ExOne Launches X1 Tooling Industrial-Grade 3D Printed Tooling Solutions
X1 Tooling offers manufacturers fast, affordable and local tooling options for the final production of metal, plastic and composite designs.
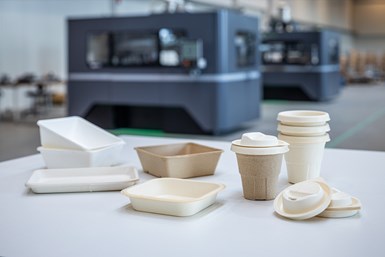
X1 MetalTool was used to produce tooling for Sweden-based Celwise’s molded fiber products.
The ExOne Co., a global provider of industrial sand and metal 3D printers using binder jetting technology, is launching X1 Tooling, a broad portfolio of industrial-grade 3D printed tooling that includes new solutions for plastic injection molding or forming, laying up composites, casting metals, and more.
The X1 Tooling line is designed to offer tooling options that speed up delivery times and bring tooling closer to the point of final production. Users that 3D print their tooling can help eliminate supply chain issues and make themselves more sustainable, with less shipping and other forms of waste. This fast, flexible tooling portfolio includes six new, affordable tooling applications, the company says.
For plastic production, X1 offers two options: X1 MetalTool is a new 3D printed metal tooling option which has passed preliminary tests to replace standard steel or aluminum tooling for plastic injection molding, blow molding and other plastic forming applications. It is available in 420i (said to be a highly durable and affordable steel-bronze matrix), as well as 316L stainless steel, M2 tool steel and more. This tooling can be finish machined, acid etched and polished to a diamond finish, and is well suited for complex inserts. The second option is X1 ThermoForm which involves a 3D printed sand form infiltrated with a durable resin and coated to create small- to large-format molds for a variety of thermoforming applications, such as vacuum forming, compression molds, foam molding and more.
For composite production, X1 offers X1 Layup and X1 Washout. X1 Layup involves a 3D printed sand form infiltrated with a durable resin and coated for high-precision, high-temperature composite layup applications. It offers dimensional tolerances of ±0.025" and the tooling can be precision machined if needed. X1 Washout is a 3D printed sacrificial tooling that washes out with tap water after traditional layup and autoclaving of composite materials, including carbon fiber. It is a sand form 3D printed with a water-soluble binder and surface coated. It is well suited for ducting, mandrels and other designs with trapped geometries.
For metal production, X1 offers three options: X1 SandCast delivers sand tooling in a variety of sand types and binders, including sustainable inorganic formulas for high-quality aluminum castings. X1 MetalTool, a tool for plastic forming applications, can also be used to directly 3D print end-of-arm tooling, and rugged, perishable or consumable tools in a variety of metals, including tool steels. While still in development, X1 DieMold is used in rugged die molds 3D printed in H13 tool steel and is currently being fast-tracked with several global manufacturers after passing proof-of-concept tests.
All sand- and sand-infiltrated tools are produced using ExOne S-Max series printers with build volume measuring 1,800 × 1,000 × 700 mm (70.9" × 39.4" × 9.84"). X1 MetalTool and X1 DieMold tools are 3D printed in an X1 25Pro with build volume of 400 × 250 × 250 mm (15.75" × 9.84" × 9.84"); development is underway for printing in the larger X1 160Pro.
Related Content
Foundry Lab: How Casting in a Day Will Improve the Design of Metal Parts (Includes Video)
The company’s digital casting process uses 3D printing, but the result is a cast part. By providing a casting faster than a foundry, the company says effective prototyping is now possible for cast parts, as well as bridge production.
Read MoreMantle: 3D Printed Molds Address Plastics Industry Lead Time and Skills Shortage
Company now shipping production systems. Steel mold tooling from its TrueShape process can be printed, shaped and sintered in days, and with fewer steps, compared to weeks of lead time for molds made conventionally.
Read MoreQ&A With Align EVP: Why the Invisalign Manufacturer Acquired Cubicure, and the Future of Personalized Orthodontics
Align Technology produces nearly 1 million unique aligner parts per day. Its acquisition of technology supplier Cubicure in January supports demand for 3D printed tooling and direct printed orthodontic devices at mass scale.
Read MoreIn "Hybrid" FIM Process, 3D Printing Complements Injection Molding
In a recent case study, Alpine Advanced Materials partnered with Nexa3D to produce 3D printed tooling for injection molded composites. Utilizing Nexa3D’s XiP desktop 3D printer and its Freeform Injection Molding process, Alpine was able to reduce prototype tooling production time and cost alike for its customers.
Read MoreRead Next
3D Printed Polymer EOAT Increases Safety of Cobots
Contract manufacturer Anubis 3D applies polymer 3D printing processes to manufacture cobot tooling that is lightweight, smooth and safer for human interaction.
Read MoreAlquist 3D Looks Toward a Carbon-Sequestering Future with 3D Printed Infrastructure
The Colorado startup aims to reduce the carbon footprint of new buildings, homes and city infrastructure with robotic 3D printing and a specialized geopolymer material.
Read MoreCrushable Lattices: The Lightweight Structures That Will Protect an Interplanetary Payload
NASA uses laser powder bed fusion plus chemical etching to create the lattice forms engineered to keep Mars rocks safe during a crash landing on Earth.
Read More