Desktop Metal Qualifies Nickel Alloy In625 for High-Volume Additive Manufacturing
Company says alloy works with its production system binder jetting technology to enable mass production of strong parts that withstand high temperatures and extreme environments.
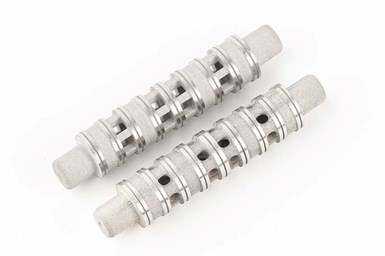
Desktop Metal’s IN625 can be an essential material for these hydraulic spools to ensure longevity and withstand highly corrosive environments. When produced using traditional manufacturing methods, the spool must typically be assembled from several machined components. With Production System technology, each hydraulic spool can be consolidated and printed as a single part instead of multiple components, significantly reducing the assembly labor costs as thousands can be printed at once with no user input. Photo Credit: Desktop Metal
Desktop Metal has qualified the use of nickel alloy IN625 for its Production System platform, which leverages patent-pending single pass jetting (SPJ) technology designed to achieve the fastest build speeds in the metal additive manufacturing (AM) industry.
The company says IN625 is a nickel-chromium superalloy characterized by high strength, resistance to corrosion and oxidation, excellent weldability, and ability to withstand extreme, elevated temperatures for parts under load. IN625 is a critical material used extensively in high-temperature aerospace applications, while its corrosion resistance under a range of temperatures and pressures also makes it an well suited for marine, power generation and chemical processing applications, the company says.
“As Desktop Metal continues to drive our internal R&D efforts to qualify more materials for the Production System platform, we are excited to offer customers an all-inclusive binder jetting solution to print fully characterized IN625 with excellent properties,” says Jonah Myerberg, Desktop Metal co-founder and CTO.
The company says that IN625’s high-temperature and corrosion-resistant properties are also well suited for flaring and sulfur incineration applications. “This will give us much more flexibility in innovative, additive manufacturing designs for some of our most difficult applications,” says Jason Harjo, director, mechanical and electrical design (Americas), Koch Engineered Solutions.
Desktop Metal’s materials science team has qualified and fully characterized IN625 printed on Production System technology in accordance with ASTM testing requirements. IN625 parts printed on the Production System platform not only eliminate the use of tooling and minimize material waste but also represent a significant decrease in production time and part cost compared to conventional manufacturing methods, the company says.
According to the company, its Production System is the fastest way to 3D print metal parts at-scale, achieving speeds up to 100 times faster those of legacy powder bed fusion AM technologies. It is also said it can enable production quantities of up to millions of parts per year at costs competitive with conventional mass production techniques.
Related Content
-
Binder Jetting Vs. Metal Injection Molding: The Cool Parts Show All Access
Alpha Precision Group, provider of both processes, discusses considerations that go into making this choice.
-
Video: Binder Jetting Production Workflow at Freeform Technologies
Additive manufacturing via binder jetting includes a sequence of downstream steps. During a visit to the Pennsylvania metal 3D printing part producer, I had the chance to walk through this process.
-
Chuck Jaws Achieve 77% Weight Reduction Through 3D Printing
Alpha Precision Group (APG) has developed an innovative workholding design for faster spindle speeds through sinter-based additive manufacturing.