Velo3D Ships First Sapphire XC to Aerospace Customer
The company’s newest and largest metal 3D printer is said to deliver bigger parts, productivity improvements and cost reduction for metal additive manufacturing
Share
Read Next
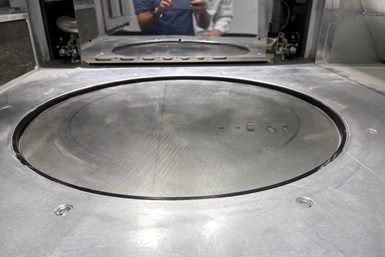
The extra-capacity build plate of the Sapphire XC metal 3D printer is said to enable larger parts, increased throughput and lower costs per part. Photo Credit: Velo3D
Velo3D has delivered its first Sapphire XC large-scale 3D printer to an aerospace customer to improve its additive manufacturing capabilities. The Sapphire XC (or Extra Capacity) is the company’s newest and largest metal 3D printer which is said to deliver both faster production and larger parts. The Sapphire XC is a scale-up version of the Sapphire printer, utilizing the same Flow print preparation software, Assure quality control software and Intelligent Fusion manufacturing process.
The company says the Sapphire XC is built to enable a seamless transition of parts that were developed and qualified on Sapphire to the larger, more productive Sapphire XC to reduce the cost of producing parts by up to 75%. Sapphire XC also expands the use of Velo3D’s production solution to parts that are up to 400% larger in volume than the largest parts possible with the original Sapphire. The aerospace company receiving the new Sapphire XC will use it to scale up production of its product which is built using the Sapphire fleet of metal 3D printers it already has.
“Because our customer is already utilizing our end-to-end production solution, they can immediately and seamlessly move parts to Sapphire XC to achieve a phenomenal production rate increase,” says Benny Buller, Velo3D CEO and founder.
It is one of the largest available laser powder bed fusion (LPBF) printers with a build volume of 600 mm × 550 mm, which is 400% larger volume than the original Sapphire system. It also offers 8 lasers × 1,000 W each and utilizes the same optical-train design, recoater technology, gas-flow technology and metrology as the current Sapphire. Together, these features are said to increase throughput by up to 400%, which lowers the cost of produced parts by up to 75%.
Related Content
-
Beehive Industries Is Going Big on Small-Scale Engines Made Through Additive Manufacturing
Backed by decades of experience in both aviation and additive, the company is now laser-focused on a single goal: developing, proving and scaling production of engines providing 5,000 lbs of thrust or less.
-
Additive Manufacturing Is Subtractive, Too: How CNC Machining Integrates With AM (Includes Video)
For Keselowski Advanced Manufacturing, succeeding with laser powder bed fusion as a production process means developing a machine shop that is responsive to, and moves at the pacing of, metal 3D printing.
-
How Norsk Titanium Is Scaling Up AM Production — and Employment — in New York State
New opportunities for part production via the company’s forging-like additive process are coming from the aerospace industry as well as a different sector, the semiconductor industry.