3D Systems’ VSP Bolus Optimizes Radiotherapy Targeting
The system is designed to enable the creation of a more personalized bolus made from a soft material that contours to the patient’s anatomy, enabling a more efficacious treatment and a more comfortable experience.
Share
Read Next
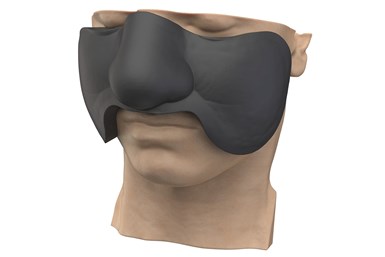
3D Systems’ VSP bolus face demo. Photo Credit: 3D Systems
3D Systems’ is entering the radiation oncology market with the FDA 510(k) clearance of its VSP Bolus — a printing solution designed to deliver high-quality, patient-specific radiotherapy treatment accessories. The 3D printing of the patient-specific shape is said to optimize radiotherapy targeting by reducing air gaps, thereby improving the efficacy of treatment and the patient experience.
The company says the VSP Bolus offers a full design and production service providing a personalized medical device based on the patient’s treatment plan. As a result, radiotherapy providers do not need specialized design software and expertise, thereby enabling them to focus directly on patient treatment and care.
3D Systems says its experience in the additive manufacturing (AM) of medical devices enables it to deliver 3D-printed, biocompatible patient-specific boluses that can improve therapy modulation as well as patient comfort.
According to the company, approximately 50% of patients diagnosed with cancer will receive radiotherapy as part of their treatment. To help target the radiation during treatment, the provider (for example, medical physicist, dosimetrist, radiation oncologist) will use a bolus — a flexible device that conforms to the patient’s skin. Off-the-shelf boluses can often leave gaps between the device and the patient’s anatomy, which can result in insufficient dosing and may also expose adjacent anatomy to undesired radiation.
With VSP Bolus, 3D Systems can design and deliver boluses that conform to a wide range of anatomies. The process begins with the patient’s imaging data and input from the radiotherapy professional. Using this information, VSP Bolus is designed at the requested material thickness to optimize the radiotherapy targeting. With these capabilities built into the solution, it is said radiotherapy professionals are freed from the time-consuming task of creating the design and fabricating the accessory themselves.
Once designed, 3D Systems’ engineers employ the company’s AM solutions to produce a high-quality bolus from a soft material that contours to the patient’s anatomy, enabling more efficacious treatment and a more comfortable experience, the company says.
Related Content
-
New Zeda Additive Manufacturing Factory in Ohio Will Serve Medical, Military and Aerospace Production
Site providing laser powder bed fusion as well as machining and other postprocessing will open in late 2023, and will employ over 100. Chief technology officer Greg Morris sees economic and personnel advantages of serving different markets from a single AM facility.
-
3D Printed PEEK Spine Implants in Production: The Cool Parts Show Bonus
Curiteva is using Fused Strand Deposition to produce two different lines of FDA-cleared spine implants. We visited the company’s Huntsville, Alabama, facility to learn more.
-
Ultra-Complex 3D Printed Scaffolds Enable Cell Growth: The Cool Parts Show #70
Perhaps the ultimate surface-area challenge is in bioengineering: creating structures that can grow sufficient cells within a compact volume to be effective for leading-edge medical treatments. The Southwest Research Institute develops bioreactor scaffolds that could only be made using 3D printing.