EOS, Grenzebach Strengthen Partnership for Efficient, Safe Additive Manufacturing
Partners seek to further advance the additive manufacturing of metal and polymer parts with the development of efficient, safe and holistic automation processes.
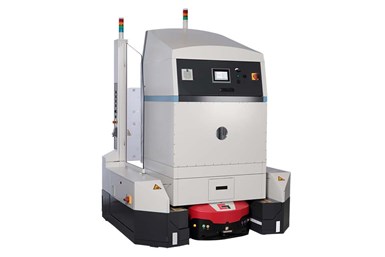
Inert Gas Container (IGC) with Docking Station (DOS). Photo Credit: EOS
To further advance the additive manufacturing (AM) of metal and polymer parts, technology provider EOS and automation specialist Grenzebach are strengthening their partnership to develop efficient, safe and holistic automation processes.
“It is essential for us to further automate and network industrial 3D printing as intelligently as possible with different processes,” says Dr. Marco Nock, EOS senior vice president business unit systems and innovation management.
Since the start of the collaboration, a variety of periphery equipment has been developed, including automation systems and transport solutions for the respective system platforms. In 2017, the NextGenAM project focused on creating fully automated series production of quality metal components. An aerospace and automotive manufacturer in Baden-Württemberg successfully used the automated solution which Grenzebach and EOS had jointly developed.
That led to more automation solutions for EOS machines in the metal sector, such as the unpacking station. The developed solutions in the metal sector were then adapted to the industrial 3D printing of polymer components. In the Polyline project, a fully automated cell was achieved and an automotive OEM customer from Bavaria tested the solution to verify that it met all requirements of the automotive industry. Within the scope of the project, the EOS P 500 will be equipped with the fully automated feeding of the exchange frames.
The partners are cooperating on further research and customer projects, developing individual configurations and deriving holistic process and production solutions to meet the requirements of common customers. The projects are focused on the highest possible utilization of the industrial 3D printer and the accompanying periphery, efficient and robust production processes, and optimal occupational health and safety production.
Grenzebach has also continued to extend its portfolio for industrial 3D printing, including 3D printer-specific automation and transport solutions such as automatic storage as well as bin picking and sorting solutions to further advance the automation of upstream and downstream process steps.
Related Content
-
3D Printed Spine Implants Made From PEEK Now in Production
Medical device manufacturer Curiteva is producing two families of spinal implants using a proprietary process for 3D printing porous polyether ether ketone (PEEK).
-
FDA-Approved Spine Implant Made with PEEK: The Cool Parts Show #63
Curiteva now manufactures these cervical spine implants using an unusual 3D printing method: fused strand deposition. Learn how the process works and why it’s a good pairing with PEEK in this episode of The Cool Parts Show.
-
3D Printed Lattices Replace Foam for Customized Helmet Padding: The Cool Parts Show #62
“Digital materials” resulting from engineered flexible polymer structures made through additive manufacturing are tunable to the application and can be tailored to the head of the wearer.