Farsoon, Evonik Collaborate on INFINAM Thermoplastic Copolyester
INFINAM TPC (thermoplastic copolyester) is a ready-to-use, elastomer-grade material for powder bed fusion 3D printing that can enable customers to unlock new markets and applications.
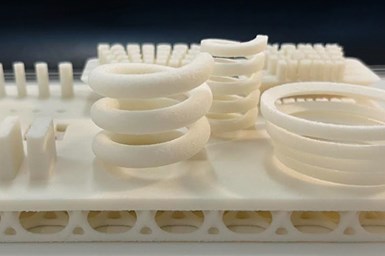
INFINAM TPC produced on the Farsoon 252P Series Platform. Photo Credit: Farsoon
Specialty chemical company Evonik and industrial 3D printer manufacturer Farsoon have collaborated to bring INFINAM TPC (thermoplastic copolyester) to market. The product is a ready-to-use elastomer powder material which expands the material library for the additive manufacturing industry, providing ways for customers to unlock new markets and applications.
Process testing for the INFINAM TPC material was conducted at the Farsoon Americas Demo Center located in Austin Texas. Committed to an open systems philosophy that gives customers the freedom to choose materials for their 3D printing applications, the two companies each contributed their expertise to ensure the material is thoroughly tested and tuned to produce repeatable benchmark parts with optimal mechanical properties.
The teams supported each other for test builds in X, Y and Z orientations at varying material refresh rates to successfully hone in machine parameters to produce accurate material properties reflected on Evonik’s material data sheets. “We see both strength and flexibility in this new TPC material,” says Ray Jones, applications and technical presale specialist at Farsoon Americas. “It is of excellent elasticity and is easy to process with Farsoon’s powder bed fusion technology. Postprocessing is efficient as well, from breakout and media blasting to sieving.”
It is said INFINAM TPC is the first high-performance flexible thermoplastic co-polyester powder on the market. Parts printed with the TPC are said to have excellent tear strength, elongation at break, impact resistance and rebound! TPC prints consistently and reliably offers easy postprocessing, and brings great material properties for a wide variety of applications in markets, including automotive, sporting goods and medical.
“We are very happy to work with the material experts at Evonik on their new TPC material,” says Don Xu, Farsoon America managing director. “With Farsoon’s open systems, we along with Evonik are able to produce parts with excellent elastic properties, enabling us to provide our customers with an even greater choice when it comes to material selection,”
Evonik says it believes in open source platforms as a market growth booster to unbound 3D printing at scale. “An open technology approach also meets our material development focus on ready-to-use, high-performance materials for main 3D printing technologies,” says Dr. Arnim Kraatz, Evonik director of powder bed fusion. “Having successfully qualified our PA613 powders on Farsoon’s machines two years ago, we are now jointly entering the market for elastomer-based 3D applications. This will open up new opportunities for users to push boundaries of 3D printing by being able to manufacture tough parts with reliable and easy processing.”
- Read how Farsoon’s Quad-Laser Flight technology maximizes production yields. The Quad-laser Flight technology on the HT1001P large-format platform offers an enhanced manufacturing speed to maximize production yield and lower manufacturing cost per part.
- Learn about Evonik’s three Infinam photopolymers which are designed for use in common UV-curing 3D printing processes such as stereolithography (SLA) or Digital Light Processing (DLP).
Related Content
-
3D Printed Spine Implants Made From PEEK Now in Production
Medical device manufacturer Curiteva is producing two families of spinal implants using a proprietary process for 3D printing porous polyether ether ketone (PEEK).
-
Understanding PEKK and PEEK for 3D Printing: The Cool Parts Show Bonus
Both materials offer properties desirable for medical implants, among other applications. In this bonus episode, hear more from Oxford Performance Materials and Curiteva about how these companies are applying PEKK and PEEK, respectively.
-
Aircraft Ducts 3D Printed in Composite Instead of Metal: The Cool Parts Show #68
Eaton’s new reinforced PEKK, tailored to aircraft applications, provides a cheaper and faster way to make ducts compared to formed aluminum.