Linde, EOS Collaborate on Study for Gas Interaction on Aluminium Alloy
The team said it utilized Linde’s ADDvance O2 precision techology to achieve continuous, exacting analysis of the gas atmosphere for the study results.
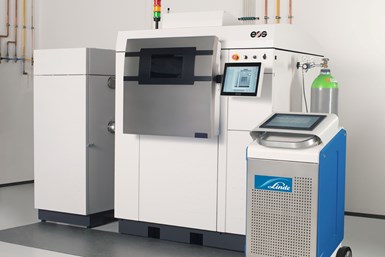
The study team utilized EOS’ M 290 system and Linde’s ADDvance O2 precision oxygen monitoring technology.
Linde, an industrial gases company, and EOS, a supplier of responsible manufacturing solutions via industrial 3D printing technology, collaborated on a study into the influence of oxygen in the print process chamber and its effect on the critical properties of aluminium alloy AlSi10Mg.
The companies say the results of the 2020 study are fundamental to advancing optimal, repeatable and reliable printing of an alloy widely used across multiple industries. EOS’ DMLS building process usually takes place under an argon or nitrogen atmosphere, established by purging high purity gas into the build chamber, which then replaces the relative ratio of ambient air until reaching an oxygen concentration below 1,000 ppm.
Even after rigorous purging of the print chamber atmosphere, it is possible for minor impurities to still remain present, the companies say. Extremely small variations in oxygen levels can impact the mechanical properties of alloys which are sensitive to oxygen, including process-induced aging of the metal powder.
As part of the Linde-EOS investigation into gas interaction with EOS Aluminium AlSi10Mg powder, Linde’s additive manufacturing (AM) oxygen monitoring technology — ADDvance O2 precision — was selected to provide continuous analysis of the gas atmosphere. Recognizing O2 concentrations as low as 10 ppm, ADDvance O2 precision initiates an automatic purging process to maintain optimal atmospheric conditions.
“For EOS, a consistent and reliable gas atmosphere, as well as accuracy of oxygen gas readings, is vital for us because it is vital for our customers,” says Dr. Astrid Rota, head of metal process technology, EOS. “Some industries require not only the most advanced printing systems generating best material quality but also need to record highly detailed data which is where the ADDvance O2 precision really delivers.”
The study team concluded that the EOS M 290 with the EOS Aluminium AlSi10Mg powder and process parameters enable a high-quality, reproducible final part. For more information, read the full study results.
Related Content
-
Additive Manufacturing Is Subtractive, Too: How CNC Machining Integrates With AM (Includes Video)
For Keselowski Advanced Manufacturing, succeeding with laser powder bed fusion as a production process means developing a machine shop that is responsive to, and moves at the pacing of, metal 3D printing.
-
With Electrochemical Additive Manufacturing (ECAM), Cooling Technology Is Advancing by Degrees
San Diego-based Fabric8Labs is applying electroplating chemistries and DLP-style machines to 3D print cold plates for the semiconductor industry in pure copper. These complex geometries combined with the rise of liquid cooling systems promise significant improvements for thermal management.
-
This Year I Have Seen a Lot of AM for the Military — What Is Going On?
Audience members have similar questions. What is the Department of Defense’s interest in making hardware via 3D printing over conventional methods? Here are three manufacturing concerns that are particular to the military.