AddUp's FormUp 350 Metal 3D Printer Designed for Safe, Repeatable Operation
Printer offers modular, scalable architecture to delay obsolescence and maintain high level of performance.
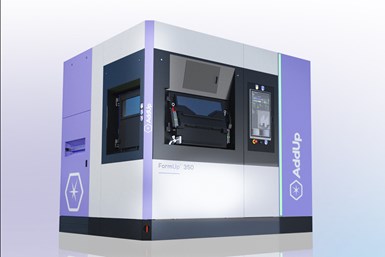
AddUp’s FormUp 350 metal 3D printer
AddUp’s FormUp 350 metal 3D printing machine uses laser powder bed fusion (PBF) technology to enable safe operation while producing quality, repeatable series of parts. The system relies on a modular, scalable architecture designed to delay machine obsolescence and maintain a high level of performance.
The company says the FormUp 350 can be used safely with all types of metal powders, reactive or not, with fine or medium granulometry. An autonomous powder module is said to ensure the storage, conveyance, recovery and sieving of powder — with all operations carried out automatically in a closed circuit, inert atmosphere. Exposure to fumes and smelting residue is controlled using an automatic passivation filter system for safe waste disposal.
All machine parameters are accessible according to users’ needs, ranging from a simplified standard use to an expert mode. Specific manufacturing recipes can be developed for each application to find the best balance between productivity and quality for each part.
The lasers provide geometric precision with the spot center of each laser at 35 µm, and are all equipped with a 3-axis optical chain, a high-end technology to ensure both positioning accuracy (24-bit resolution) and laser beam quality. The machine’s NCore software is capable of processing large production files of more than 80 GB in one go, enabling production of complex parts.
The dashboard enables traceability and analysis of all production data, including the tracking of 80 manufacturing parameters and the automatic editing of production conformity reports. The machine also features an interchangeable coating device, enabling users to choose the powder spreading system that best suits their needs— a scraper system or roller system. It can use four 500 W lasers simultaneously with each laser covering the entire surface of the tray.
The FormUp 350 comes in four configurations: starter, efficiency, productivity and advanced. Its modular design enables customers to add new modules, options or equipment at any time, without replacing the machine.
Related Content
-
How Machining Makes AM Successful for Innovative 3D Manufacturing
Connections between metal 3D printing and CNC machining serve the Indiana manufacturer in many ways. One connection is customer conversations that resemble a machining job shop. Here is a look at a small company that has advanced quickly to become a thriving additive manufacturing part producer.
-
Additive Manufacturing Is Subtractive, Too: How CNC Machining Integrates With AM (Includes Video)
For Keselowski Advanced Manufacturing, succeeding with laser powder bed fusion as a production process means developing a machine shop that is responsive to, and moves at the pacing of, metal 3D printing.
-
What Is Neighborhood 91?
With its first building completely occupied, the N91 campus is on its way to becoming an end-to-end ecosystem for production additive manufacturing. Updates from the Pittsburgh initiative.