HP, Legor Collaborate on Specialty Precious Metals for Jewelry Markets
The initial collaboration will focus on enabling the production of functional stainless steel accessories for the jewelry and fashion markets, while also implementing an R&D program to parameterize and characterize bronze and silver powders, and eventually gold powders.
Share
Read Next
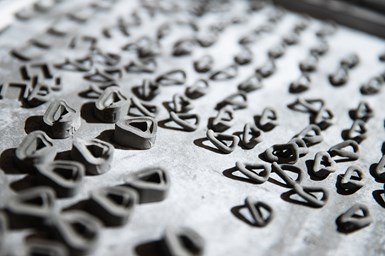
Photo Credit: Legor
HP Inc. and Legor Group SPA are collaborating on the development of precious metal materials for use with HP’s Metal Jet system to produce functional stainless steel accessories for the jewelry and fashion markets.
Legor is a provider of metals science, including the development of alloys, powders and plating solutions. According to the company, it is the first to produce specialty precious metal materials for the jewelry and fashion accessories markets designed to work with HP’s 3D metal binder jet platform.
“Our vision for additive manufacturing (AM) goes beyond small series and prototyping,” says Massimo Poliero, president & CEO of Legor Group SPA. “We see a future where every modern business will have one or more of HP’s state-of-the-art binder jetting printers in its facilities, enabled by Legor’s technology, design and support to reduce the time to market for both precious and nonprecious metal parts. This strategic partnership with HP is the keystone to accelerate this vision and move the industry toward more sustainable manufacturing.”
The partnership is focused on enhancing the speed, quality and economic advantages delivered by HP Metal Jet which is said to enable a rapid path to serial production of 3D-printed metal parts.
“Our work with Legor aligns perfectly with HP’s vision to disrupt manufacturing norms, accelerate digital manufacturing and sustainable impact for customers around the world,” says Didier Deltort, president, HP personalization and 3D printing.
The collaboration will initially focus on enabling the production of functional stainless steel accessories for the jewelry and fashion markets. In parallel, the companies say they will implement a rigorous R&D program to parameterize and characterize bronze and silver powders, and eventually gold powders, the core material in the precious sector. HP and Legor will work to optimize the printing and sintering parameters for these new materials and the surface finish results. Research will take place in the new Legor 3DMetalHub in Bressanvido, Italy, a center of excellence focused on accelerating AM for the luxury industry.
In addition, working closely with HP, Legor is creating opportunities for its customers to take advantage of the cost, quality and productivity benefits of HP Metal Jet, and helping them integrate sustainable manufacturing into their businesses. The advantages of HP Metal Jet is said to enable Legor to transform product manufacturing on behalf of customers in the precious sectors and beyond. Along with design freedom, production flexibility and lowering development costs, HP Metal Jet is said to enable customers to economically manufacture high-quality metal parts at scale.
“The digital capabilities of HP Metal Jet provides an alternative method to the classic investment casting which requires the combustion of waxes or resins and the use of gypsum (calcium sulphate) as casting material, containing free breathable silica,” Poliero says. “It is our way to promote more robust and intentional sustainability into production processes.”
Related Content
-
Beehive Industries Is Going Big on Small-Scale Engines Made Through Additive Manufacturing
Backed by decades of experience in both aviation and additive, the company is now laser-focused on a single goal: developing, proving and scaling production of engines providing 5,000 lbs of thrust or less.
-
ActivArmor Casts and Splints Are Shifting to Point-of-Care 3D Printing
ActivArmor offers individualized, 3D printed casts and splints for various diagnoses. The company is in the process of shifting to point-of-care printing and aims to promote positive healing outcomes and improved hygienics with customized support devices.
-
Two 12-Laser AM Machines at Collins Aerospace: Here Is How They Are Being Used
With this additive manufacturing capacity, one room of the Collins Iowa facility performs the work previously requiring a supply chain. Production yield will nearly double, and lead times will be more than 80% shorter.