Farsoon FS273M System Offers Versatile Production for Larger Volume Parts
System offers an industrial-sized 275 × 275 × 355 mm build envelope as well as versatile single or dual laser options for improved productivity and efficiency.
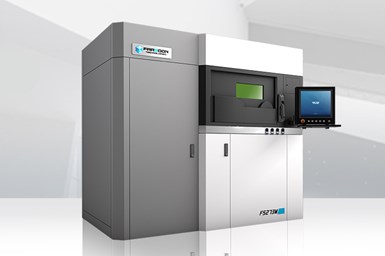
The FS273M is a powerful and versatile production tool of larger volume parts for a wide range of industrial metal materials.
Farsoon’s FS273M metal system offers single or dual laser options for commercial orders and is designed to address productivity, cost-efficiency and industrial workflow in metal additive manufacturing (AM). With an industrial-sized 275 × 275 × 355 mm build envelope, the FS273M is a powerful and versatile production tool for larger volume parts with a wide range of industrial metal materials, the company says.
The system is the next generation of Farsoon’s FS271M medium-sized metal system. The company says the system is optimized for improved productivity and performance. Updates include a streamlined metal production workflow for a wide range of industrial metal materials. The advanced dual-laser scanning strategy and calibration algorithms is said to offer an improved build volume rate by up to two times compared to the single-laser configuration. The enhanced communication signal control and the recoater design are said to enable robust operational speeds and stable powder delivery throughout the whole manufacturing process.
According to the company, the FS273M offers improved cost performance for an industrial production platform. Advanced digital optics system, robust control and truly open parameters are said to enable the user unparalleled freedom in processing capability. It is designed to achieve highly detailed, functional parts while maintaining a cost competitive advantage. Compact machine design enables denser, flexible factory layout for maximum throughput yield per floor area at an economical additive production cost.
The FS273M features an integrated, long-lasting filtration system enabling extended operation time for longer builds and reduced cost of filter changes. Features such as a preheated base-plate, robust recoating operations, removable overflow containers and a powder supply sufficient for a full build ensure the ease of operation and good serviceability.
Related Content
-
Why AM Leads to Internal Production for Collins Aerospace (Includes Video)
A new Charlotte-area center will provide additive manufacturing expertise and production capacity for Collins business units based across the country, allowing the company to guard proprietary design and process details that are often part of AM.
-
VulcanForms Is Forging a New Model for Large-Scale Production (and It's More Than 3D Printing)
The MIT spinout leverages proprietary high-power laser powder bed fusion alongside machining in the context of digitized, cost-effective and “maniacally focused” production.
-
Additive Manufacturing Is Subtractive, Too: How CNC Machining Integrates With AM (Includes Video)
For Keselowski Advanced Manufacturing, succeeding with laser powder bed fusion as a production process means developing a machine shop that is responsive to, and moves at the pacing of, metal 3D printing.