SLM Solutions, Burgmaier Introduce Case-Hardening Steel for AM Tooling, Hybrid Manufacturing
Burgmaier introduces case-hardening steel 16MnCr5 to additive manufacturing and develops a hybrid additive manufacturing process using the SLM280.
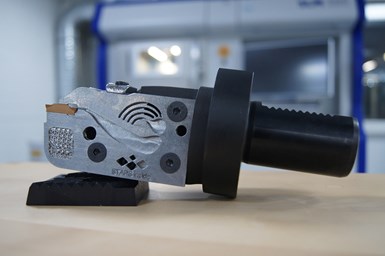
Burgmaier says its hybrid manufacturing technique using various steels such as 1.2709 or 16MnCr5 enables it to manufacture with the highest precision.
Additive Manufacturing (AM) provider SLM Solutions and high-precision metal parts processor Burgmaier have been working together for more than three years to redefine what is possible in part processing to open new possibilities in the tooling industry and hybrid manufacturing.
With the help of SLM’s AM technology, Burgmaier is pushing the limits for innovative tooling with 16MnCr5 — a favorite material for the tooling industry, the company says. It combines a very hard surface with a ductile core, and various heat treatments can flexibly adjust its characteristics to meet the customer’s needs. Burgmaier has established a hybrid manufacturing technique using various steels such as 1.2709 or 16MnCr5 — an innovation it says enables it to manufacture with the highest precision.
The introduction of case-hardening-steels to AM can be a game changer where hard-wearing designs are now possible — from lightweight tools with flexible cooling channels to resistant and cost-efficient molds. The company says its hybrid manufacturing process includes an innovative, self-developed system to clamp various base bodies and a standardized approach to manufacture the parts additively in an SLM 280, enabling single-use and series production with the highest accuracy. Burgmaier says it achieves a positioning and repeating accuracy of fewer than 0.05 millimeters and a high-quality joint of the base body and the AM part.
At the heart of the partnership is the SLM280, a multilaser, closed-loop powder handling system which the company says is well suited for medium- to high-volume metal part production and prototyping. The multilaser system is said to build at an 80% faster rate than a single laser, and the bidirectional powder recoating is said to boost productivity by reducing overall manufacturing time. This material flexibility makes it a well suited build companion for several industries, from aviation and aerospace to automotive and energy.
Related Content
-
VulcanForms Is Forging a New Model for Large-Scale Production (and It's More Than 3D Printing)
The MIT spinout leverages proprietary high-power laser powder bed fusion alongside machining in the context of digitized, cost-effective and “maniacally focused” production.
-
How Norsk Titanium Is Scaling Up AM Production — and Employment — in New York State
New opportunities for part production via the company’s forging-like additive process are coming from the aerospace industry as well as a different sector, the semiconductor industry.
-
Additive Manufacturing Is Subtractive, Too: How CNC Machining Integrates With AM (Includes Video)
For Keselowski Advanced Manufacturing, succeeding with laser powder bed fusion as a production process means developing a machine shop that is responsive to, and moves at the pacing of, metal 3D printing.