Sculpteo Redesigns Lumbar Support Belt to Enhance Environment Awareness for the Blind
The choice of the 3D printed flexible material considerably improves user comfort, while also simplifying the production process.
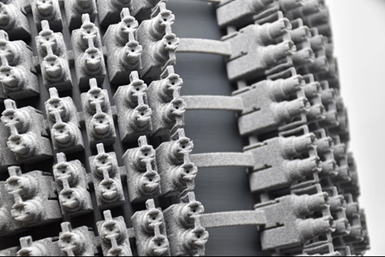
Sculpteo’s redesign of the lumbar belt improves user comfort, durability and design, as well as reducing production time. Photo Credit: Sculpteo
Sculpteo is partnering with Artha France to develop and 3D print lumbar belts that include a camera linked in real time to belt-mounted actuators, enabling people with visual impairments to perceive their environment. Artha France is a startup offering new autonomy to the visually impaired and blind by offering a tactile technology that reproduces the perception of the environment.
By redesigning the hinges from a multipart design to a single piece printed in one go with Multi Jet Fusion (MJF) Ultrasint TPU 01, Sculpteo has enabled Artha France to improve user comfort, durability and design, as well as considerably reduce production time.
The companies say this metamorphosis is a testament to their shared commitment to improve existing solutions, placing innovation at the service of inclusion.
Belt Capable of Expressing Sight Through Sensory Experience
Founded in 2018 in the Paris area, Artha France says it is developing a revolutionary device that enables its users to feel the topography of the environment through touch. Consisting of a camera attached to an eyeglass temple which is linked to a lumbar belt, the device enables the visually impaired to use a computer, offering extended possibilities.Artha France’s aim is to unleash the potential of the visually impaired by offering them a unique sensory experience and facilitating their active participation in a variety of activities.
New Flexible Material for Lumbar Belts Suitable for Every User
Because of Sculpteo’s expertise in 3D printing, Artha France was able to transcend the initial design limitations of its lumbar belt. Sculpteo redesigned the hinges, moving from a multipart design to a single piece, printed in one go with the MJF Ultrasint TPU 01. The choice of this flexible material has considerably improved user comfort, while simplifying the production process. Sculpteo’s efficiency, combined with the high quality of 3D printing, enabled Artha France to speed up the development of its device. It demonstrates the benefits of 3D printing in the production of complex challenges of innovative device designs. The collaboration between Artha France and Sculpteo has brought significant advances in the field of assistance for the visually impaired.
“Sculpteo’s expertise in 3D printing, combined with their commitment to understand our specific needs, helped turn our vision into a reality,” says Rémi du Chalard, Artha France CEO. “Sculpteo played an essential role in the improvement of our design, reinforcing our commitment to the autonomy of the visually impaired. Their dedicated team made our project a success story, and we are grateful for the positive impact their collaboration has had on our mission.”
Sculpteo offers an online 3D printing service with an online platform to securely upload 3D files and select from 75-plus materials and finishing options. “Working with Artha France to rethink and improve their device for the visually impaired has been a thrilling adventure,” says Alexandre d’Orsetti, Sculpteo CEO. “The magic of 3D printing lies in its ability to transform ideas into concrete objects, and this collaboration is a perfect example of this.”
Based in Paris and San Francisco, Sculpteo offers on-demand 3D printing and manufacturing at a large scale for startups, SMEs and design studios. Sculpteo offers its professional 3D printing service alongside its expert Design Studio to help businesses integrate additive manufacturing into their product development and production systems.
- Learn more about Sculpteo with its RE-cycleo 3D printed part recycling program. The program offers recycling services to Sculpteo clients not only for the clients’ obsolete parts but also for production scrap.
Related Content
What Does Additive Manufacturing Readiness Look Like?
The promise of distributed manufacturing is alluring, but to get there AM first needs to master scale production. GKN Additive’s Michigan facility illustrates what the journey might look like.
Read More6 Trends in Additive Manufacturing Technology at IMTS 2024
3D printers are getting bigger, faster and smarter. But don’t overlook the other equipment that the AM workflow requires, nor the value of finding the right supplier.
Read More3D Printed Spine Implants Made From PEEK Now in Production
Medical device manufacturer Curiteva is producing two families of spinal implants using a proprietary process for 3D printing porous polyether ether ketone (PEEK).
Read MoreThis Drone Bird with 3D Printed Parts Mimics a Peregrine Falcon: The Cool Parts Show #66
The Drone Bird Company has developed aircraft that mimic birds of prey to scare off problem birds. The drones feature 3D printed fuselages made by Parts on Demand from ALM materials.
Read MoreRead Next
Crushable Lattices: The Lightweight Structures That Will Protect an Interplanetary Payload
NASA uses laser powder bed fusion plus chemical etching to create the lattice forms engineered to keep Mars rocks safe during a crash landing on Earth.
Read MoreBike Manufacturer Uses Additive Manufacturing to Create Lighter, More Complex, Customized Parts
Titanium bike frame manufacturer Hanglun Technology mixes precision casting with 3D printing to create bikes that offer increased speed and reduced turbulence during long-distance rides, offering a smoother, faster and more efficient cycling experience.
Read More3D Printed Polymer EOAT Increases Safety of Cobots
Contract manufacturer Anubis 3D applies polymer 3D printing processes to manufacture cobot tooling that is lightweight, smooth and safer for human interaction.
Read More