Vertex Manufacturing Selects Velo3D for 3D Printing Production-Ready Metal Parts
System to give Vertex customers more design freedom to engineer complex geometries.
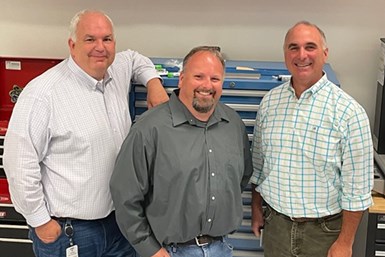
(Left to right) Tim Warden, Steve Rengers and Greg Morris, co-founders of Vertex Manufacturing.
Vertex Manufacturing, a Cincinnati-based business providing CNC machining and manufacturing services from development through production, has selected Velo3D to help meet its customers’ growing demand for 3D printing “impossible” metal parts. This advanced manufacturer and full-service machining shop is expanding its support for production programs with its first Velo3D Sapphire intelligent additive manufacturing (AM) solution.
Vertex was founded by early AM enthusiasts Greg Morris, Steve Rengers and Tim Warden, previously of Morris Technologies Inc. (MTI). It was created to leverage their advanced manufacturing and technology backgrounds to help companies solve some of their most difficult problems. Vertex is registered and certified for AS9100, ISO13485 and ITAR.
At MTI, they were best known for their work with GE Aviation’s 3D printed LEAP Engine fuel nozzle used in commercial aviation. The LEAP Engine fuel nozzle was one of the first metal AM parts to be certified for flight by the U.S. Federal Aviation Administration.
“With unique technology providing the capability to create production parts that would be impractical or impossible using other methods, our new additive manufacturing solution from Velo3D means customers will have even more freedom to design and engineer some of the most complex geometries imaginable,” says Greg Morris, co-founder and CEO, Vertex Manufacturing.
Where Morris Technologies primarily focused on prototyping use cases, Vertex was created to help customers who need advanced manufacturing solutions for both development and production programs. It offers a range of services including advanced multi-axis CNC machining, additive manufacturing, rapid castings and final inspection of manufactured parts.
Related Content
-
What Is Neighborhood 91?
With its first building completely occupied, the N91 campus is on its way to becoming an end-to-end ecosystem for production additive manufacturing. Updates from the Pittsburgh initiative.
-
Video: 5" Diameter Navy Artillery Rounds Made Through Robot Directed Energy Deposition (DED) Instead of Forging
Big Metal Additive conceives additive manufacturing production factory making hundreds of Navy projectile housings per day.
-
DMG MORI: Build Plate “Pucks” Cut Postprocessing Time by 80%
For spinal implants and other small 3D printed parts made through laser powder bed fusion, separate clampable units resting within the build plate provide for easy transfer to a CNC lathe.