Desktop Health Launches Metal Binder Jetting for Dental Labs
The Shop System is designed to offer dental labs a high-speed, turnkey metal binder jetting solution to deliver faster and more cost-effective chrome cobalt production capabilities for bridges, crowns, partial dentures and more.
Share
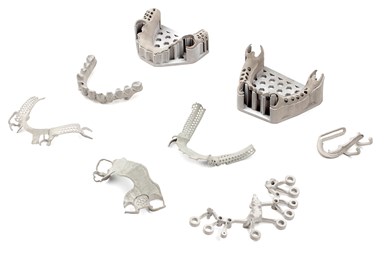
Dental applications 3D printed in chrome cobalt on Shop System.
Desktop Health, a healthcare business within Desktop Metal dedicated to developing 3D printing and biofabrication solutions for personalized medicine, is expanding its dental technology portfolio to include a turnkey metal 3D printing solution for dentistry along with the launch of chrome cobalt for use in dental applications.
The company says its Shop System metal binder jetting solution is now available to dental labs for preorder to deliver superior surface finish and resolution, and offer a promising pathway for custom dental appliances and surgical guides. The Shop System is said to bring mass customization through 3D printing to the dental lab, eliminating labor costs associated with machine programming required for CNC milling, which is typically a common manufacturing process for producing metal dental components.
The Shop System is designed to offer dental labs a high-speed, turnkey metal binder jetting solution to deliver faster and more cost-effective chrome cobalt production capabilities for bridges, crowns, partial dentures and more. The system is able to print up to 32 partials in less than four hours, as compared to the nearest competitive system which supports up to 10 partials in 9 ½ hours, the company says.
In addition, metal parts on the Shop System print fully supported in the powder bed and feature hand-removable sintering setters, thereby drastically reducing labor time and costs associated with postprocessing parts printed on laser-based 3D printing systems. By reducing postprocessing and providing high throughput printing, the Shop System can drive down part costs for custom dental applications, such as partials, to as low as one-third the cost that can be achieved for comparable part quantities produced using laser-based 3D printing systems, the company says.
The Shop System solution includes all the software, hardware and materials a dental lab needs to begin binder jetting dental appliances — from build preparation through printing and sintering.
Related Content
-
7 Things We Saw at Formnext 2024 — Video Playlist
There were countless processes, applications and announcements at Formnext 2024. Here are seven standouts Peter Zelinski and Stephanie Hendrixson caught on film.
-
Video: Multimodal Powders for Metal 3D Printing
Rather than uniform particle diameters, multimodal powders combine particles of different sizes. In this video, how and why Uniformity Labs produces multimodal metal powders for additive manufacturing.
-
Binder Jetting Vs. Metal Injection Molding: The Cool Parts Show All Access
Alpha Precision Group, provider of both processes, discusses considerations that go into making this choice.