A Total Plastic 3D Printing Process Designed for Production
Sponsored ContentFast, predictable and precise, HP’s Multi Jet Fusion additive manufacturing process is ideal for production applications. Now there’s a new addition to the family of printers designed for even higher volume environments, taking HP’s portfolio of digital manufacturing solutions to a new level.

When HP introduced the Multi Jet Fusion process in 2016 it was clear this is a process ideal for production. Inherently faster than laser-based powder bed AM systems, Multi Jet Fusion can fuse an entire layer in 8 seconds or less, an astonishing increase in speed compared to other plastic additive manufacturing methods. Moreover, Multi Jet Fusion offers uniquely predictable print times for any type of part and exceptional process controls to ensure high quality conformance. This drives optimized production and design freedom.
Now HP is pushing the envelope further with the addition of the 5200 Series 3D Printing Solution designed for even higher volume production environments. Combined, the HP family of printers radically extends the viability of production 3D printing in three critical ways:
- Manufacturing predictability — The Multi Jet Fusion printers can produce detailed functional parts with high dimensional accuracy, repeatability, and best-in-class isotropy at industrial standards of quality and efficiency.
- Breakthrough economics — Much faster than other precision plastic AM methods and with extremely high yield rates, the process is cost competitive with a variety of more traditional manufacturing processes, yet more flexible and agile.
- Expand into new markets — With the rapid development of new materials for Multi Jet Fusion, the process can serve an increasingly wider range of applications.
It’s a 3D printing solution that’s competitive, not just with other AM processes, but with injection molding and in some cases CNC machining. You can still use it for prototyping, but now with a process that is exactly representative of the full production environment.
Moreover, Multi Jet Fusion is a major element of HP’s suite of digital manufacturing solutions as well as the company’s vision for the next industrial revolution where more sustainable manufacturing technologies can accelerate a the path to a low waste circular economy.
How HP’s Multi Jet Fusion process works.
The Multi Jet Fusion Process
Why is Multi Jet Fusion so much faster? Rather than using single point lasers to fuse material, a multiple jet print head, that spans the width of the powder bed, deposits droplets of fusing and detailing agents as it sweeps across the length of the bed. The fusing agent serves as a heat-absorbing ink, making the powder more prone to melting. The detailing agent enables a cooling effect, providing crisp edges around the melted area and preventing the melt pool from bleeding into the loose powder. Then an array of infrared lamps melt the areas defined by the agents. Powder is then distributed for the next layer, and the process repeats until the part is complete. Because the powder holds the parts as they grow, supports are not necessary, which allows for greater design freedom and enables larger quantities of parts to be produced at once.
This build method is what makes Multi Jet Fusion so much faster than other polymer Multi Jet Fusion processes. An entire layer is built with a single pass of the print head which takes just 8 to 10 seconds, regardless of the number of parts or the volume of material being fused. Overall, Multi Jet Fusion is much faster than other laser-based processes.
Multi Jet Fusion also delivers high quality parts. The highly controllable process results in quality surface finishes, fine feature resolution and more consistent mechanical properties when compared to laser-based powder bed processes. And because of the ability to isolate the heating areas from lower layers of the build, there is less process induced warpage of parts. HP says Multi Jet Fusion also produces functional parts with best-in-class isotropy, meaning the mechanical properties of the part perform equally well under forces of compression or tension.
Predictability And Process Control

The >Multi Jet Fusion process allows multiple parts to be printed at a time without supports and with no sacrifice in speed.
HP says that the Multi Jet Fusion process can deliver accuracy and repeatability that rivals industrial tooling. And they are talking about being able to maintain those standards, not just across tens of parts, but across 10,000 parts or more, which is why this process is a real alternative to injection molding in many applications, and without the expense and time required to build molds.
That’s a big claim, so how do they do it? It begins with the HP SmartStream 3D Build Manager software that quickly prepares jobs for printing. The printers are also integrated with Autodesk Netfabb, Materialize, and Siemens NX 3D printing solutions.
On the printer, HP 3D Process Control software is used to quickly achieve and maintain dimensional accuracy and repeatability. A user-initiated calibration process is executed where test parts are built and measured. Any deviations from the desired dimensional model are entered, which allows the software to target the variability that occurs with any specific device or job. The software then creates a calibrated profile that automatically compensates in the build program. This profile can be stored in the software library so that consistent process controls can be applied with different operators and jobs.
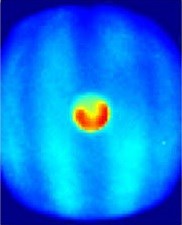
Thermal sensing cameras monitor the heat profile of the process and the system automatically compensates for unwanted conditions.
Thermal control of the process is monitored with a closed loop system with cameras that monitor heat in the workpiece at some 5000 points across the print bed. Deviations from the desired parameters are also automatically compensated for with adjustments to lamp intensity and/or the amount of agent applied. With HP’s latest generation sensor technology the resolution of these cameras has been increased fivefold, allowing for significantly finer process control. Also, the newest lamp array includes redundant units. If a single lamp fails, another automatically takes its place without interruption to the 3D printing process.
Moreover, the system can learn over time. During a part run a sampling of parts are measured. When deviations are detected, they are entered into the printer control which then automatically adjusts agent placement and volume as well as lamp intensity to further fine tune the process. This capability can improve accuracy by as much as 25% over the initial build program.
How HP 3D Process Control Software works
All of these elements finally bring plastics 3D printing into the realm of statistical process control. Rather than full final part inspection, as has been customary with many polymer AM processes, a statistical sampling can be used to monitor dimensional part quality. Many parts can be held to a CPK of 1.33 (67 nonconforming parts per million) or less, depending of course on the tolerances of the part.
Breakthrough Economics
Among the greatest barriers to wider adoption of AM for production has been cost, and this is where the 5200 Series production system offers dramatic improvements over what was possible before. Certainly a faster printing process and higher levels of quality conformance are major contributors to increasing yield. But how HP has integrated the entire production system further increases output by better utilization of the printing equipment.
The HP 5200 Series 3D Printing Solution
The system consists of the printer, a portable build unit, a processing station and natural cooling units. Here’s how it works:
- The build unit is inserted into the processing station for material loading. Fresh and reused material is mixed and loaded into the build unit in a clean automated process.
- The build unit is inserted into the printer. Preprint and in-printer checks are completed and production can start.
- When job is complete the build unit is inserted back into the processing station for cooling, or the finished job is loaded into a natural cooling unit. The processing station cools parts about three times faster. But transferring the build to a natural cooling unit immediately frees the processing station to move on to the next job, enabling greater throughput and better utilization of the equipment.
- Once cooled, the job can be unpacked and any unused material recovered for reuse.

