Kimya Working to Expand Range of Recycled High-Performance 3D Filaments
Kimya researchers are now targeting between 70% and 100% recycled materials in so-called high-performance filaments, without affecting the properties.
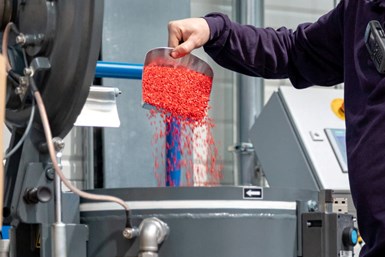
Kimya, Armor Group’s additive brand, continues expanding its range of recycled 3D filaments to turn waste into a genuine resource. Photo Credit: Kimya
Kimya, the Armor Group brand dedicated to additive manufacturing (AM), is continuing to expand its range of recycled 3D filaments within the framework of the FIL’REC project, which is tied to the Orplast plastics recycling venture. Orplast is ADEME’s financial incentive policy to support the use of recycled plastics.
For the third stage of the program initiated by ADEME, Kimya is focusing its research on developing a new offering of recycled high-performance 3D filaments by 2024. After its first successful participation in the Orplast program led to the commercialization of four new recycled filaments, Kimya is now targeting between 70% and 100% recycled materials in so-called high-performance filaments, without affecting the properties. With higher resistance levels and benefiting from physical-chemical properties (such as resistance to high temperatures and warping), it is said these materials are well suited for applications in the railway, automotive and aerospace industries.
“(Developing recycled high-performance materials) … is also an opportunity for us to extend our offering of engineering materials and to expand our range of eco-designed filaments,” says Nicolas Morand, Kimya R&D, innovation & industrialization manager.
The company is also working to create local and sustainable production ecosystems by taking part in the relocation of industrial projects. It’s beginning by initially collaborating mainly with French operators in this third stage of the Orplast project, from the sourcing of recycled plastic materials to the various stages of technical feasibility.
The Orplast program is designed to support those who fight against plastic waste. Lasting three years, the objective of the program is to provide financial support for plasturgists and manufacturers that convert raw materials into products by incorporating recycled plastics in the materials they use. Orplast provides the selected operators with research and investment support in order to adapt manufacturing processes to the integration of recycled plastics. The FIL’REC project is being funded by ADEME in order to remove certain technological obstacles impeding the use of recycled plastics.
Related Content
-
Next-Gen Horse Trailers to Be Built With Robotic 3D Printing
Double D Trailers is currently developing a prototype horse trailer that will be made with large-format additive manufacturing. The technology brings potential benefits for labor, weight and design features to this subset of recreational vehicles.
-
Machine Tool Drawbar Made With Additive Manufacturing Saves DMG MORI 90% Lead Time and 67% CO2 Emission
A new production process for the multimetal drawbar replaces an outsourced plating step with directed energy deposition, performing this DED along with roughing, finishing and grinding on a single machine.
-
Copper, New Metal Printing Processes, Upgrades Based on Software and More from Formnext 2023: AM Radio #46
Formnext 2023 showed that additive manufacturing may be maturing, but it is certainly not stagnant. In this episode, we dive into observations around technology enhancements, new processes and materials, robots, sustainability and more trends from the show.