Essentium Acquiring Collider's DLP AM Technology
Company plans to advance Collider’s Programmable Tooling, which combines the speed of Digital Light Processing 3D printing and the material strength of injection molding.
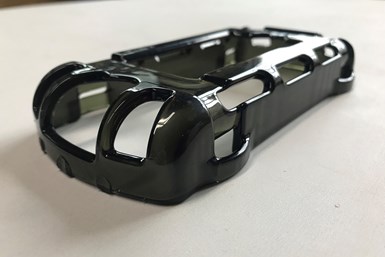
Collider’s Programmable Tooling combines the speed of DLP 3D printing and the material strength of IM.
Essentium Inc., a provider of industrial additive manufacturing (AM) has signed a letter of intent to acquire Collider, a developer of Programmable Tooling, which combines the speed of Digital Light Processing (DLP) 3D printing and the material strength of injection molding (IM). The addition of Collider to the Essentium portfolio is designed to drive new growth paths while enabling manufacturers to speed time to production of parts and innovation, the company says.
“We see significant opportunities in tooling for low volumes of parts and the ability to manufacture geometrically complex, custom parts on-demand and quickly,” says Jeffrey Lumetta, Essentium chief technology officer. “In addition, this represents Essentium’s first entrance into photopolymer AM technologies and will expand product offerings in several areas — especially when combined with our unique material science capabilities.”
According to the company, as manufacturers look to respond quickly to market changes, many are challenged with late-stage product development. Creating injection moldings or specific tooling for low-quantity parts production can be a costly and time-consuming process. Instead of a permanent, hard tooling mold, Collider’s DLP 3D printing technology creates a thin photopolymer shell, which is then injected with a variety of materials and cured through a chemical process. After some postprocessing, a production-quality part or mold is left.
Collider 3D printing technology is said to unlock an array of high-performance thermosetting polymers and composites, including polyurethanes, silicones, epoxies, polyesters, foamed resins and carbon fiber composites, as well as sintered metals and ceramics with one machine. The company says it has structural integrity on par with IM processes and creates high-detail aesthetic surfaces, enabling manufacturers to speed up the design process and obtain parts in a few hours rather than weeks.
Essentium aims to grow the technology by leveraging its expertise in material science and 3D printing machines. This could unlock enormous speed, economic and innovation advantages for manufacturers across consumer, medical, transportation, wearables, aerospace and industrial industries, the company says.
Related Content
-
This Drone Bird with 3D Printed Parts Mimics a Peregrine Falcon: The Cool Parts Show #66
The Drone Bird Company has developed aircraft that mimic birds of prey to scare off problem birds. The drones feature 3D printed fuselages made by Parts on Demand from ALM materials.
-
Aircraft Ducts 3D Printed in Composite Instead of Metal: The Cool Parts Show #68
Eaton’s new reinforced PEKK, tailored to aircraft applications, provides a cheaper and faster way to make ducts compared to formed aluminum.
-
3D Printed Lattices Replace Foam for Customized Helmet Padding: The Cool Parts Show #62
“Digital materials” resulting from engineered flexible polymer structures made through additive manufacturing are tunable to the application and can be tailored to the head of the wearer.