SLM Solutions’ Free Float Software Reduces 3D Printing Support Structures
Software is said to give users the ability to design bolder, freer and with fewer limitations to work faster and more productively.
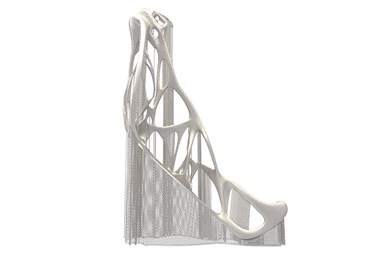
Reducing or removing supports gives users more design freedom with fewer limitations to work faster and more productively.
SLM Solutions’ Free Float software used for the creation of metal components empowers the creation of previously impossible designs and lower costs, the company says. The software is said to reduce supports and, in some cases, remove them completely without increasing build time, thereby enabling increased productivity, reduced overall material usage and minimized end-part cost to achieve industrial-scale production.
According to the company, the software also enables better part quality, sharper edges and a smoother finish. Free Float is said to give users the ability to design bolder, freer and with fewer limitations to work faster and more productively.
Support structures can sometimes limit the design of the main component and can be a substantial section of the overall part volume, increasing material usage which, by default, increases cost. The supports also need to be removed later during the postprocessing phase. Those factors led SLM Solutions to search for a support-free alternative.
Free Float was first discovered in 2017 as as research project byproduct with further research and development leading to the current software. The company says the software’s vector technology establishes thermal management that significantly decreases net build time while simultaneously enhancing part quality, especially in the case of overhang areas, which can now free float like the branches of a tree.
The software is designed to offer seamless useability with three profiles — low, medium and high — to give users their desired outcomes. Free Float can be retrofitted on many previously built systems, including the SLM 280 Production Series, the SLM 280 2.0, the SLM 500, the SLM800 and the NXG Xll 600.
Related Content
-
Spherene Creates Metamaterial with Geometry Derived from Spheres
An algorithm developed by Spherene Inc. generates Adaptive Density Minimal Surfaces (ADMS) as a self-supporting infill strategy that can be used to reduce mass and manage material properties in 3D printed parts.
-
3D Printed "Evolved Structures" for NASA Exoplanet Balloon Mission: The Cool Parts Show #61
Generative design creates stiff, lightweight brackets for EXCITE mission monitoring planets orbiting other stars. The Cool Parts Show visits Goddard Space Flight Center.
-
3D Printed Cutting Tool for Large Transmission Part: The Cool Parts Show Bonus
A boring tool that was once 30 kg challenged the performance of the machining center using it. The replacement tool is 11.5 kg, and more efficient as well, thanks to generative design.