The 5200 consists of, from left, a portable build unit, printer, processing station, and natural cooling units.
While a 3D printing shop using this equipment can still appear to be as clean as a lab, it is nonetheless a full production system. With the ability to accurately predict build times and yields, to process accurate parts much faster than other AM processes, to produce multiple parts in a single build process, and to keep printers working almost continually, the economics of using additive manufacturing for production parts is dramatically altered. Add in the ability to turn assemblies of metal or plastic components into a single 3D printed part, and cost reductions become possible that were unimaginable just a few years ago.
Expand into New Markets

This is a part for one of HP's printers. By replacing the metal parts assembly (left) with a single 3D printed part (right), the cost for this component went from $354 to $26.
While some may still see production AM as destined to serve niche, short run markets, HP has a much broader vision. In particular they see the 5200 series system working side by side with injection molding machines at custom plastics processors and as a complement to CNC machining at metalworking job shops. These printers will certainly deliver short lead times perhaps, particularly in comparison to injection molding, but not be relegated just to short runs. Moreover, because the capacity of HP 3D printing systems is so predictable, it is easy to scale up as more parts or higher volumes are added to the mix. This provides great opportunities for parts suppliers to broaden their capabilities and grow their business.
A key to serving new markets is developing new materials, and HP has devoted great resource internally and with partners to expand the material options for functional parts.
New grades include:

HP 3D High Reusability PA 11
Designed for high impact resistance and ductility, this thermoplastic material also offers high material reusability of surplus powder.

HP 3D High Reusability PA 12
A lower cost thermoplastic that’s good for general purpose applications, also with high material reusability.

BASF Ultrasint™ 3D TPU01
A multipurpose TPU material with elastomeric properties for accurate, flexible parts.
In addition to BASF, HP is working with other third parties on materials development including Arkema, Dressler Group, Evonik, Henkel, Lehmann & Voss, Lubrizol and Sigma Design. Go here for more on HP 3D printing materials.
The HP 3D Center is designed to further assist users to make the most productive use of their additive manufacturing investment. All the printing hardware is connected to this cloud-based application which provides real-time information on:
- Productivity of printer: time spent printing, cooling, idle, off.
- Tracking of jobs: agents used, starting time, packing density, recycled material used.
- Notifications on errors, maintenance and job status sent via email.
- Current status of Multi Jet Fusion devices: printers, processing stations, build units and cooling frames.
- Current status of jobs with location and state.
The data collected by the 3D center can be used in a variety of ways. It can reduce downtime by identifying common problems which can then be addressed before they occur. It can reduce idle time with proactive notifications. It can improve cost control and materials planning with tracking of variable costs such as powder and agent usage. And it can improve quality control and reduce unplanned production interruptions through better maintenance scheduling.
These functions are great examples of how HP has systematically thought through the entire requirements of AM production. Profitable volume parts manufacturing isn’t just about having great equipment. It’s also about making the most productive use of that equipment, day in and day out. The HP 5200 Series 3D Printing Solution delivers both.
Driving More Sustainable Digital Manufacturing Solutions
HP’s broader view is that digital manufacturing solutions contribute much more than just finding better ways to make a part. It’s the way to drive toward a more sustainable economy.
This year, HP President and CEO Dion Weisler wrote this for the World Economic Forum:
“Digital manufacturing can create a brighter future for our planet by reducing the environmental impacts of production, shortening and simplifying traditional supply chains, unlocking new sustainable industries and accelerating a more circular and low-carbon economy. It has the potential to offer cleaner and safer jobs for workers, enabling greater well-being and opportunities for people everywhere. Digital manufacturing can also be a powerful force for social and economic good in our global communities by enabling new business models, the creation of new local jobs, and innovative new solutions to address our most challenging issues.”
That’s a big challenge. This company is already on the way.
Go here for more information on HP 3D Printing Solutions.