Metal 3D-Printed Implants Are Helping Injured Racehorses
A successful collaboration between Clinique de Grosbois and French service bureau 3D Medical is driving positive outcomes in equine medicine with the development of a new type of prosthesis that improves healing.
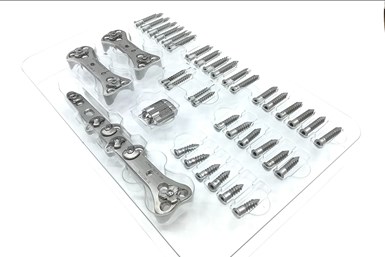
Metal 3D printing has enabled the development of a new type of prosthesis that improves healing and will hopefully positively improve the outcome for injured racehorses. Photo Credit: 3D Medical
A collaboration between Clinique de Grosbois and French service bureau 3D Medical is driving positive outcomes in equine medicine with their neck generation innovation involving metal 3D-printed implants to help injured racehorses.
Neck and vertebral fractures caused by falls at high speed are some of the most common causes of injury in racehorses. Equine veterinary surgeon Dr. Fabrice Rossignol and his team at the Clinique de Grosbois, located southeast of Paris, France, have been exploring the potential of metal 3D printing implants for treating neck fracture cases.
In the past, it was not uncommon for horses with neck fractures to be euthanized, sometimes within hours. It is difficult, especially with open fractures, to rehabilitate the animal because racehorses are not animals that can lie down for months, and immobilizing them is almost impossible. Additionally, the cost of an operation and subsequent convalescence is often very high, which unfortunately affects the decision of some owners.
Given some of the technical restrictions of using conventionally manufactured implants, Dr. Rossignol and his colleagues began exploring the potential of using metal 3D printing within equine medicine for neck fracture cases. “We’ve ended up with a new type of prosthesis that improves healing and hopefully will positively improve the outcome for as many animals as possible,” says Vincent Nuttens, 3D Medical CEO.
During surgery, the injured horse is anesthetized and placed in a surgical hammock to immobilize it. The fracture is stabilized with a 3D-printed plate and 3D-printed cancellous screws bridging the vertebrae (depending on the case and the vertebrae affected) with a small 3D-printed titanium cage applied in the ventral disc space. Cancellous or cortical screws may sometimes be associated with the locked screws to enable compression of the fractured fragment.
The company says the benefit of this assembly lies in that the 3D-printed titanium intervertebral spacer used during surgery makes use of compression forces to preserve the spacing between the vertebrae. The shape of the plate enables the placement of three screws in each vertebra. In addition, the company says implants manufactured using titanium alloys have shown better osseointegration than steel implants. And, unlike conventional machining, metal 3D printing enables the creation of porous patterns that facilitate the growth of bone through the cage and the fixation of the bone onto the cage.
Finally, the screws used are self-tapping and partially self-drilling, which enables maximum anchorage , while reducing the risk of perforation during drilling or tapping. “The three major features and benefits of the metal 3D implant are its precision of custom printing and its resistance to a force and weight (a horse’s weight is significantly greater than a human’s), as well as the postoperative mobility of the animal,” Rossignol says.
The procedure is performed under radiographic or fluoroscopic control and, so far, few complications have been noted, the company says.
In the postoperative period, the horses are left free in the stall for one month. Then, they are gradually rehabilitated by hand walking, with a walker and in the paddock, until they are gradually returned to activity (between the fifth and eighth month) after a clinical and radiographic test.
“Metal 3D printing allows us to be inventive, which gives us very encouraging long-term (care) of our four-legged companions,” Nuttens adds.
Related Content
3D Printed Spine Implants Made From PEEK Now in Production
Medical device manufacturer Curiteva is producing two families of spinal implants using a proprietary process for 3D printing porous polyether ether ketone (PEEK).
Read MoreDMG MORI: Build Plate “Pucks” Cut Postprocessing Time by 80%
For spinal implants and other small 3D printed parts made through laser powder bed fusion, separate clampable units resting within the build plate provide for easy transfer to a CNC lathe.
Read MoreUnderstanding PEKK and PEEK for 3D Printing: The Cool Parts Show Bonus
Both materials offer properties desirable for medical implants, among other applications. In this bonus episode, hear more from Oxford Performance Materials and Curiteva about how these companies are applying PEKK and PEEK, respectively.
Read MoreMore Affordable Suture Anchors 3D Printed from PEKK: The Cool Parts Show #60
Selective laser sintering (SLS) of polyether ketone ketone (PEKK) is being used to produce medical implants that are more cost effective and perform better than their conventional counterparts. We highlight fasteners known as suture anchors in this episode of The Cool Parts Show.
Read MoreRead Next
3D Printed Polymer EOAT Increases Safety of Cobots
Contract manufacturer Anubis 3D applies polymer 3D printing processes to manufacture cobot tooling that is lightweight, smooth and safer for human interaction.
Read MoreCrushable Lattices: The Lightweight Structures That Will Protect an Interplanetary Payload
NASA uses laser powder bed fusion plus chemical etching to create the lattice forms engineered to keep Mars rocks safe during a crash landing on Earth.
Read MorePostprocessing Steps and Costs for Metal 3D Printing
When your metal part is done 3D printing, you just pull it out of the machine and start using it, right? Not exactly.
Read More