Additive Industries’ MetalFABG2 Features Modular, Scalable, Open Systems
All three series models offer modular, scalable, open systems to ensure maximum flexibility and enable configurations up to 11 modules.
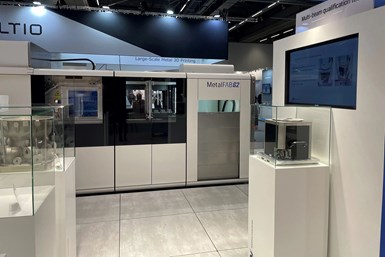
Additive Industries’ MetalFABG2 large-frame metal additive manufacturing system features modular, scalable, open systems. Photo Credit: Additive Industries
Additive Industries’ MetalFABG2 is the next generation of its MetalFAB large-frame metal additive manufacturing (AM) system designed to offer double the productivity, compared to its previous models.
The series has over 150 updates, and features optimized gas flow and heat management, updated process parameters and automated beam quality measurements. The system is also Sigma Labs PrintRite3D ready and is available in three versions — Core, Automation and Continuous Production. The models feature a build volume of 420 × 420 × 400 (width × depth × height) and build speed up to 150 cm3/hr.
All three models offer modular, scalable, open systems to ensure maximum flexibility and enable configurations up to 11 modules. When capacity needs increase, users can add more modules. Users can also optimize print parameter settings for specific part qualification.
The series has automated manual steps for conventional powder bed fusion (PBF) printers to ensure high productivity, resulting in a lower cost per printed part. The fully automated process is also said to reduce human errors and increase reproducibility.
For industrial-quality production, the part reproducibility of the MetalFAB is assured through solid machine design in combination with advanced laser calibration technology that can be preprogrammed to automatically run at specified intervals, the company says. Pedictability is achieved by combining part build simulation, scripted process controls and in-process quality monitoring.
The MetalFAB system can be configured to include several optional modules that extend productivity or automate postprocessing. Flexible configurations include up to four AM Cores with 1 to 4 lasers, storage module, exchange module.
The MetalFABG2 Core model is designed for large part production and application development, and offers benefits such as four full-field lasers and closed-loop powder handling.
The MetalFABG2 Automation model is able to run two jobs consecutively, and offers maximum ease of use and safety to the operator, the company says. It is well suited for small to medium series production.
The MetalFABG2 Continuous Production model is designed for continuous series production over multiple print cores in one system, and can print up to eight sequential jobs autonomously.
Related Content
-
“Mantis” AM System for Spacecraft Uses Induction for Deposition
The metal 3D printing system melts wire without lasers. 30-foot-diameter parts are built on a rotary-feed system that eliminates the need for a large machine frame or gantry.
-
Big Metal Additive: The Difference Between a Shape and a Part Is Quality
Preparing to scale directed energy deposition to ongoing full production is not a technological challenge: DED is ready. But it is an organizational challenge, says the company founder. Here is what it means to implement a quality system.
-
Robot Vs. Gantry for Large-Format Additive Manufacturing (Includes Video)
Additive Engineering Solutions, specialist at 3D printing very large parts and tools on gantry machines, now also uses a robot for large-format AM. Here is how the robot compares.