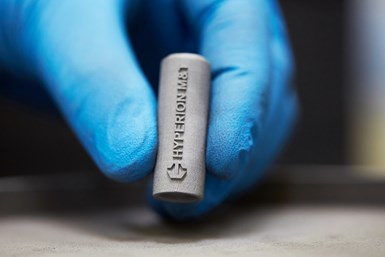
Carbide is one of the hardest materials, making it desirable for cutting tools and wear parts, but that also means its manufacturing processes and part designs are limited. 3D printing could enable design flexibility and rapid prototyping, but it would require an entirely new process with specialized materials, machine parameters, sintering methods and design considerations. Photo Credit: Hyperion Materials & Technologies
Because it’s one of the hardest materials, tungsten carbide is a popular choice for demanding surface-to-surface applications like cutting tools in machining, and wear parts in the fluid dispensing, oil and gas, aerospace, automotive and other industries. But this quality also means that carbide parts are difficult to produce. “Our customers are sometimes limited by the manufacturing processes that are available to make carbide and therefore, they are maybe compromising a bit on the design so that they can make a manufacturable part,” explains Biju Varghese, Vice President, Engineered Solutions Business and Global Research & Development at Hyperion Materials & Technologies, which provides materials science, engineering and manufacturing services for a range of materials and components, including those made of carbide.
Traditionally, Hyperion produces carbide parts through press and sinter processes. This method requires a punch and die set, which is typically also made of carbide via grinding and polishing (to ensure a smooth surface so the part doesn’t stick). It can take a week or two to produce these punch and die sets at the company’s internal tool shops. When it’s ready, the die set is filled with carbide powder, which is pressed or compacted to form a “green body.” The green part is then sintered to create a fully dense carbide part. Sometimes sintered parts require finishing operations, usually grinding, polishing or EDM due to the material’s hardness. Using this process, it can be extremely difficult to make certain carbide parts with complex features like fins and internal channels, and the use of tooling means it can be difficult to produce prototypes.
“With the emergence of 3D printing technology, especially in the metals side, we could see that our customers could benefit a lot from using this technology in terms of design flexibility, rapid prototyping and so on,” Varghese says. But in order to 3D print carbide, the company needed to develop an entirely new process with specialized materials, machine parameters, sintering methods and design considerations. And until recently, Hyperion’s only experience with 3D printing was a small polymer machine used to make certain fixtures. However, the company knew it could leverage its deep knowledge of the carbide production process, from material development to postprocessing, to establish a method for 3D printing carbide. So, it acquired a binder jetting system (the company wasn’t allowed to share which brand) and started to experiment.
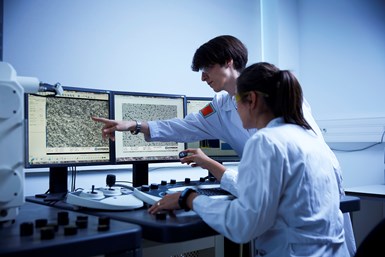
Hyperion developed a new, pre-densified carbide powder that was specially designed for 3D printing. Its existing materials were specifically developed for press-and-sinter processes, and 3D printing them would result in parts with the wrong properties and density. Photo Credit: Hyperion Materials & Technologies
Challenges
The first challenge Hyperion faced when developing 3D printing processes for carbide parts was to create a material. All of the company’s existing carbide powders had been specially formulated for press and sinter processes, and none of them were suitable for additive manufacturing (AM). “There's a lot of engineering and science that goes into it to make sure that particular powder flows into this sometimes complex mold, and it needs to fill into those cavities in the right way, and so on,” Varghese explains. He describes the particles in these materials as hollow spheres that get crushed together when they’re pressed. Because it lacks a compacting step, using these materials for AM “would be just like stacking a bunch of table tennis balls. The gaps between the balls will remain unfilled and you don't get the right density or material properties,” he says. “We had to figure out a way that we could fill all those empty spaces, and so we have a different powder.” Instead of filling a cavity, Hyperion had to use pre-densified powder and consider how that powder would flow work with the binder-applicator and roller to form solid parts in binder jetting.
With the material developed, Hyperion began experimenting with different settings to optimize the machine for printing carbide. “We had to develop parameters to give us a little bit more of an edge in terms of geometric tolerances” Varghese says. These involved adjusting the print speed, the recoater and the way the binder is dropped.
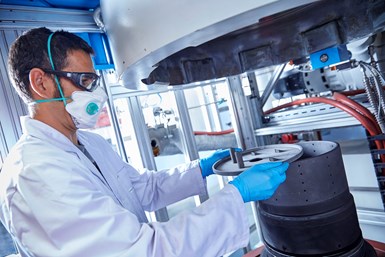
The company developed special sintering cycles for 3D printed carbide parts, and develop an understanding of how the materials behave during the sintering process. In order to minimize and reduce geometric deformation during sintering, Hyperion simulated and modelled the process using different finite element methods. Photo Credit: Hyperion Materials & Technologies
Once the company had green parts, it had to figure out how to sinter them. The new materials and part designs necessitated different sintering cycles than the ones used for pressed carbide parts. Building on its existing knowledge, it was able to develop a complex, proprietary sintering cycle for 3D printed parts. Varghese says that one of the biggest challenges of figuring out the sintering cycle was predicting the dimensional effects. All parts shrink during sintering, but as he points out, “that shrinkage is not uniform in every direction. You cannot arbitrarily scale it.” This makes it difficult to determine what the geometry of the green body should be, so that the part has the proper dimensions after sintering. There are also other risks during sintering, such as cracking. To figure this out, Hyperion spent a lot of time simulating and modeling the sintering process using different finite element methods to minimize or eliminate resulting geometric deformation.
