EOS Expands Metal Additive Manufacturing Options for Demanding Industries
The two stainless steels, one tool steel and one nickel alloy were designed and optimized specifically to increase application opportunities for demanding industries.
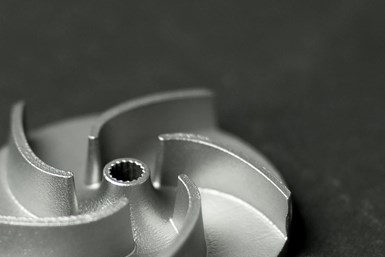
Impeller, austenitic EOS stainless steel 254 3D printing material. Photo Credit: EOS
EOS has four new metal materials for additive manufacturing (AM) on its EOS M 290 metal system, including two stainless steels, one tool steel and one nickel alloy. The four new metal materials were designed and optimized specifically to meet the needs of AM to increase application opportunities for demanding industries.
Stainless steel 254 is tailored for extreme conditions. It is an austenitic stainless steel that comes with a 40/60 micrometer process for the EOS M 290 system. The high chromium, molybdenum and nitrogen alloying are said to give excellent corrosion resistance in many difficult environments. The company says the material has an excellent stress corrosion cracking and higher strength than conventional austenitic steel. It also said to show excellent resistance to uniform, pitting and crevice corrosion. The material is particularly well suited for applications such as chlorinated seawater handling equipment, pulp and paper manufacturing devices as well as chemical handling equipment.
EOS StainlessSteel SuperDuplex is well suited for difficult environments. It comes with a 40/80 micrometer process for the EOS M 290 system. It is an austenitic-ferritic duplex stainless steel optimized for AM while maintaining super duplex properties. Its high chromium, molybdenum and nitrogen alloying are said to give excellent corrosion resistance in many difficult environments. At the same time, it is said to show excellent resistance to uniform, pitting and crevice corrosion, as well as enabling high strength together with high corrosion resistance. The company says the optimization of phase balance enables use of the product in as-manufactured condition in many use cases. The material is particularly suited for applications in the oil and gas industry, in pulp and paper manufacturing devices and for mining and offshore equipment.
EOS ToolSteel CM55 is well suited for use at elevated temperatures. It comes with a 40/80 micrometer process for the EOS M 290 system. It is a cobalt-free, ultra-high strength and high hardness steel for tooling and engineering solutions. The company says its alloying elements and moderate carbon content form a strong, stable structure for demanding applications and for the use in elevated temperatures. Typical applications include cold and hot working tools, powertrain components and parts for mechanical engineering.
EOS NickelAlloy Haynes 282 is designed for use at elevated temperatures. It is a nickel alloy powder intended for manufacturing parts on EOS metal systems. The company says it is a precipitation-strengthened, nickel-base superalloy with a unique combination of high temperature strength, thermal stability, good corrosion and oxidation resistance, easy fabricability and excellent weldability. It was developed for high-temperature structural applications and is manufactured under license from Haynes International Inc. Typical applications range from aerospace and rocket engine components to turbomachinery and gas turbine parts, and to energy industry components.
Related Content
-
How Norsk Titanium Is Scaling Up AM Production — and Employment — in New York State
New opportunities for part production via the company’s forging-like additive process are coming from the aerospace industry as well as a different sector, the semiconductor industry.
-
3D Printed NASA Thrust Chamber Assembly Combines Two Metal Processes: The Cool Parts Show #71
Laser powder bed fusion and directed energy deposition combine for an integrated multimetal rocket propulsion system that will save cost and time for NASA. The Cool Parts Show visits NASA’s Marshall Space Flight Center.
-
With Electrochemical Additive Manufacturing (ECAM), Cooling Technology Is Advancing by Degrees
San Diego-based Fabric8Labs is applying electroplating chemistries and DLP-style machines to 3D print cold plates for the semiconductor industry in pure copper. These complex geometries combined with the rise of liquid cooling systems promise significant improvements for thermal management.