Desktop Metal Qualifies D2 Tool Steel for Studio System 2
Engineers can now produce D2 cold work tool and die parts using a simple, two-step bound metal process.
Share
Read Next
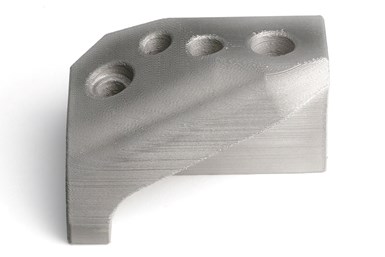
The company says D2 is a versatile high-carbon, high-chromium air-hardening tool steel characterized by its high hardness and compressive strength after heat treatment. Photo Credit: Desktop Metal
Desktop Metal has qualified D2 tool steel for its Studio System 2, which it says is an accessible metal 3D printing platform offering customers an easy way to print high-performance metal parts in low volumes for preproduction and end-use applications. Desktop Metal offers the material in a two-step bound metal additive manufacturing (AM) process, enabling customers to utilize a simple, nearly hands-free process to produce parts for high-strength D2 applications such as cold work metal forming tools, dies, punches and injection molds with conformal cooling channels.
The company says D2 is a versatile high-carbon, high-chromium air-hardening tool steel characterized by its high hardness and compressive strength after heat treatment. This tool steel is said to offer extremely high wear resistance properties, dimensional stability and corrosion resistance in the hardened condition, which is a key benefit for conformal cooling applications. D2 is used for a wide variety of cold work tools that require a combination of wear resistance and moderate toughness, such as coining and sizing tool members, blanking and forming dies, shear cutting tools, gauges, burnishing tools and other wear parts.
According to the company, D2 tool steel has traditionally been a challenging and expensive material with which to work. With this material now available on the Studio System 2, the company says it has streamlined production of D2 parts to just two simple steps for improved affordability and accessibility. This new material is said to feature higher hardness after heat treatment than all of the other Studio System materials qualified to-date, unlocking new applications that require tooling material grade strength.
With the Studio System 2, D2 tool steel parts demonstrate excellent mechanical properties on a more accessible platform than legacy powder bed fusion 3D printing alternatives, the company says. It is said the Studio System 2 is an office-friendly metal AM system that leverages Desktop Metal’s proprietary Bound Metal Deposition (BMD) technology to produce parts. The easy, two-step process enables parts to be transferred directly from the printer into the furnace, thereby providing a nearly hands-free experience, while eliminating loose powders and dangerous lasers commonly associated with metal 3D printing.
Consisting of a printer and furnace, the Studio System 2 is said to simplify in-house low volume production of a wide range of complex geometries with outstanding surface finish and high-performance mechanical properties.
Related Content
-
AM 101: What Is Binder Jetting? (Includes Video)
Binder jetting requires no support structures, is accurate and repeatable, and is said to eliminate dimensional distortion problems common in some high-heat 3D technologies. Here is a look at how binder jetting works and its benefits for additive manufacturing.
-
DMG MORI: Build Plate “Pucks” Cut Postprocessing Time by 80%
For spinal implants and other small 3D printed parts made through laser powder bed fusion, separate clampable units resting within the build plate provide for easy transfer to a CNC lathe.
-
VulcanForms Is Forging a New Model for Large-Scale Production (and It's More Than 3D Printing)
The MIT spinout leverages proprietary high-power laser powder bed fusion alongside machining in the context of digitized, cost-effective and “maniacally focused” production.