GE Earns Air Force Airworthiness Qualification for Critical Jet Engine Part
Pathfinder with the USAF’s Propulsion Directorate and Rapid Sustainment Office (RSO) gathers momentum as it establishes its own qualification path for additively manufactured metal parts.
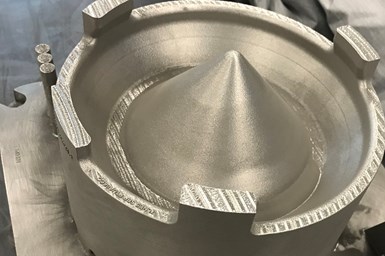
The cobalt-chrome sump cover for F110 engine was additively manufactured on a GE Additive Concept Laser M2 machine at the GE Additive Technology Center in Cincinnati, as part of collaboration with the U.S. Air Force’s Rapid Sustainment Office.
GE Aviation has received Engineering Change Proposal (ECP) approval from the U.S. Air Force (USAF) for an F110 additively manufactured sump cover. The F110 component is the latest milestone in the USAF and GE’s pathfinder Pacer Edge program and is the first engine component designed for and produced by metal additive manufacturing (AM) to be qualified by any U.S. Department of Defense entity.
“Much like the GE90 T25 sensor that was an FAA certification pathfinder for metal additive manufacturing for GE Aviation in commercial aerospace, the F110 sump cover sets a solid foundation for many more additively manufactured component qualifications with GE’s military customers,” says Matt Szolwinski, chief engineer and leader of GE’s Large Military Engineering team.
The company says that the Pacer Edge program is an important initiative for reducing risk and showcasing the application of AM in aerospace. “The ability to additively manufacture an aircraft engine part and gain military airworthiness is a significant step forward in growing the adoption of additive manufacturing in the Air Force,” says Nathan Parker, deputy program executive officer for the USAF RSO.
The Chief of Staff of the Air Force has challenged the group to ‘accelerate change or lose.’ “The entire Pacer Edge process is built around the ‘accelerate change’ philosophy, and the speed of the F110 sump cover development and airworthiness approval is evidence of that,” says John Sneden, director of the USAF’s Directorate of Propulsion. “The capability that Pacer Edge is demonstrating and proving will be a game changer to engine production and sustainment and will resolve many future Air Force readiness challenges.”
The company says that part of the key to the accelerated qualification — in under a year — was GE’s decade of metal additive engineering and manufacturing expertise. The team’s in-depth knowledge of commercial aerospace engine airworthiness for flightworthy 3D printed metal parts is proving instrumental in helping the USAF establish its own robust process validation and certification processes for military airworthiness.
Related Content
-
3D Printed NASA Thrust Chamber Assembly Combines Two Metal Processes: The Cool Parts Show #71
Laser powder bed fusion and directed energy deposition combine for an integrated multimetal rocket propulsion system that will save cost and time for NASA. The Cool Parts Show visits NASA’s Marshall Space Flight Center.
-
Additive Manufacturing Is Subtractive, Too: How CNC Machining Integrates With AM (Includes Video)
For Keselowski Advanced Manufacturing, succeeding with laser powder bed fusion as a production process means developing a machine shop that is responsive to, and moves at the pacing of, metal 3D printing.
-
This Drone Bird with 3D Printed Parts Mimics a Peregrine Falcon: The Cool Parts Show #66
The Drone Bird Company has developed aircraft that mimic birds of prey to scare off problem birds. The drones feature 3D printed fuselages made by Parts on Demand from ALM materials.