Researchers 3D Print Customized Sensors with Integrated Electronics
Inductive proximity sensors come in cylindrical metal casings in which a coil, circuit board and plug are installed in a fixed configuration and can be used for non-contact detection of metal objects.
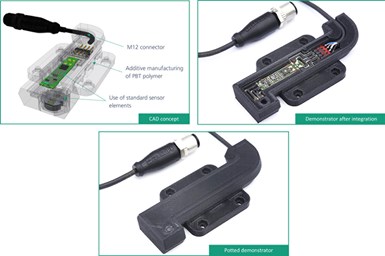
Demonstration model of customized sensor at different production stages: CAD concept (top left), after integration of the electronic components (top right) and as a finished demonstration model (bottom).
Researchers at the Center for Additive Production at the Fraunhofer Institute for Manufacturing Engineering and Automation (IFAM) have successfully 3D printed customized sensors for the first time. The team was supported by colleagues from the plastics processing machine manufacturer Arburg GmbH & Co. KG and the sensor and automation company Balluff GmbH.
The “Electronic Function Integration in Additively Manufactured Components” research project ran for 18 months, led by Stefan Pfeffer. The research involved printing the sensor casing in plastic so that it could be manufactured in any shape. A plastic with high dielectric strength and flame-retardant properties was required for the sensor casing. The team opted for semi-crystalline plastic polybutylene terephthalate (PBT), which is used as standard injection molding material for the production of electronic casings. However, this type of material had not yet been used for 3D printing.
The plastic was fed in granulate form into Arburg‘s “freeformer” industrial additive manufacturing (AM) system, which uses a material preparation unit with a special plasticizing screw. After melting the standard granulate, the freeforming process (which uses no molds) followed. A high-frequency nozzle closure discharged tiny plastic droplets, which could be precisely positioned with the aid of a movable part carrier.
This enabled the freeformer to create three-dimensional components with cavities layer by layer, into which components could be inserted during the printing process. To make this possible, the freeformer automatically interrupted the process at each respective layer, so that the coil, circuit board and plug could be precisely integrated. In a separate process, a dispenser was then used to produce the silver conductor tracks inside the casing. To complete the process, all that was needed was to overprint the cavities and then put them in polyurethane.
The team produced more than 30 demonstration models of customized sensors and tested them. The components had to be able to withstand temperature changes and vibrations, be waterproof and pass an electrical insulation test. By optimizing the design and manufacturing process, the tests were ultimately completed successfully.
Related Content
-
Semiconductors, Tungsten, AM Affordability and More from Formnext 2024: AM Radio #56
The trade show included increased applications for the semiconductor market, machine launches and technology advances aimed at cost cutting, plenty of LFAM and more. Listen to our conversation on Formnext 2024.
-
EOS Launches Digital Foam Architects Network
EOS created the collaborative additive manufacturing alliance to accelerate time-to-market for 3D printed foam applications.
-
Bike Manufacturer Uses Additive Manufacturing to Create Lighter, More Complex, Customized Parts
Titanium bike frame manufacturer Hanglun Technology mixes precision casting with 3D printing to create bikes that offer increased speed and reduced turbulence during long-distance rides, offering a smoother, faster and more efficient cycling experience.