Fabrisonic Earns IS0 9001:2015 Certification
The scope of the registration for ISO 9001 covers UAM products, equipment and R & D service.
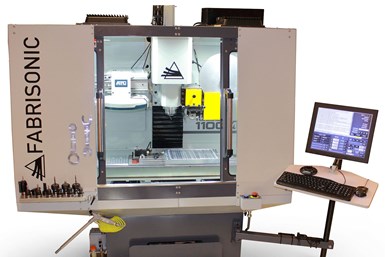
The Fabrisonic SonicLayer 1200 features a hybrid additive and subtractive process.
Fabrisonic, a manufacturer specializing in metal 3D printing applications, has achieved ISO 9001:2015 certification, an internationally recognized quality standard. The certification further validates its quality management system which the company says is focused on the customer, continuous improvement and risk-based thinking so that quality problems can be prevented. Fabrisonic is commercializing ultrasonic additive manufacturing (UAM), a 3D metal printing process which joins thin metal foils to produce a three-dimensional product.
The scope of the registration for ISO 9001 covers UAM products, equipment and R & D service. The journey toward ISO certification has enabled Fabrisonic to further hone existing continuous improvement efforts, the company says. One unique aspect of Fabrisonic’s ISO scope is the system did not just address production. Unlike many companies, Fabrisonic chose to incorporate its research and development efforts in its scope.
“UAM is a new and exciting process, and as a result much of the commercial efforts centers on first of its kind applications,” says Mark Norfolk, Fabrisonic president. “We think it is important that all our production is covered by our quality system. It’s the way we do business.”
In 2020, Fabrisonic experienced strong growth and won Oak Ridge National Laboratory’s Small Business of the Year award. Its quality system, bolstered by the addition the recent ISO 9001 certification, is said to further enhance its ability to serve its customers, continue to improve and impact future growth.
Related Content
-
EOS Helps Strengthen Indiana Tech's STEM Program
Indiana Tech acquires second EOS additive manufacturing system as part of a $21.5 million expansion of its Zollner Engineering Center and STEM educational programming.
-
DMG MORI, Illinois Tech to Establish National Center for Advanced Manufacturing in Chicago
The center will focus on workforce training for additive manufacturing and related advanced manufacturing industries.
-
EOS Additive Minds Academy Opens Space for Hands-On AM Training
The engineering, consulting and education arm of EOS has offered training in various capacities before now, but a new physical footprint at the company’s Novi, Michigan, facility will make AM training more accessible and affordable.