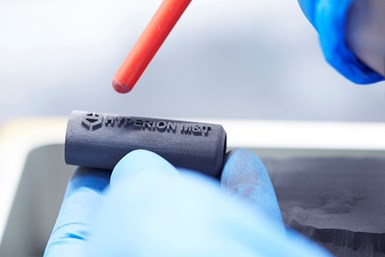
3D printed carbide parts have different design considerations than carbide parts made through press-and-sinter operations. For example, de-powdering, part handling and feature sizes need to be taken into consideration. Photo Credit: Hyperion Materials & Technologies
Design Considerations
In addition to different materials, printing and sintering processes, Varghese notes that 3D printed carbide parts have design considerations different from conventional carbide as well:
- De-powdering. “De-powdering is a major issue, especially the smaller and more intricate the internal channels are,” he says. “It’s not trivial,” especially when figuring out how to de-powder delicate parts with thin walls. Green parts are fragile and can break under too much pressure, so options like vacuums often won’t work. Hyperion has found that a combination of techniques, including specialized lances and forced airflow, work well for de-powdering 3D printed carbide parts.
- Part handling. 3D printing can produce intricate features, like thin fins, but this can make handling the green part challenging. Varghese says that the company looks to reinforce these types of features, or finds ways to redesign them so they’re more robust.
- Feature size. “We can pretty faithfully reproduce things in the millimeter to half a millimeter size range,” he says, “but anything below that, we find it difficult to consistently hold the shape of the feature.”
Applications
While Varghese thinks that 3D printing will be useful for rapidly prototyping carbide parts, he adds that he sees the biggest application being production of parts that can’t be made by traditional methods. “Most of the applications we are aiming for right now are focused on wear-type applications,” he says. The biggest markets for these parts are general industry, which includes “everything from drawing wire to nozzles to pumps and other fluid dispensing components, and oil and gas type applications, where you have very complex components that are used in all the drilling and exploration equipment.”
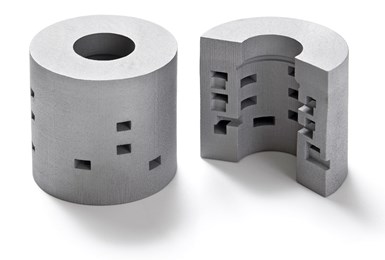
Hyperion 3D printed this carbide control component with features that would have been impossible to machine.
Photo Credit: Hyperion Materials & Technologies
One success so far has been a die for rod size reduction, which was re-designed to include internal recesses that could be packed with lubrication to make the process faster and more energy efficient. “We came up with a design that facilitated that and it has been very, very successful, and it was purely enabled because of additive manufacturing,” Varghese says. He points to another ongoing project that involves a 3D-printed carbide nozzle, which has special features to lock it into place, fin-like structures on the outside, and a curved internal channel with a chamber. He says this part is performing well in tests, but the company is working to make further improvements. Other potential applications Varghese envisions include toolholders with complex through-tool coolant channels and spare parts production.
Future Developments
Thus far, Hyperion has developed a general-purpose carbide grade for 3D printing (a 12% cobalt carbide that Varghese says has a wear performance that’s very close to traditional pressed and sintered carbide). The next step is to develop 3D printing materials with other specialized carbide grades. “One of the things we are known for in in the marketplace is for our highly specialized grades for different applications,” he says. These include grades that are specifically formulated to, for example, resist corrosion. “There's a whole list of grades that we use in the traditional carbide world, so we are systematically working through each one of those,” he explains. Additionally, Varghese says that Hyperion is considering larger machines to print more or larger parts, as well as multi-material printing capabilities.
Related Content
3D Printing Molds With Metal Paste: The Mantle Process Explained (Video)
Metal paste is the starting point for a process using 3D printing, CNC shaping and sintering to deliver precise H13 or P20 steel tooling for plastics injection molding. Peter Zelinski talks through the steps of the process in this video filmed with Mantle equipment.
Read MoreHow Norsk Titanium Is Scaling Up AM Production — and Employment — in New York State
New opportunities for part production via the company’s forging-like additive process are coming from the aerospace industry as well as a different sector, the semiconductor industry.
Read MoreAdditive Manufacturing Is Subtractive, Too: How CNC Machining Integrates With AM (Includes Video)
For Keselowski Advanced Manufacturing, succeeding with laser powder bed fusion as a production process means developing a machine shop that is responsive to, and moves at the pacing of, metal 3D printing.
Read More3D Printed Titanium Replaces Aluminum for Unmanned Aircraft Wing Splice: The Cool Parts Show #72
Rapid Plasma Deposition produces the near-net-shape preform for a newly designed wing splice for remotely piloted aircraft from General Atomics. The Cool Parts Show visits Norsk Titanium, where this part is made.
Read MoreRead Next
AM 101: What Is Binder Jetting? (Includes Video)
Binder jetting requires no support structures, is accurate and repeatable, and is said to eliminate dimensional distortion problems common in some high-heat 3D technologies. Here is a look at how binder jetting works and its benefits for additive manufacturing.
Read MoreLightweight Combustion Chamber for 3D Printed Rocket Engine: The Cool Parts Show #30
An engine for repeated trips to the moon is 3D printed in just three pieces from a metal matrix composite combining aluminum for weight saving with ceramic for high-temperature performance.
Read MoreDistribution Network Aims to Be the "Inventory Bridge" for Metal Powders
Recently launched KBM Advanced Materials connects metal powder suppliers to customers in additive manufacturing, metal injection molding and more.
Read More