Velo3D Qualifies New Superalloy for Use in Its Sapphire Printers
New nickel-based Höganäs Amperprint 0233 Haynes 282 powder enhances the capabilities of Velo3D’s end-to-end solution for customers in oil and gas, aviation, energy, space and other high-value applications.
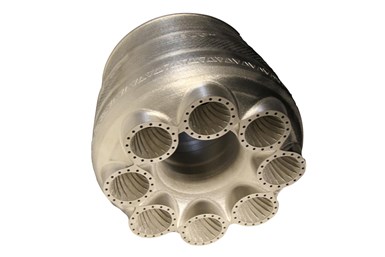
Combustor liner made using Amperprint 0233 Haynes 282 powder from Höganäs. The part features 23,000 unique holes for optimized air-to-fuel ratios and internal channels for regenerative cooling. The part is shown as printed, with no supports. Photo Credit: Velo3D
Velo3D Inc. has qualified the nickel-based superalloy powder Amperprint 0233 Haynes 282 for use in its Sapphire printers. The powder was produced by metal powder producer Höganäs AB under license from Haynes International Inc., and is designed for high creep strength, thermal stability, weldability and fabricability not commonly found in other alloys.
The company says the material is well suited for high-temperature structural applications like energy generation, gas turbines and space launch vehicles to build parts such as heat exchangers, combustors, nozzles, combustion liners, rocket engines and shrouded impellers.
The first Sapphire printer utilizing the Amperprint 0233 Haynes 282 powder will be operated by Duncan Machine Products (DMP), a contract manufacturer based in Duncan, Oklahoma. The system will be the seventh in DMP’s fleet of Velo3D Sapphire printers.
“Our goal at Velo3D is to enable engineers to build the parts they want without compromising on the design or quality,” says Benny Buller, Velo3D CEO and founder. “Qualifying new powdered metals, like Amperprint 0233 Haynes 282, for use in our end-to-end solution, further expands what’s possible with our additive manufacturing technology. Our partners at Höganäs provide materials of the highest quality, and I look forward to seeing what our customers build using this amazing alloy.”
Powdered nickel-based superalloys, like Amperprint 0233 Haynes 282, are often used to print parts for use in high-temperature applications due to the alloy’s resistance to cracking and its ability to operate at near-melting-point temperatures. This tolerance enables parts printed with the alloy to be used in vacuum, plasma and other demanding applications. Its high weldability makes the powder well suited for parts in larger systems because of its ability to be welded to other components.
Höganäs specializes in creating powders for additive manufacturing, delivering products with consistent spherical shape, tight control on chemistry and enhanced flowability. The powders are made using the purest materials with very precise compositions of trace elements that give the metals their unique properties, the company says.
Related Content
-
At General Atomics, Do Unmanned Aerial Systems Reveal the Future of Aircraft Manufacturing?
The maker of the Predator and SkyGuardian remote aircraft can implement additive manufacturing more rapidly and widely than the makers of other types of planes. The role of 3D printing in current and future UAS components hints at how far AM can go to save cost and time in aircraft production and design.
-
Beehive Industries Is Going Big on Small-Scale Engines Made Through Additive Manufacturing
Backed by decades of experience in both aviation and additive, the company is now laser-focused on a single goal: developing, proving and scaling production of engines providing 5,000 lbs of thrust or less.
-
3D Printed NASA Thrust Chamber Assembly Combines Two Metal Processes: The Cool Parts Show #71
Laser powder bed fusion and directed energy deposition combine for an integrated multimetal rocket propulsion system that will save cost and time for NASA. The Cool Parts Show visits NASA’s Marshall Space Flight Center.