EOS Conducts Sustainability Study for Eyewear Frames
Study results indicate 3D printed glasses have a higher wearing comfort, are more stable and sustainable than any other glasses.
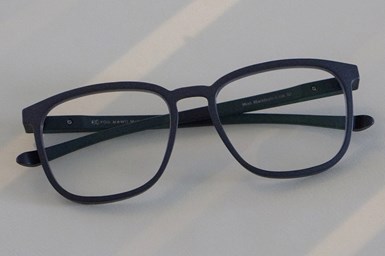
3D printed You Mawo eyewear frame. Photo Credit: You Mawo
EOS partnered with its customer You Mawo and Fraunhofer EMI to conduct a systemic life cycle analysis (LCA) for You Mawo’s 3D printed glasses. From cradle-to-grave, excluding the use phase, the study compares the environmental impact of additively and conventionally manufactured eyewear, covering the life cycle from material sourcing to production, packaging and shipping. The study also included a hotspot analysis to identify major contributors and potential for improvement, including powder refresh rates, powder feedstock and energy sources used.
The study concluded that additively manufactured eyewear has a lower carbon footprint. The 3D printed eyewear performed significantly better than the conventional eyewear in all 18 impact categories, such as climate change, human toxicity, ozone depletion and water depletion. For example, according to the study, the carbon footprint of a customized, 3D printed You Mawo eyewear product is around 58% lower compared to conventionally manufactured eyewear. The analysis also concluded that 3D printed eyewear compared to conventionally manufactured acetate eyewear creates 80% less waste and can help avoid lengthy postprocessing.
While all You Mawo locations are powered with renewable energies, the study revealed more potential for improvement, such as a further reduction in the powder refresh rate, further development of powders with a lower footprint (for example, bio-based) and less expensive packaging.
Altogether, the 3D printing-based eyewear frame production offered by You Mawo — based on EOS technology — produces three times less CO2 emissions than a traditionally produced pair of glasses.
“We are shaping the future of responsible manufacturing,” says Björn Hannappel, head of sustainability at EOS. “Our goal and purpose are to combine pioneering digital innovation in industrial 3D printing and sustainable practices.”
As the technology enables the design and manufacturing of highly individualized eyewear, it also helps manufacturers avoid overproduction, minimize supply chains and enable on demand production. “The EOS technology convinced us as it meets our high-quality, low scrap rate criteria,” says Sebastian Zenetti, managing director and head of sales at You Mawo. “It supports our strive for sustainable production and products.”
Related Content
-
3D Printing Brings Sustainability, Accessibility to Glass Manufacturing
Australian startup Maple Glass Printing has developed a process for extruding glass into artwork, lab implements and architectural elements. Along the way, the company has also found more efficient ways of recycling this material.
-
Video: A Mechanical Method for Metal Powder Production
Metal Powder Works has developed a method for producing powders from solid barstock, no melting required. This video covers how the process works and benefits of mechanical production of powders.
-
Video: AM for Repair of Large Shafts
Wind power shafts that might once have been scrapped are now returned to service. See the robotic directed energy deposition (DED) and shaft preheating system developed by Ikergune, Izadi and Talens.