Velo3D Expands European Presence with New Technical Center
European expansion also includes Schoeller Bleckmann Oilfield Technology’s purchase of first end-to-end solution, including the Sapphire printer, to expand its additive manufacturing capabilities.
Share
Read Next
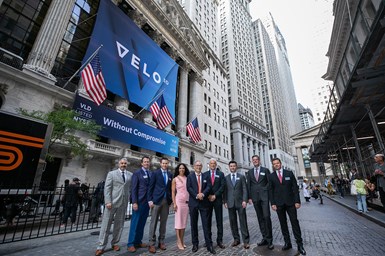
The Velo3D team in front of the New York Stock Exchange.
Velo3D, a metal additive manufacturing (AM) technology company for mission-critical parts, has expanded its European presence to support its growth efforts in the region. The expansion includes a technical center in Augsburg, Germany, where Velo3D’s Sapphire systems will be assembled and demonstrated. The company is also delivering the first end-to-end manufacturing solution to Schoeller-Bleckmann Oilfield (SBO) Technology, a European contract manufacturer specializing in the production of high-value metal parts for the oil and gas industry.
“Europe is a key market for Velo3D’s growth in the coming years and we’re thrilled to deliver our first end-to-end additive manufacturing solution and open our new technical center to accelerate this expansion,” says Benny Buller, Velo3D CEO and founder.
Velo3D’s European Technology Center will enable the company to demonstrate its 3D printing capabilities. The facility will be located at the Augsburg Innovations Park in Augsburg, Germany, and will include more than 110 square meters (1,200 square feet) of space across a main hall (which will house Sapphire systems), a lab area and offices. It also includes conference rooms for hosting customers for presentations, events and other meetings.
SBO is a multinational corporation with 1,130 employees worldwide operating more than 450 conventional CNC machines. The company’s U.S.-based subsidiary, Knust-Godwin LLC, has validated Velo3D’s end-to-end AM technology in its Houston facility and is using its solutions to build production parts for its customers in the aerospace and oil and gas industries. SBO’s new Sapphire system will be located in the company’s Austrian headquarters and will enable the company to print complex metal parts in Inconel 718. SBO has EN 9100, ISO 9001, and ISO 14001 certifications, which enable it to develop and produce parts for aerospace customers, as well as other industries, while also meeting certain standards for quality and environmental management.
“By adding Velo3D’s innovative additive manufacturing solution to our capabilities, we will be able to expand into new markets and service new customers, helping them build metal parts that were previously thought impossible to create,” says Campbell MacPherson, SBO EVP of Advanced Manufacturing.
Related Content
-
DMG MORI: Build Plate “Pucks” Cut Postprocessing Time by 80%
For spinal implants and other small 3D printed parts made through laser powder bed fusion, separate clampable units resting within the build plate provide for easy transfer to a CNC lathe.
-
3D Printed Cutting Tool for Large Transmission Part: The Cool Parts Show Bonus
A boring tool that was once 30 kg challenged the performance of the machining center using it. The replacement tool is 11.5 kg, and more efficient as well, thanks to generative design.
-
Beehive Industries Is Going Big on Small-Scale Engines Made Through Additive Manufacturing
Backed by decades of experience in both aviation and additive, the company is now laser-focused on a single goal: developing, proving and scaling production of engines providing 5,000 lbs of thrust or less.