Formlabs Develops Powder for Strong, Flexible End-Use Parts, Prototypes
The material’s characteristics enable users to print end-use parts that need to bend or take impact such as hinges, clips and orthotics.
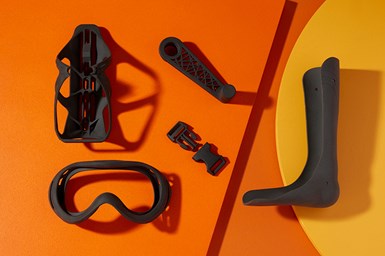
Nylon 11 Powder’s ductile, strong and flexible characteristics make it well suited for end-use parts that must be able to take impact and handle wear and tear over time, including snaps, clips, and hinges.
Formlabs’ Nylon 11 powder is a high-performance nylon material developed for functional prototyping and small batch production. It is designed for use on Formlabs’ Fuse 1 high-performance selective laser sintering (SLS) 3D printer.
The material enables users to print parts that need to bend or take impact such as hinges, clips and orthotics, making it well suited for manufacturing, engineering, and health care uses. Nylon 11 powder is one of many materials Formlabs plans to launch for use with the benchtop Fuse 1 printer, which is designed to make industrial 3D printing more cost accessible and user friendly with its straightforward workflow.
The Nylon 11 powder was developed to bolster design and creation capabilities with low cost per part. It requires less training and additional equipment needed, compared to other PA11 materials on the market, the company says. This is said to expand the functionality of the Fuse 1 and enable users to print end-use parts that can handle wear and tear over time, all in-house.
The material is said to be optimal for products requiring durability and performance. Nylon 11 Powder’s ductile, strong and flexible characteristics make it well suited for end-use parts that must be able to take impact and handle wear and tear over time, including snaps, clips, and hinges. It also designed for use in manufacturing, production, engineering and product design to create impact-resistant prototypes, thin-walled ducts and enclosures, robust jigs and fixtures, replacement parts, and prosthetics and orthotics.
According to the company, using Nylon 11 powder with the Fuse 1 gives engineers, product designers and manufacturers design freedom, the ability to customize end-use parts, and speed in bringing products to market.
Related Content
-
3D Printed Spine Implants Made From PEEK Now in Production
Medical device manufacturer Curiteva is producing two families of spinal implants using a proprietary process for 3D printing porous polyether ether ketone (PEEK).
-
3D Printing with Plastic Pellets – What You Need to Know
A few 3D printers today are capable of working directly with resin pellets for feedstock. That brings extreme flexibility in material options, but also requires greater knowledge of how to best process any given resin. Here’s how FGF machine maker JuggerBot 3D addresses both the printing technology and the process know-how.
-
Q&A With Align EVP: Why the Invisalign Manufacturer Acquired Cubicure, and the Future of Personalized Orthodontics
Align Technology produces nearly 1 million unique aligner parts per day. Its acquisition of technology supplier Cubicure in January supports demand for 3D printed tooling and direct printed orthodontic devices at mass scale.