Desktop Metal Triples Manufacturing Capacity for Production System P-50
Company opens new in-house manufacturing facility to accelerate production to meet demand.
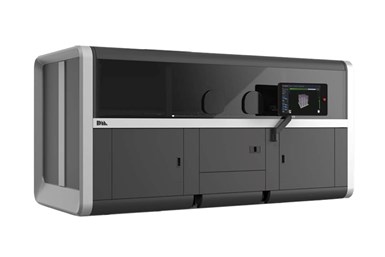
New facility is part of a strategic plan to accelerate the production ramp of Desktop Metal’s flagship Production System P-50 printer. Photo Credit: Desktop Metal
Desktop Metal has opened a new in-house manufacturing facility in Massachusetts that will more than triple the final assembly space currently dedicated to its Production System platform to meet robust demand for its metal 3D printing technology. This new facility is part of a strategic plan to accelerate the production ramp of Desktop Metal’s flagship Production System P-50 printer, which the company is currently engaged in component procurement and assembly of initial builds targeted for shipment in the fourth quarter of 2021.
“After a significant development cycle, we are experiencing growing, pent-up demand for our Production System P-50 solution,” says Ric Fulop, Desktop Metal founder and CEO. “As we continue to convert these opportunities, expanding our in-house final assembly capabilities has become a critical step to scaling deployment of our single pass jetting technology.”
This new facility in Massachusetts, in conjunction with the company’s contract manufacturers and suppliers, supports its ability to meet growing demand for high-volume applications. “We are now well-positioned to supply our global customers with the fastest metal 3D printing platform to enable cost-effective mass production via additive manufacturing,” Fulop says.
Created by the inventors of binder jetting and single-pass inkjet technology, the Production System is an industrial manufacturing platform powered by Desktop Metal’s single pass jetting technology. The company says it is designed to achieve speeds up to 100 times faster than those of legacy powder bed fusion additive manufacturing technologies and enable production quantities of up to millions of parts per year at costs competitive with conventional mass production techniques.
According to the company, the P-50 printer is paving the way for the mass production of end-use parts —unlocking throughput, repeatability and competitive part costs.
Related Content
-
What Is Neighborhood 91?
With its first building completely occupied, the N91 campus is on its way to becoming an end-to-end ecosystem for production additive manufacturing. Updates from the Pittsburgh initiative.
-
How Machining Makes AM Successful for Innovative 3D Manufacturing
Connections between metal 3D printing and CNC machining serve the Indiana manufacturer in many ways. One connection is customer conversations that resemble a machining job shop. Here is a look at a small company that has advanced quickly to become a thriving additive manufacturing part producer.
-
VulcanForms Is Forging a New Model for Large-Scale Production (and It's More Than 3D Printing)
The MIT spinout leverages proprietary high-power laser powder bed fusion alongside machining in the context of digitized, cost-effective and “maniacally focused” production.