Thermwood Releases ‘Why LSAM’ Video for Large-Part Production
Video focuses on large-scale additive manufacturing systems (LSAM) for thermoplastic composite large-part production.
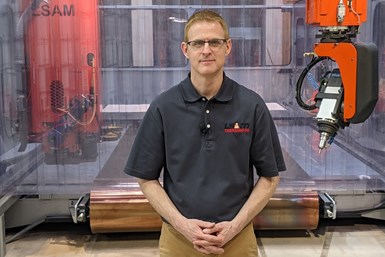
Scott Vaal, Thermwood’s LSAM product manager, addresses the question of “Why LSAM?”
Thermwood Corp. recently released a video focused on why companies should consider its large-scale additive manufacturing systems (LSAM) for thermoplastic composite large-part production. In the video, Scott Vaal, Thermwood’s LSAM product manager, addresses the question of “Why LSAM?”
Vaal focuses on key aspects of the large-scale additive manufacturing (AM) market and LSAM’s position in it. This video also covers the current state-of-the-art technology in additive printing, including a quick overview of the broad LSAM product line, slicing software, industry collaboration, additive system reliability, service, support and upgradability. He also highlights other issues which may be important to potential users and anyone interested in large-scale AM of thermoplastic composites.
According to the company, Thermwood has found that some companies exploring large-scale AM don’t have a clear understanding of the current state of the market, the available technology or the capabilities of currently available systems. The video is designed to increase the level of understanding, comfort and confidence that capable, proven and reliable large-scale additive systems are not only available but are already successfully operating in major industries every day, generating significant benefits and profits.
Thermwood is a U.S.-based, multinational, diversified machinery manufacturer offering large-scale AM of thermoplastic composite molds, tooling, patterns and parts with its line of LSAM that both 3D print and trim on the same machine. These manufacturing systems are said to be well suited for a variety of markets, including aerospace, marine, automotive and foundry industries as well as military, government and defense contractors.
Related Content
-
Louisville Slugger Uses Formlabs Technology to Accelerate Innovation
Louisville Slugger relies on Formlabs’ Form 3 stereolithography 3D printer to create both prototypes and manufacturing aids for designs of the composite and aluminum bats swung by youth and collegiate players.
-
Aircraft Ducts 3D Printed in Composite Instead of Metal: The Cool Parts Show #68
Eaton’s new reinforced PEKK, tailored to aircraft applications, provides a cheaper and faster way to make ducts compared to formed aluminum.
-
Evaluating the Printability and Mechanical Properties of LFAM Regrind
A study conducted by SABIC and Local Motors identified potential for the reuse of scrap reinforced polymer from large-format additive manufacturing. As this method increases in popularity, sustainable practices for recycling excess materials is a burgeoning concern.