3D Systems Acquires DP Polar
It is said DP Polar’s industrial-scale rotating build platform enables continuous, high-speed 3D printing of components across multiple processes for industrial and health care production applications.
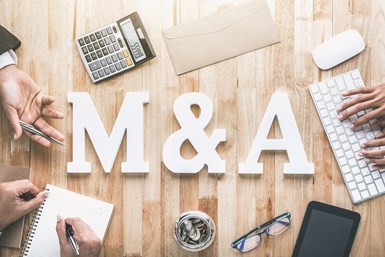
Photo Credit: Getty Images
3D Systems has entered an agreement to acquire DP Polar GmbH, the German-based designer and manufacturer of the industry’s first additive manufacturing (AM) system designed for high-speed mass production of customized components. Central to DP Polar’s continuous printing process is a large-scale, segmented, rotating print platform that eliminates the start/stop operations of virtually all AM platforms.
It is said traditional printers operate on a Cartesian Coordinate system in which the printhead moves sequentially from point to point throughout component production. With dp polar’s technology and polar coordinate control, the printheads remain stationary above the rotating platform, providing a continuous print process. This approach not only dramatically speeds component production but also minimizes wear and vibration associated with traditional printhead motion, the company says.
With this modular approach, the rotating platform can be mated with a variety of printing technologies and can even accommodate pick-and-place robotic systems that can embed electronics or other features into the body of the component as it is printed. With this acquisition, 3D Systems will leverage its polymer materials portfolio as well as Oqton’s software technology to bring true high-speed, mass production AM to a breadth of industries, including aerospace, automotive, foundries, consumer goods and health care.
“This acquisition is the next step in executing on our investment strategy to provide our customers with an industry-leading additive manufacturing solutions portfolio to address their critical applications challenges,” says Dr. Jeffrey Graves, president and CEO, 3D Systems. “DP Polar has designed a very unique system that provides true high-volume production. The ability to print a broad range of materials — alongside the printer’s modular design that enables multiple processes in one high-speed platform — not only increases productivity by orders of magnitude but also reduces the total cost of ownership.”
The printing process designed by dp polar enables simultaneous application of different materials to precisely define the desired performance properties in components — such as elasticity, hardness, temperature resistance or coloring — with high precision. It is said the high-speed AM solution can integrate preprocessing, production and postprocessing elements, and seamlessly connects with ERP systems. This enables end-to-end traceability and quality assurance which is vital for applications in highly regulated markets such as aerospace and health care.
“As the founder of DP Polar GmbH, I am very excited about the unique opportunity to work with a leading provider of highly professional 3D printing systems,” says Hans Mathea, DP Polar CEO, CTO and founder. “The synergy that results from the combination of our two companies is particularly valuable: the mass production solutions meet a range of industrially mature AM materials.”
Related Content
-
This Drone Bird with 3D Printed Parts Mimics a Peregrine Falcon: The Cool Parts Show #66
The Drone Bird Company has developed aircraft that mimic birds of prey to scare off problem birds. The drones feature 3D printed fuselages made by Parts on Demand from ALM materials.
-
Additive Manufacturing Is Subtractive, Too: How CNC Machining Integrates With AM (Includes Video)
For Keselowski Advanced Manufacturing, succeeding with laser powder bed fusion as a production process means developing a machine shop that is responsive to, and moves at the pacing of, metal 3D printing.
-
At General Atomics, Do Unmanned Aerial Systems Reveal the Future of Aircraft Manufacturing?
The maker of the Predator and SkyGuardian remote aircraft can implement additive manufacturing more rapidly and widely than the makers of other types of planes. The role of 3D printing in current and future UAS components hints at how far AM can go to save cost and time in aircraft production and design.