-
This Drone Bird with 3D Printed Parts Mimics a Peregrine Falcon: The Cool Parts Show #66
The Drone Bird Company has developed aircraft that mimic birds of prey to scare off problem birds. The drones feature 3D printed fuselages made by Parts on Demand from ALM materials.
-
3D Printed Titanium Replaces Aluminum for Unmanned Aircraft Wing Splice: The Cool Parts Show #72
Rapid Plasma Deposition produces the near-net-shape preform for a newly designed wing splice for remotely piloted aircraft from General Atomics. The Cool Parts Show visits Norsk Titanium, where this part is made.
-
What Is Neighborhood 91?
With its first building completely occupied, the N91 campus is on its way to becoming an end-to-end ecosystem for production additive manufacturing. Updates from the Pittsburgh initiative.