Desktop Metal Qualifies Pure Copper for Additive Manufacturing
Production System binder jetting technology is said to enable the mass production of high-performance copper parts for automotive, aerospace and electronics.
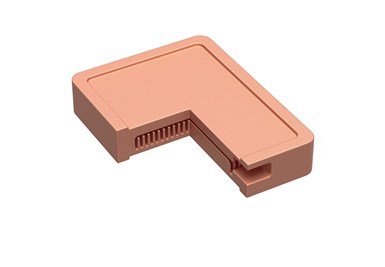
Copper liquid cooling plate cutaway view. Photo Credit: Desktop Metal
Desktop Metal has qualified commercially pure copper (> 99.95% purity) for additive manufacturing (AM) on its Production System platform, which leverages single pass jetting (SPJ) technology which is designed to achieve the fastest build speeds in the metal AM industry. The company says customers can now leverage SPJ technology for the production of high-performance copper parts at scale across a broad variety of industries, including automotive, aerospace, and electronics.
With its excellent thermal and electrical conductivity, it is said commercially pure copper is a well-suited material for applications requiring heat or electricity transfer, such as cold plates, pucks and manifolds, heat sinks, heat exchangers and bus bars used in power-intensive electrical applications. It is the third most consumed industrial metal in the world.
“Copper has been a highly requested material from many of our customers and prospects, and has applications spanning a broad variety of industries, from thermal hardware found in air and liquid cooling systems to conformally cooled coils for transmission of high frequency currents,” says Jonah Myerberg, co-founder and CTO of Desktop Metal. “We are excited to be able to expand our extensive Production System materials portfolio to support customers looking to 3D print electrically and thermally conductive components at scale and at a fraction of the cost of conventional manufacturing methods.”
Desktop Metal’s materials science team has qualified and fully characterized commercially pure copper (C10300) printed on Production System technology with greater than 99.95% purity, which is said to enable excellent thermal and electrical conductivity. Manufacturers can now print copper parts on the Production System with significant geometric complexity in a single step instead of brazing multiple conventionally produced copper components together, eliminating a time-intensive and expensive process prone to error and waste. With the geometric freedom enabled by binder jetting, engineers can also explore new, high-performance designs not possible with conventional manufacturing methods, such as the lattice structures and conformal cooling channels to improve heat transfer.
Related Content
-
3D Printed NASA Thrust Chamber Assembly Combines Two Metal Processes: The Cool Parts Show #71
Laser powder bed fusion and directed energy deposition combine for an integrated multimetal rocket propulsion system that will save cost and time for NASA. The Cool Parts Show visits NASA’s Marshall Space Flight Center.
-
“Mantis” AM System for Spacecraft Uses Induction for Deposition
The metal 3D printing system melts wire without lasers. 30-foot-diameter parts are built on a rotary-feed system that eliminates the need for a large machine frame or gantry.
-
Additive Manufacturing Is Subtractive, Too: How CNC Machining Integrates With AM (Includes Video)
For Keselowski Advanced Manufacturing, succeeding with laser powder bed fusion as a production process means developing a machine shop that is responsive to, and moves at the pacing of, metal 3D printing.